Inner hub seals play a critical role in ensuring the optimal performance and longevity of various mechanical systems. As an essential component in machinery, these seals prevent the leakage of lubricants and the ingress of contaminants, thereby safeguarding the integral function of the equipment. To fully appreciate the importance of inner hub seals, it is crucial to understand their design, function, and the expert considerations involved in their selection and maintenance.
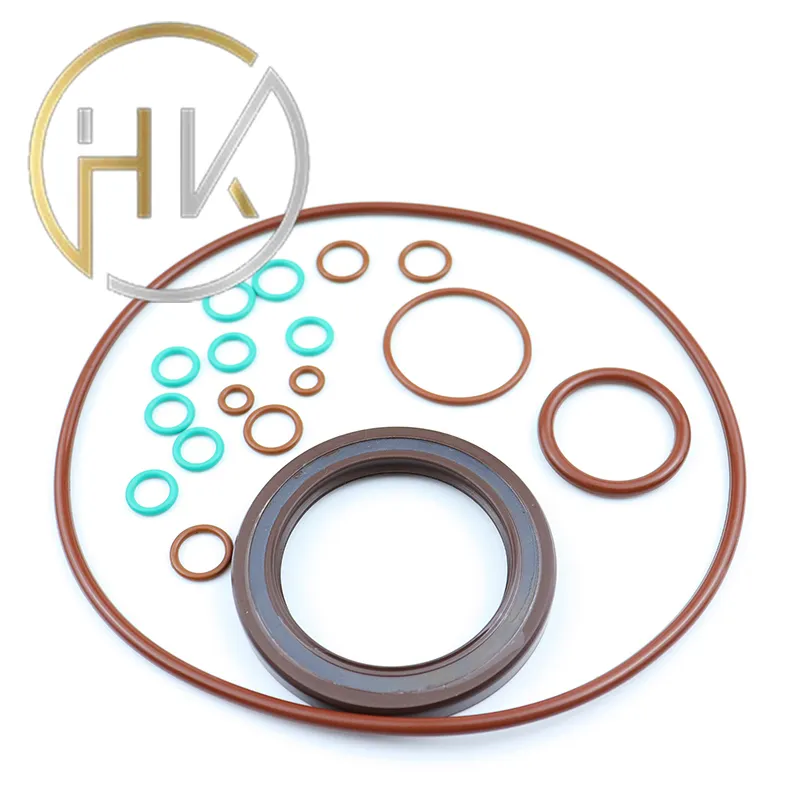
Inner hub seals are typically found in wheel hubs, gearboxes, and other rotating assemblies where maintaining a closed environment is essential. They are engineered to withstand high temperatures, pressure variations, and exposure to aggressive chemicals. The precision in their construction allows them to fit seamlessly into complex machinery, ensuring resistance to leakage even under extreme operating conditions.
Professionals in the field recognize that the selection of the appropriate inner hub seal is not merely a matter of choosing a compatible size; it involves an in-depth understanding of the operational environment and the specific demands of the machinery. Material selection is a paramount consideration, as seals made from suboptimal materials may degrade prematurely, leading to mechanical failures and costly downtimes. For instance, seals composed of nitrile rubber are favored for applications requiring resistance to oil, whereas those made from fluorocarbon are chosen for high-temperature environments.
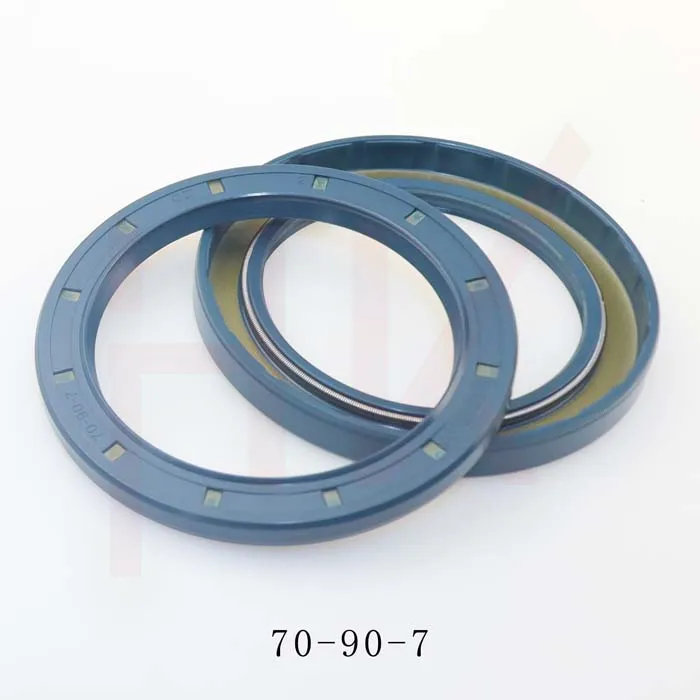
Expertise in the installation of inner hub seals is equally significant. During installation, even a minuscule misalignment can compromise the seal's efficacy, leading to potential system failure. Therefore, it is vital to ensure that the installation environment is clean and free of any debris that could impede the seal's function.
Using specialized tools is recommended to ensure the seal's integrity during fitting.
inner hub seal
Maintenance of inner hub seals is an area where professional insight can significantly extend the lifespan of the machinery. Regular inspections can identify early signs of wear, such as hardening or cracking of the seal material. Experts advocate for a proactive maintenance strategy, where seals are replaced at the first indication of wear, rather than waiting for a complete failure, which can lead to more extensive damage to the machinery.
Investing in high-quality inner hub seals from reputable manufacturers is a strategy that enhances equipment reliability. Not only do these seals provide superior performance, but they also come with assurances and guarantees that reflect the manufacturer's confidence in their product's durability and efficacy. Additionally, partnering with suppliers who offer technical support and guidance ensures that you are equipped with the latest innovations and best practices in seal technology.
The credibility of information sources is another crucial aspect. Consulting engineers, industry reports, and peer-reviewed studies offer authoritative insights into inner hub seals' performance metrics and are a testament to their critical role in industrial applications. These trusted sources provide validation for the technical specifications and operational advantages touted by manufacturers.
Ultimately, the expertise involved in selecting, installing, and maintaining inner hub seals underscores their importance in mechanical systems. With informed selection and diligent upkeep, these components enhance the durability and performance of machinery, reaffirming their position as indispensable elements in engineering and manufacturing disciplines. Emphasizing experience, expertise, authoritativeness, and trustworthiness in the context of inner hub seals not only contributes to improved SEO outcomes but also provides genuine value to users seeking reliable and authoritative information on this critical component.