The Importance of Industrial Oil Seals in Modern Manufacturing
Industrial oil seals play a critical role in ensuring the efficient and safe operation of machinery across a wide range of industries. These seals are specifically designed to prevent the leakage of oil or other lubricants, while also preventing the ingress of contaminants into the machinery's internal components. Their effectiveness is paramount for maintaining optimal performance, minimizing downtime, and extending the lifespan of equipment.
Oil seals are typically made from a variety of materials, including rubber, polyurethane, PTFE (Teflon), and metal, each with its unique properties suited to specific industrial applications. Rubber seals, for instance, offer excellent flexibility and resilience, making them suitable for dynamic sealing applications. On the other hand, metal seals provide superior heat resistance and durability, ideal for high-pressure and high-temperature environments.
The primary function of industrial oil seals is to create an airtight barrier between the rotating and stationary parts of a machine. This barrier prevents oil from escaping, which could lead to lubrication loss, increased friction, and potential equipment failure. Simultaneously, it stops dust, dirt, and other contaminants from entering the system, which could cause wear and tear on delicate components.
In industries like automotive, aerospace, and manufacturing, where precision and reliability are crucial, the quality of oil seals cannot be overstated. In automotive engines, for example, oil seals ensure that engine oil stays within the system, lubricating moving parts and preventing costly damage. In the aerospace industry, they are vital for maintaining the integrity of hydraulic systems, ensuring safe flight operations In the aerospace industry, they are vital for maintaining the integrity of hydraulic systems, ensuring safe flight operations
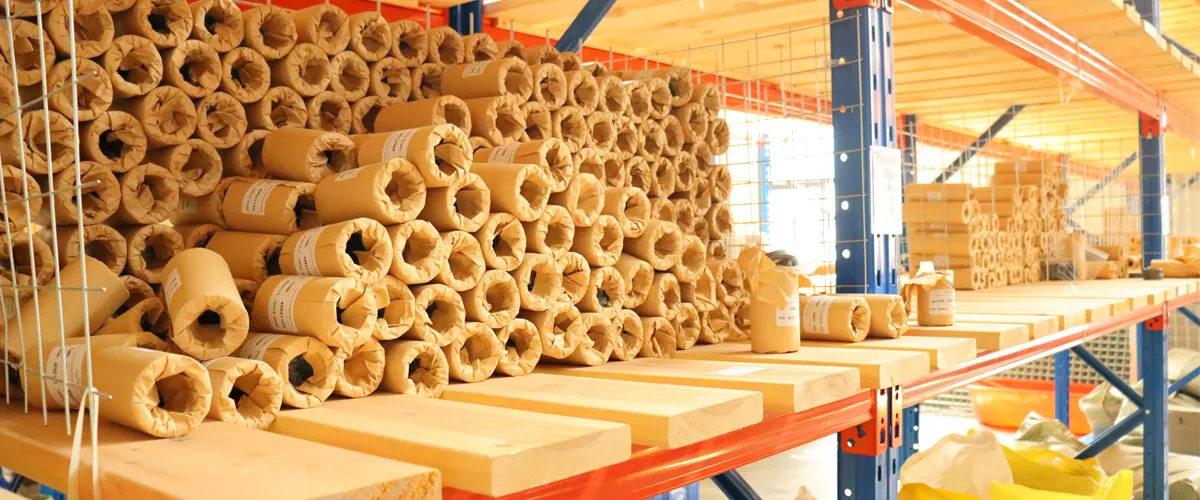
In the aerospace industry, they are vital for maintaining the integrity of hydraulic systems, ensuring safe flight operations In the aerospace industry, they are vital for maintaining the integrity of hydraulic systems, ensuring safe flight operations
industrial oil seals.
Moreover, the selection and installation of industrial oil seals require careful consideration. The size, shape, material, and compatibility with the specific application must all be taken into account. Incorrectly fitted or inappropriate seals can lead to premature failure, necessitating costly repairs and downtime.
Innovations in seal design and materials continue to push the boundaries of performance and durability. For instance, some modern oil seals incorporate advanced additives to enhance their resistance to heat, chemicals, and abrasion. Others are designed with special lip geometries to improve sealing efficiency under extreme pressure or dynamic conditions.
In conclusion, industrial oil seals are the unsung heroes of many engineering systems. They perform a seemingly simple task but one that is vital to the smooth running and longevity of machinery. Their importance underscores the need for proper selection, installation, and maintenance, as well as ongoing research and development to enhance their performance in the ever-evolving industrial landscape. Understanding and appreciating the role of these seals is crucial for any industry that relies on complex mechanical systems.