Oil Seal Technology A Comprehensive Guide
Oil seals are critical components in various mechanical systems, providing a vital barrier between the moving and stationary parts of an engine or machinery. These seals prevent oil leaks and maintain the integrity of the lubrication system, ensuring optimal performance and extending the life of the equipment. In this article, we will delve into the fundamentals of oil seal technology, including its types, materials, design considerations, and maintenance practices.
There are several types of oil seals available, each designed for specific applications and operating conditions. The most common types include lip seals, radial shaft seals, face seals, and metal bellows seals. Lip seals are simple, low-cost seals that consist of a flexible rubber or polymer lip that contacts the surface of the rotating shaft to create a seal. Radial shaft seals are more complex, featuring a metal case and a rubber or polymer sealing element that surrounds the shaft and prevents oil leakage. Face seals are similar to radial shaft seals but have a flat sealing surface that contacts the mating surface to create a seal. Metal bellows seals are used in high-pressure and high-temperature applications and consist of a flexible metal bellows that compensates for thermal expansion and movement.
The material selection for oil seals is crucial as it determines their performance, durability, and compatibility with various fluids. Common materials used in oil seals include nitrile rubber, fluoroelastomers, silicone rubber, and polytetrafluoroethylene (PTFE). Nitrile rubber is widely used due to its good chemical resistance, oil resistance, and moderate temperature range Nitrile rubber is widely used due to its good chemical resistance, oil resistance, and moderate temperature range
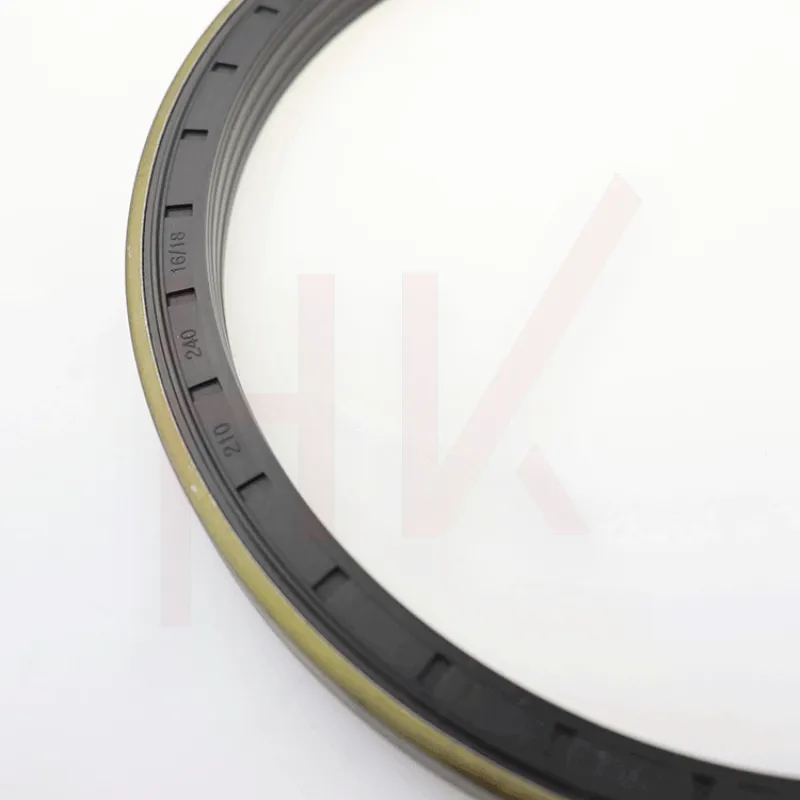
Nitrile rubber is widely used due to its good chemical resistance, oil resistance, and moderate temperature range Nitrile rubber is widely used due to its good chemical resistance, oil resistance, and moderate temperature range
oil seal tcn. Fluoroelastomers, such as Viton, offer excellent chemical and heat resistance but are more expensive. Silicone rubber is known for its flexibility and resistance to extreme temperatures, while PTFE is highly resistant to chemicals and has low friction coefficients.
Designing an oil seal involves considering several factors, including the type of seal, operating conditions, and the size and shape of the shaft or housing. It is essential to ensure that the seal provides an adequate seal under all operating conditions, including high pressures, speeds, and temperatures. Additionally, the seal must be designed to withstand the expected lifetime of the equipment without failure.
Proper maintenance is crucial for the longevity and performance of oil seals. Regular inspection and replacement of worn or damaged seals can prevent costly repairs and downtime. It is also important to ensure that the seal is properly installed and aligned to ensure optimal performance.
In conclusion, oil seal technology plays a vital role in maintaining the performance and longevity of mechanical systems. By understanding the different types of seals, materials, design considerations, and maintenance practices, engineers and maintenance personnel can select the appropriate seal for their application and ensure optimal performance and reliability.