In the intricate machinery of the industrial world, the oil hub seal stands as a critical component, often unsung yet fundamental to the seamless operation of countless machines and vehicles. This small but mighty part is designed to maintain the integrity of the lubrication system, preventing leaks and thus ensuring longevity and efficiency. The oil hub seal is pivotal in industries ranging from automotive to manufacturing, each relying on its robust functionality to avoid costly downtimes and repairs.
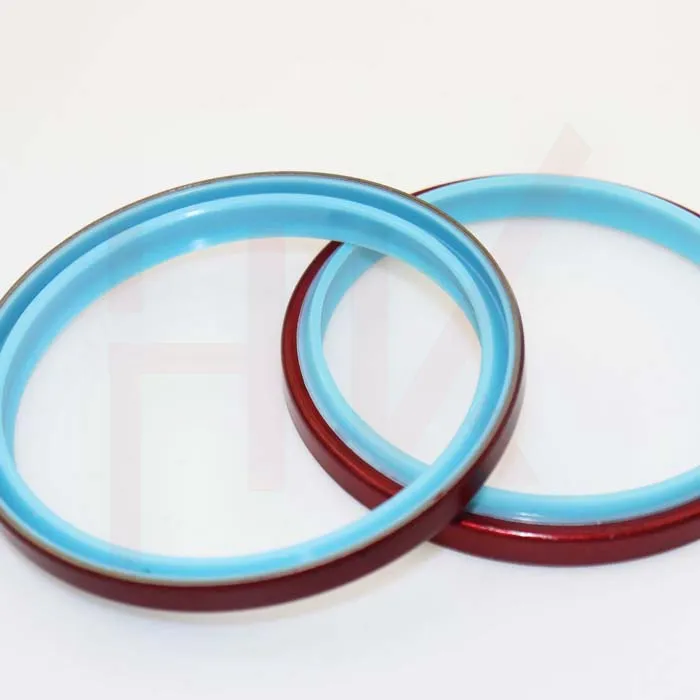
The importance of oil hub seals is deeply rooted in their ability to sustain optimal performance under pressure, effectively keeping lubricants intact and contaminants at bay. Such efficiencies contribute not only to the mechanical health of equipment but also to the economic and environmental sustainability by minimizing oil wastage and machine wear. A well-selected oil hub seal can significantly elongate the lifecycle of a piece of machinery, safeguarding investments and maintaining high levels of performance.
Expertise in selecting the correct oil hub seal is not merely a matter of choosing one with the right size or fit.
It requires an understanding of the specific operational environment in which the seal will function. Variations in temperature, exposure to chemicals, and degrees of mechanical load can all affect seal performance. Therefore, consulting with experts or manufacturers who have a profound understanding of the material composition and design suitable for particular applications is crucial. Professionals in this field emphasize the importance of considering factors like material toughness against thermal expansion or contraction and resistance against corrosive substances – a knowledge area where experience clearly takes precedence.
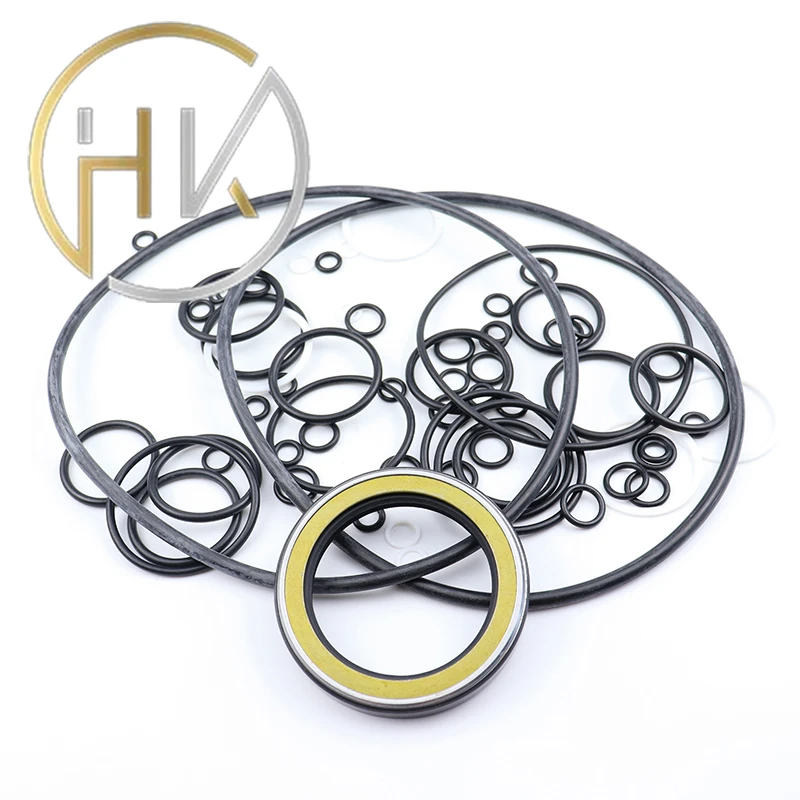
Manufacturers and suppliers of oil hub seals play a key role in not only providing high-quality products but also in advancing research and development for innovative seal technologies. The authoritative voice in this industry often comes from those companies that invest heavily in R&D, refining seal designs to enhance reliability and durability. Such firms are often at the forefront of adopting new materials, such as advanced polymers or composite structures, which offer enhanced sealing capabilities compared to traditional materials. Their contributions extend beyond product provision to include advising machinery operators on best practices in seal maintenance and replacement schedules to avert potential failures.
oil hub seal
Trust in oil hub seals also emanates from rigorous testing and certification processes. Reliable suppliers subject their products to stringent quality control checks, simulating real-world conditions to verify performance standards. Certifications from recognized bodies further endorse a seal's reliability, highlighting its suitability for specific industrial applications. As a trusted partner in machinery maintenance, an oil hub seal's credibility is established through consistent, verifiable performance data and reliable customer feedback.
End-users' experiences often provide invaluable insights into the everyday application of oil hub seals. Such accounts not only validate the theoretical claims made by manufacturers but also offer practical advice on maximizing seal performance. Real-world use cases, shared in forums or industry gatherings, contribute to a collective knowledge base, enhancing collective understanding and often sparking further innovations.
In conclusion, the oil hub seal's role transcends its apparent simplicity, embodying a confluence of engineering precision, material science, and practical ingenuity. Its impact is measured in operational continuity, cost savings, and environmental responsibility. As industries evolve, so too do the demands placed on these unassuming yet indispensable components, driving ongoing advancements and affirming the oil hub seal's place as a cornerstone of modern machinery reliability.