Hydraulic ram seals are critical components in ensuring the efficient and reliable functioning of hydraulic systems. Made from a variety of materials including nitrile rubber, polyurethane, and PTFE, these seals are engineered to withstand the immense pressures and dynamic movements inherent in hydraulic systems. For those invested in the maintenance and optimization of hydraulic machinery, understanding the nuances of hydraulic ram seals is key to enhancing the longevity and performance of such systems.

The construction of hydraulic ram seals is pivotal in preventing leaks and maintaining pressure levels within hydraulic cylinders. With machinery operating under extreme operational environments, these seals are designed to act as a barrier, keeping high-pressure fluids contained and ensuring smooth motion and energy transfer. Each material used in crafting these seals offers distinct advantages; for instance, nitrile rubber is highly resistant to oils and greases, polyurethane offers excellent tensile strength, and PTFE is known for its low friction properties and resistance to chemicals and high temperatures.
The choice of a seal often comes down to specific application requirements. For example, in industries where machinery is exposed to very high temperatures, PTFE seals might be preferred due to their heat resistance. Conversely, in environments where machinery might experience frequent coolant exposure, materials like nitrile may provide better resilience. This adaptability underlines the criticality of selecting a seal material that aligns with environmental and operational demands, thereby reducing maintenance costs and unplanned downtime.
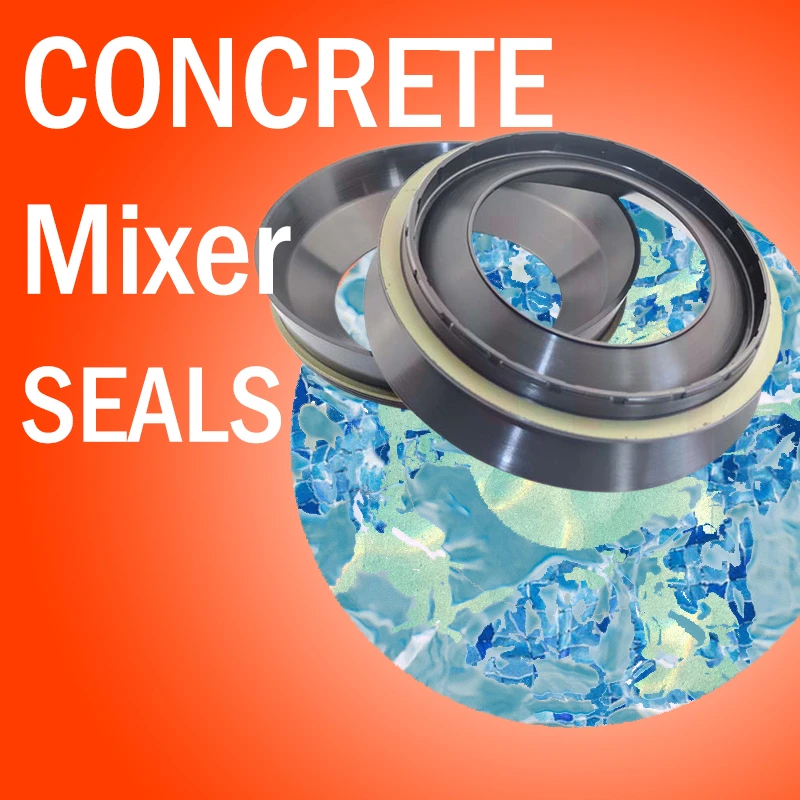
Performance notwithstanding, the installation of hydraulic ram seals is equally crucial. Incorrect installation can lead to immediate operational failure, unnecessary wear and tear, and even catastrophic system failures. Precision during installation is paramount seals need to be aligned perfectly, inserted without damage, and checked for fit within their corresponding grooves. Professionals in the field often rely on specialized tools and equipment to ensure the seals are seated correctly, maintaining the intended compression and pressure.
hydraulic ram seals
Moreover, regular inspections and maintenance are indispensable best practices. Seals, despite their robust design, can degrade over time due to factors like thermal cycling, chemical erosion, and mechanical stress. Regular visual inspections, accompanied by performance audits of the hydraulic system, can preemptively identify potential issues. Look for telltale signs of wear such as cracking, deformation, or hardening, which can indicate imminent seal failure.
Hydraulic ram seals also play a significant role in enhancing the safety standards of machinery operations. A compromised seal can not only lead to system inefficiency but pose serious safety hazards. High-pressure fluid leaks can cause machinery to malfunction unexpectedly, posing risks to personnel. Therefore, keeping hydraulic systems sealed tight is as much about optimizing performance as it is about ensuring operational safety.
For those tasked with the selection and maintenance of hydraulic ram seals, leveraging expertise from reputable manufacturers and suppliers is advisable. Industry leaders often provide product specifications, technical support, and guidance that help in making informed decisions regarding the right seals for specific applications. Partnering with such manufacturers can provide assurance of quality, compatibility, and compliance with industry standards.
In summation, the influence of hydraulic ram seals on the successful operation of hydraulic systems cannot be overstated. Their role extends beyond mere fluid retention – they are intrinsic to the functionality, efficiency, and safety of the machinery they serve. As advancements in material science continue, the future of hydraulic ram seals will likely see innovations that further enhance their performance capabilities, pushing the boundaries of what’s possible within hydraulic engineering. As such, those in the field should remain updated with industry developments and continuously hone their understanding of these integral system components. By doing so, they not only extend the lifespan of machinery but also help drive forward a culture of excellence and safety within industrial operations.