The Vital Role of Oil Seals in Machinery Performance
Oil seals play a crucial role in the performance and durability of machinery. These vital components prevent the leakage of oils, which are essential for lubricating and cooling various mechanical parts. By sealing these interfaces, oil seals help maintain the proper function of the machine and extend its service life.
Oil seals consist of a flexible lip or sealing ring made of rubber, synthetic materials, or metal, which is designed to create a tight seal between two dynamic surfaces, such as a rotating shaft and a stationary housing. The lip of the seal is typically pressed against the surface of the shaft by a spring or other external force, creating a seal that prevents the escape of fluids.
The effectiveness of an oil seal depends on several factors, including the choice of material, design, and installation. For example, high-quality elastomers such as Buna-N, PTFE, and Viton are known for their resistance to heat, chemicals, and wear. The shape and design of the seal, such as the lip profile and the use of hydrodynamic features, can also significantly impact its performance. Proper installation techniques, including cleaning the surfaces to be sealed and ensuring that the seal is correctly aligned and seated, are critical for long-term functionality.
In addition to preventing leaks, oil seals also help to retain important lubricants within the machine, improving its efficiency and reducing wear on moving parts
In addition to preventing leaks, oil seals also help to retain important lubricants within the machine, improving its efficiency and reducing wear on moving parts
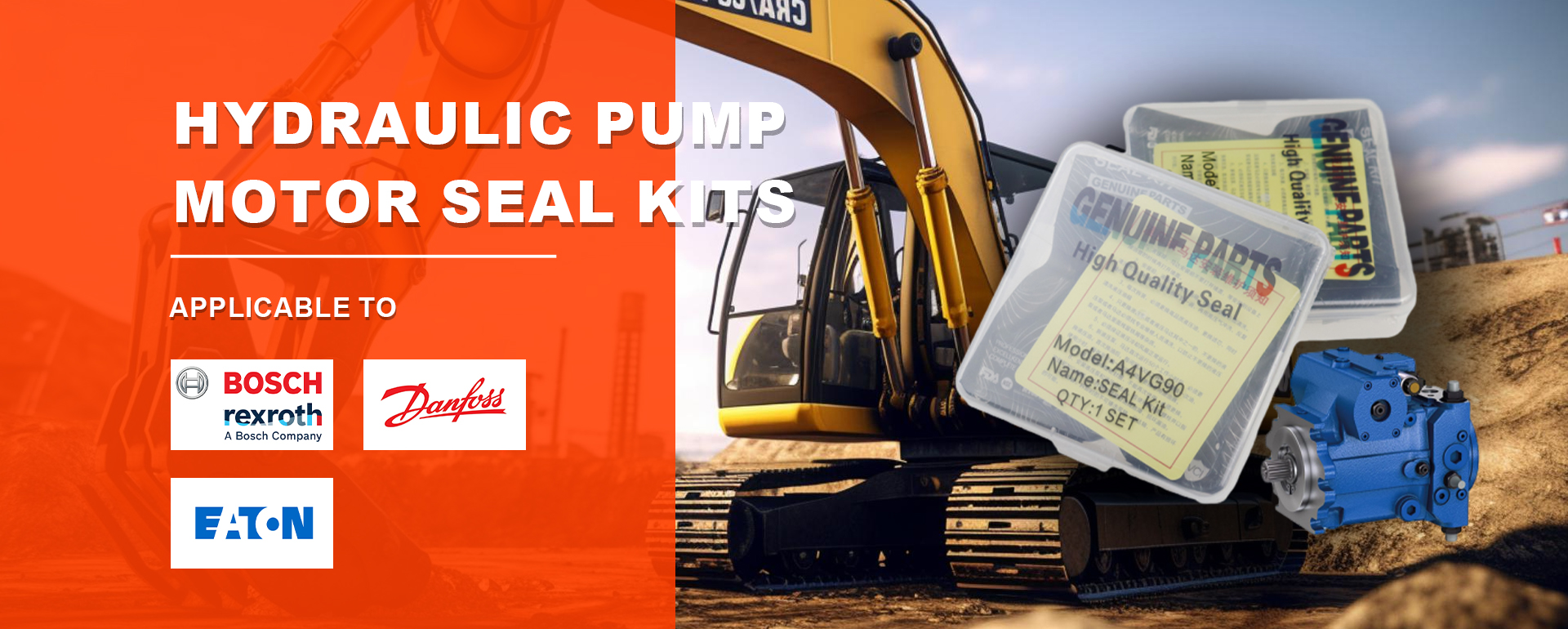
In addition to preventing leaks, oil seals also help to retain important lubricants within the machine, improving its efficiency and reducing wear on moving parts
In addition to preventing leaks, oil seals also help to retain important lubricants within the machine, improving its efficiency and reducing wear on moving parts
38x52x7 oil seal. When oil seals fail, they can result in costly repairs, downtime, and reduced productivity. Therefore, it is essential to regularly inspect and replace worn or damaged seals to ensure optimal machine performance.
To further enhance the effectiveness of oil seals, manufacturers are constantly researching and developing new materials and designs that offer improved durability, temperature resistance, and chemical compatibility. With continuous innovation, these vital components will continue to play a key role in the operation of machinery across various industries.
Overall, oil seals are a critical element in maintaining the performance and longevity of machinery. By preventing the leakage of fluids and retaining important lubricants, these components contribute to the efficient and reliable operation of many types of equipment. With ongoing advances in technology and materials science, we can expect to see even more advanced and effective oil seal designs in the future.