The Importance of Oil Seals for Motors A Comprehensive Overview
In the intricate machinery of modern technology, the motor stands as a vital component, driving numerous applications across various industries. Integral to the efficient functioning of motors is an often-overlooked but crucial element the oil seal. This article delves into the significance of oil seals in the context of motor operations, highlighting their function, types, and the critical role they play in ensuring optimal motor performance.
An oil seal, also known as a shaft seal or lip seal, serves as a barrier between the lubricating oil within a motor and the external environment. Its primary purpose is to prevent oil leakage while simultaneously blocking contaminants from entering the motor, thus maintaining cleanliness and preserving the oil's integrity. This dual functionality is crucial in extending the lifespan and efficiency of motors.
There are several types of oil seals, each designed to cater to specific motor requirements. The most common are radial shaft seals, which consist of a rubber lip that contacts the rotating shaft, creating a seal. Another type is the labyrinth seal, which utilizes a series of interlocking grooves to obstruct fluid flow. Additionally, mechanical seals, typically used in high-speed applications, employ spring-loaded faces to minimize leakage.
The selection of the right oil seal for a motor depends on factors such as operating conditions, temperature, pressure, and speed. For instance, in high-temperature environments, oil seals made of heat-resistant materials like silicone rubber or fluoroelastomers are preferred For instance, in high-temperature environments, oil seals made of heat-resistant materials like silicone rubber or fluoroelastomers are preferred
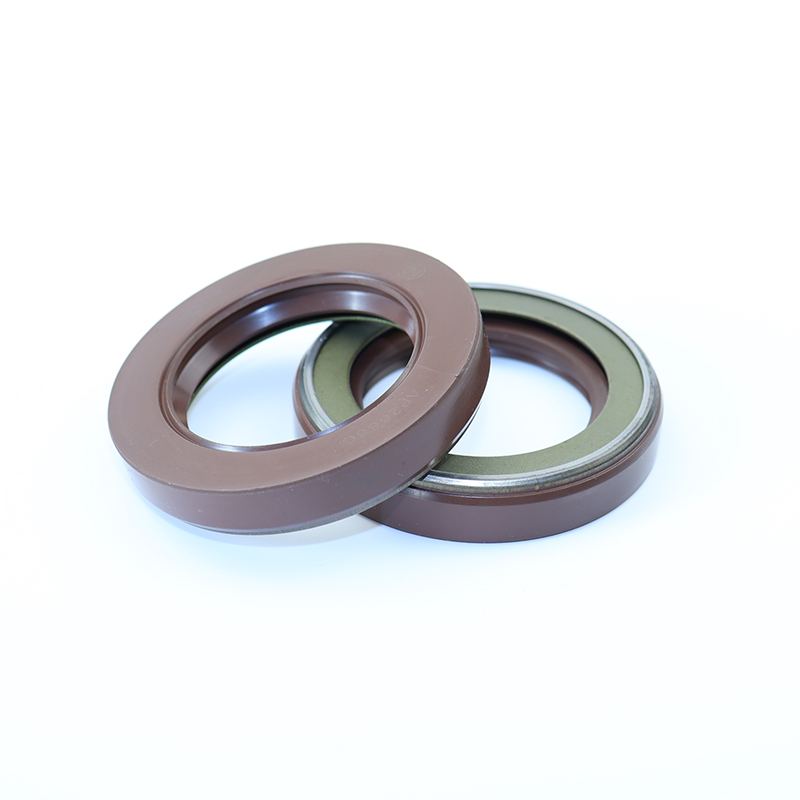
For instance, in high-temperature environments, oil seals made of heat-resistant materials like silicone rubber or fluoroelastomers are preferred For instance, in high-temperature environments, oil seals made of heat-resistant materials like silicone rubber or fluoroelastomers are preferred
oil seal for motor. Similarly, in applications involving harsh chemicals, oil seals with chemical resistance, like those made from Teflon, may be more suitable.
Beyond preventing oil leaks and ingress of contaminants, oil seals contribute significantly to energy conservation. By maintaining the integrity of the lubrication system, they ensure smooth and efficient motor operation, reducing friction and energy loss. Furthermore, they protect motor components from wear and tear, minimizing the need for frequent repairs and replacements.
However, it's important to note that oil seals, like any other mechanical part, are subject to wear over time. Regular inspection and timely replacement are necessary to prevent potential failures that could lead to motor damage or downtime.
In conclusion, oil seals for motors are more than just a simple component; they are a safeguard for the overall health and longevity of the motor. Their role in maintaining optimal performance, preventing leaks, and protecting against contaminants cannot be overstated. Understanding the importance of oil seals and selecting the appropriate one for a specific motor application is essential for ensuring reliable and efficient motor operation in today's fast-paced industrial landscape.