Oil Seal The Crucial Component in Machinery Performance
In the realm of machinery and equipment, the oil seal serves as a critical component, ensuring smooth operation and extending the life of the system. This tiny yet indispensable device is designed to prevent the leakage of fluids, such as oil and grease, while allowing for the rotation of shafts or pistons.
The primary function of an oil seal is to create a barrier between two moving parts, one of which is usually stationary. It achieves this by utilizing a combination of materials, including rubber, plastic, metal, and fibrous materials, to form a tight seal. The design of the oil seal is crucial, as it must accommodate the dynamic movements of the shaft or piston without compromising its integrity.
One of the key factors that determine the effectiveness of an oil seal is its material composition. Rubber is a popular choice due to its ability to withstand high temperatures and pressures, making it suitable for use in a wide range of applications. However, other materials such asPTFE (polytetrafluoroethylene) and Viton are also used for their specific properties, such as chemical resistance and low friction.
Another important consideration when selecting an oil seal is its size and shape. The dimensions of the seal must be precisely tailored to fit the application, ensuring a snug fit that prevents leaks The dimensions of the seal must be precisely tailored to fit the application, ensuring a snug fit that prevents leaks
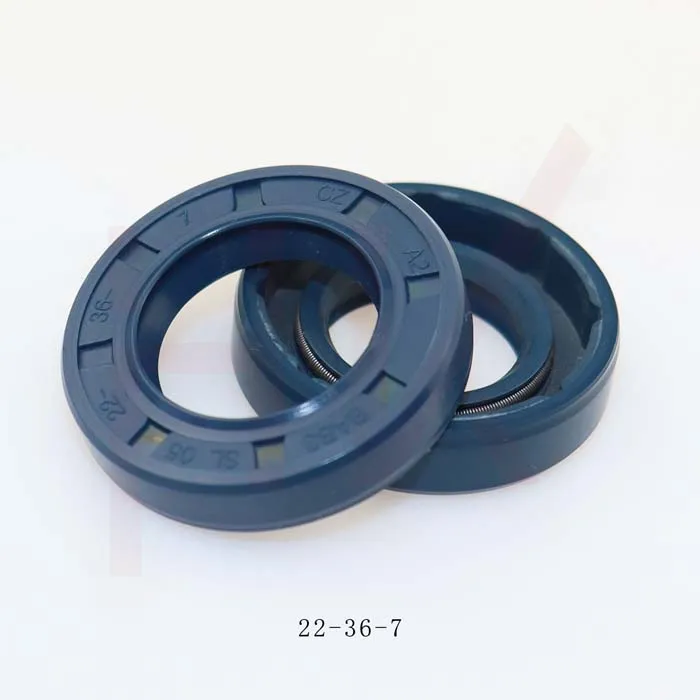
The dimensions of the seal must be precisely tailored to fit the application, ensuring a snug fit that prevents leaks The dimensions of the seal must be precisely tailored to fit the application, ensuring a snug fit that prevents leaks
20 35 7 oil seal. In addition, the shape of the seal can vary depending on the specific requirements of the machinery. For example, lip seals have a flexible lip that extends outward to create a seal, while shaft seals encircle the shaft and are secured in place with a retaining ring.
The maintenance of oil seals is also crucial to ensure optimal performance. Regular inspection and replacement are necessary to prevent wear and tear, which can lead to leaks and reduced efficiency. It is important to follow the manufacturer's recommendations for maintenance intervals and to use the correct tools and techniques when replacing the seals.
In conclusion, oil seals play a vital role in the proper functioning of machinery and equipment. By preventing fluid leaks and ensuring smooth operation, these tiny components help to extend the life of the system and reduce maintenance costs. With proper selection, installation, and maintenance, oil seals can provide reliable performance in a variety of industrial and automotive applications.