Metal wiper seals, essential components in the arena of hydraulic and pneumatic systems, play a pivotal role in ensuring the longevity and efficiency of various mechanical applications. Often overshadowed by their rubber counterparts, metal wiper seals offer unmatched durability and performance in extreme conditions, setting them apart as indispensable assets in specialized industries.
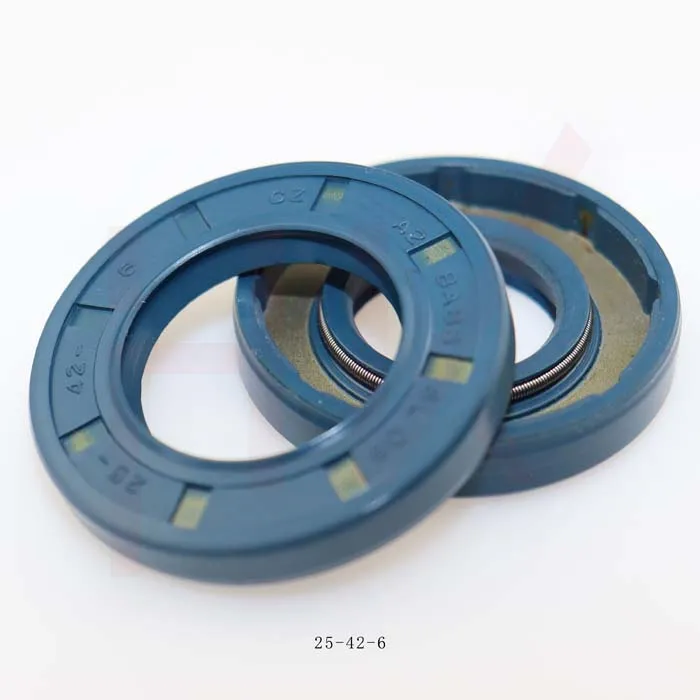
Experience in employing metal wiper seals reveals their superior capacity to combat contamination and wear, making them ideal for environments with stringent operational demands. These seals are meticulously engineered to withstand not only high temperatures but also abrasive materials that would typically degrade polymer-based seals faster. For industries like aerospace, automotive, and heavy machinery, where operational failure is not an option, the reliability of metal wiper seals is irreplaceable. In real-world applications, they have consistently demonstrated an ability to sustain prolonged use without a noticeable decline in performance, thus reducing maintenance requirements and extending the life span of the equipment they protect.
From an expertise standpoint, metal wiper seals are crafted from a variety of metals, each chosen based on the specific operational environment and required resistance. Stainless steel, for instance, is favored for its resistance to corrosion and ability to maintain integrity under thermal stress. Aluminum, on the other hand, offers a lightweight alternative for applications where weight savings are critical. Modern manufacturing processes leverage these materials, combined with advanced metallurgical techniques, to produce seals with bespoke characteristics, such as enhanced elasticity or increased hardness. This level of customization ensures that each seal can be precisely matched to its intended purpose, optimizing functionality and efficiency.
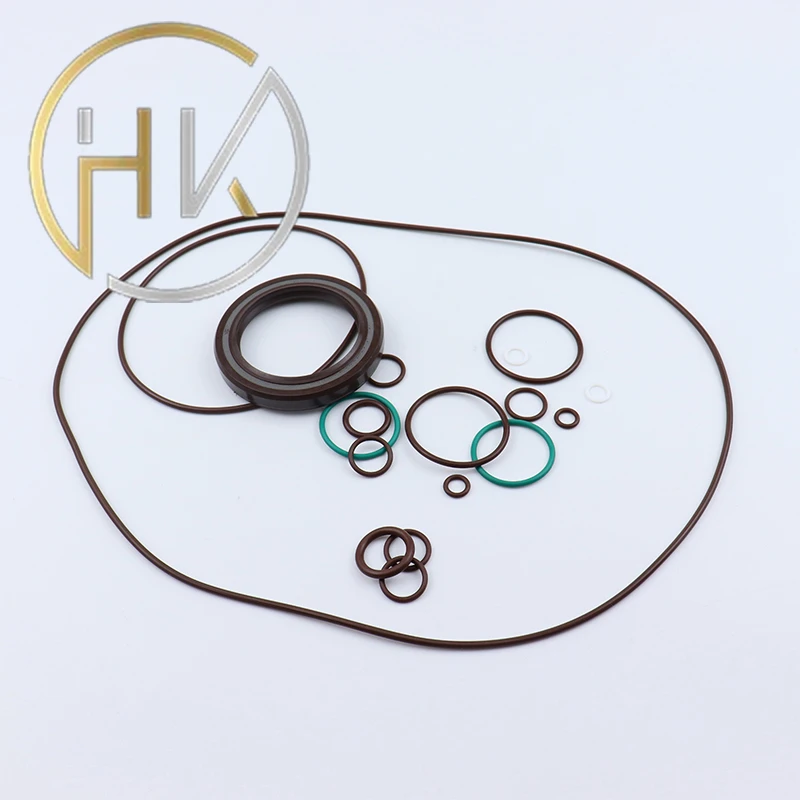
metal wiper seal
The authoritative aspects of metal wiper seal usage lie in the extensive research and development that informs their design and application. Leading manufacturers invest heavily in R&D, often in collaboration with industry experts and research institutions, to push the boundaries of what metal seals can achieve. This effort results in high-precision products capable of maintaining a flawless operation in conditions that include fluctuations in pressure, exposure to hydraulic fluids, and contact with particulates. The authoritative voice of these manufacturers is further reinforced by their rigorous quality control processes, ensuring each seal meets industry standards and client specifications.
Trustworthiness in metal wiper seals is earned through their proven track record and the credibility of their makers. Suppliers of high-quality metal seals provide extensive documentation to validate the performance claims of their products, often including rigorous testing data. These include endurance tests,
exposure to extreme temperatures, and resistance to fluid degradation. Additionally, third-party certifications from recognized standards organizations serve as further testament to the reliability and quality of these components. This transparency in testing and certification instills confidence among users, advocating for the switch from traditional sealing methods to metal alternatives where appropriate.
In conclusion, metal wiper seals stand as a testament to engineering excellence, showcasing a harmonious blend of experience-driven development, specialized expertise, authoritative design standards, and an unwavering commitment to trustworthiness. These seals are not merely functional components; they are critical to the integrity and efficiency of the systems they serve. As industries continue to evolve and demand ever-greater performance from their equipment, the role of metal wiper seals as reliable protectors against contamination and wear will only become more pronounced, ensuring their place at the forefront of sealing technology advancements.