Hydraulic ram seals are critical components in the construction and operation of hydraulic systems. These seals serve multiple purposes, including maintaining pressure, preventing fluid leakage, and keeping contaminants out of the hydraulic system. Without the proper functioning of these seals, hydraulic systems can suffer from inefficiencies, maintenance issues, and even failure. The importance of selecting high-quality hydraulic ram seals cannot be understated, especially for businesses reliant on heavy machinery.
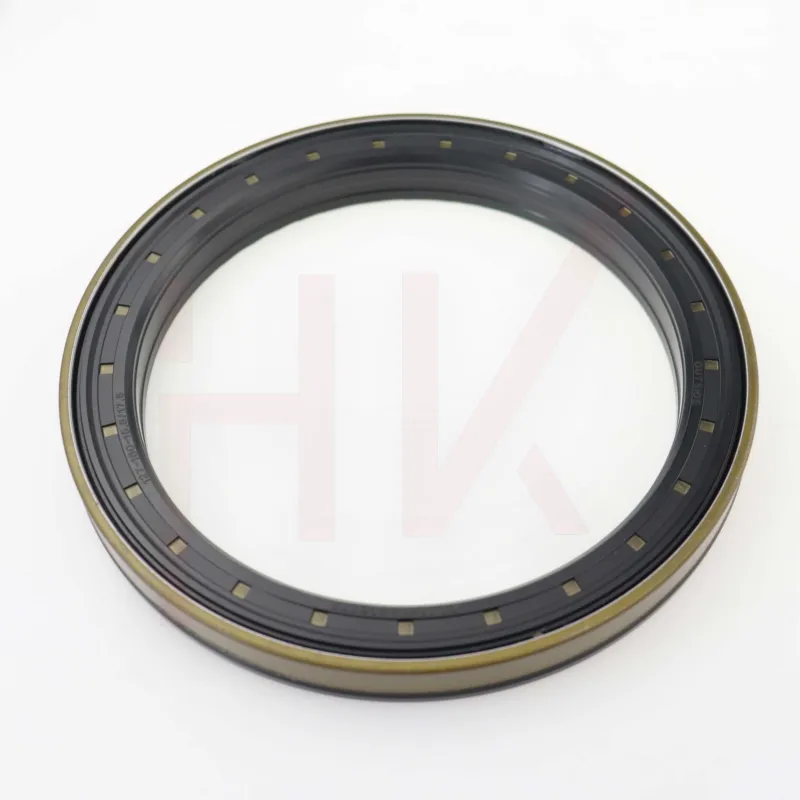
In the realm of hydraulic systems, the choice of seals significantly impacts efficiency and operational reliability. Not all hydraulic ram seals are created equal, and the key to effective selection lies in understanding the specific requirements of your application. This involves assessing factors such as temperature, pressure, chemical exposure, and the type of fluid used. Failing to accommodate these variables can lead to accelerated wear or failure, potentially bringing operations to a halt.
Materials matter when choosing hydraulic ram seals. Common materials include nitrile rubber, Viton, and polyurethane, each offering distinct advantages. Nitrile rubber seals excel in applications involving petroleum-based fluids, providing resilience at a cost-effective price. Conversely, Viton seals cater to high-temperature applications with excellent chemical resistance, suitable for demanding environments. Polyurethane seals, known for their robustness, are ideal for applications requiring superior wear resistance and high-pressure sealing.
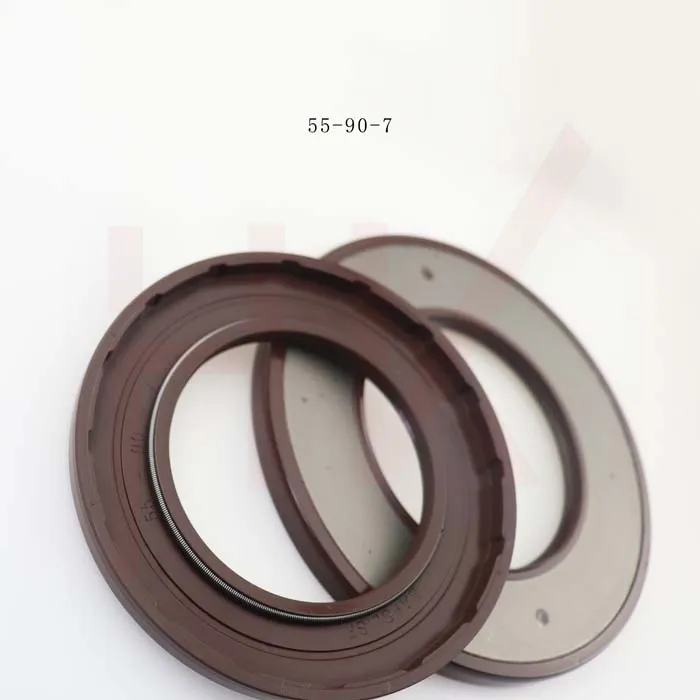
Precision in manufacturing ensures the hydraulic ram seals' effectiveness. Companies producing these seals, such as Parker Hannifin and Trelleborg, uphold high standards by employing advanced techniques and top-grade materials. These manufacturers also offer custom solutions, catering to unique specifications and challenging environments. Leveraging reputable brands and custom capabilities guarantees that the hydraulic ram seals perform optimally over their intended lifespan.
hydraulic ram seals
Installation and maintenance of hydraulic ram seals are equally crucial. Correct installation involves ensuring alignment and cleanliness, avoiding damage from debris or improper fitting. Regular inspection of seals for wear or cracks preempts potential failures, emphasizing the importance of a proactive maintenance schedule. Immediate replacement of compromised seals prevents breakdowns, maintaining operational continuity.
Enhancing the lifespan and performance of hydraulic ram seals can also be achieved through proper lubrication. Utilizing lubricants specifically designed for hydraulic systems minimizes friction and heat generation, thereby extending the service life of the seals. Moreover, investing in quality lubricants reduces maintenance costs and sustains system efficiency through consistent performance.
Businesses should also consider partner providers who offer after-sales support and seal refurbishment services. Partners like SKF provide comprehensive solutions, including testing, inspection, and remanufacturing services, securing operational reliability. Opting for such partners not only maximizes the hydraulic system's uptime but also adds a layer of expertise, as these providers often bring decades of industry experience.
In conclusion, hydraulic ram seals are not mere accessories but integral components indispensable for the efficient operation of a hydraulic system. Businesses should prioritize quality, compatibility, and reliability when selecting these seals. By investing time and resources into choosing the right seals and adhering to best maintenance practices, companies can ensure smooth, efficient, and uninterrupted operations in their hydraulic systems.