Oil Seal The Essential Component in Machinery Performance
In the realm of machinery and equipment, a seemingly small yet crucial component is the oil seal. This vital part plays a significant role in maintaining the integrity and efficiency of various mechanical systems. From automobiles to heavy-duty industrial equipment, oil seals are indispensable for preventing the leakage of fluids and ensuring long-term functionality.
The primary function of an oil seal is to create a barrier between two moving parts, typically a rotating shaft and a stationary housing. This barrier is essential as it prevents the leakage of lubricating oil, which is critical for reducing friction and wear between these components. Without oil seals, these machines would quickly degrade, leading to reduced performance, increased maintenance costs, and ultimately, premature failure.
One of the key factors that determine the effectiveness of an oil seal is its material composition. Modern oil seals are typically made from high-quality elastomers, such as nitrile rubber or fluoroelastomers, which possess excellent resistance to heat, chemicals, and abrasion. These materials allow oil seals to withstand extreme operating conditions, ranging from subzero temperatures to high temperatures, while maintaining their shape and sealing properties.
Another important consideration when selecting an oil seal is its design. Oil seals come in a variety of shapes and sizes, each designed to meet specific requirements Oil seals come in a variety of shapes and sizes, each designed to meet specific requirements
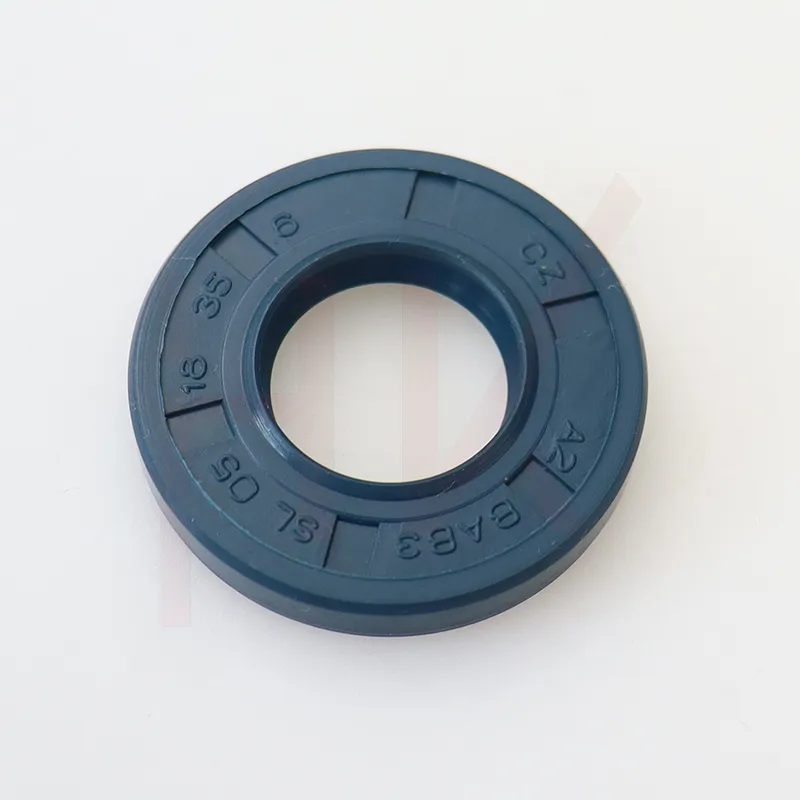
Oil seals come in a variety of shapes and sizes, each designed to meet specific requirements Oil seals come in a variety of shapes and sizes, each designed to meet specific requirements
22 35 7 oil seal. For example, lip seals are commonly used in applications where the shaft has a small diameter, while radial shaft seals are better suited for larger diameters. Additionally, the design of the seal's sealing lip can vary, with some being more effective at creating a tight seal under high pressure or speed conditions.
Proper installation and maintenance are also critical for ensuring the longevity and performance of oil seals. It is essential to ensure that the seal is correctly aligned and torqued during installation to prevent damage or misalignment. Regular inspection and replacement of worn or damaged seals are also necessary to prevent leaks and ensure optimal machine performance.
In conclusion, oil seals are a vital component in maintaining the performance and longevity of machinery and equipment. By providing a reliable barrier between moving parts, these seals prevent the leakage of fluids and reduce friction and wear, leading to improved efficiency and reduced maintenance costs. With their high-quality materials and careful design, modern oil seals can withstand extreme operating conditions and withstand the test of time. Proper installation and maintenance are also crucial for ensuring their continued effectiveness, making them an indispensable part of any mechanical system.