The Pivotal Role of 70%, 90%, and 10% Oil Seal Ratios in Modern Engineering
In the intricate world of engineering, oil seals play an indispensable role in ensuring the efficient and safe operation of various machinery. These seals, often overlooked, are the silent guardians that prevent oil leaks and maintain optimal lubrication, thereby extending the lifespan of equipment. A critical aspect of oil seal selection lies in understanding the percentages - 70%, 90%, and 10%. These figures represent the balance between functionality, durability, and environmental impact.
The 70% component typically refers to the rubber compound used in the seal's construction. This elastomer is responsible for the seal's flexibility and resilience, allowing it to conform to the surface it contacts, creating a tight seal against oil leakage. It must possess excellent resistance to temperature fluctuations, chemicals, and wear, ensuring it can withstand harsh operating conditions over time. The choice of the right rubber compound is crucial, as it directly influences the seal's performance and longevity.
The 90% part signifies the sealing effectiveness. An ideal oil seal should ideally prevent 90% or more of the lubricant from escaping, while also preventing contaminants from entering the system. Advanced designs, such as labyrinth seals or double lip seals, enhance this percentage by creating multiple barriers, improving the seal's ability to protect the internal components from damage Advanced designs, such as labyrinth seals or double lip seals, enhance this percentage by creating multiple barriers, improving the seal's ability to protect the internal components from damage
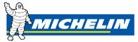
Advanced designs, such as labyrinth seals or double lip seals, enhance this percentage by creating multiple barriers, improving the seal's ability to protect the internal components from damage Advanced designs, such as labyrinth seals or double lip seals, enhance this percentage by creating multiple barriers, improving the seal's ability to protect the internal components from damage
70 90 10 oil seal.
Lastly, the 10% represents the environmental consideration. While oil seals are vital for machinery, they also have an ecological footprint. The production process, material choice, and end-of-life disposal all contribute to this percentage. Engineers strive to minimize this impact by using eco-friendly materials, designing seals that last longer, and promoting recycling programs for discarded seals.
In conclusion, the percentages 70%, 90%, and 10% encapsulate the essence of a high-quality oil seal. They denote the delicate balance between functionality, efficiency, and sustainability that every engineer aims to achieve. Whether it's a small engine or a massive industrial machine, these oil seals, with their intricate composition and design, ensure smooth operation and minimal environmental impact. Understanding and appreciating these percentages is crucial for making informed decisions in engineering, ultimately leading to more reliable and eco-conscious machinery.