Navigating the world of hydraulic systems often leads one to explore the critical role of oil seals in hydraulic presses. Hydraulic press oil seals are pivotal components in such systems, designed to prevent fluid leakage, ensure system efficiency, and prolong the life of the machinery. Understanding these seals from an expert perspective requires insight into their design, material composition, function, and maintenance. This article aims to provide you with a comprehensive understanding of hydraulic press oil seals that is both informative and trustworthy.
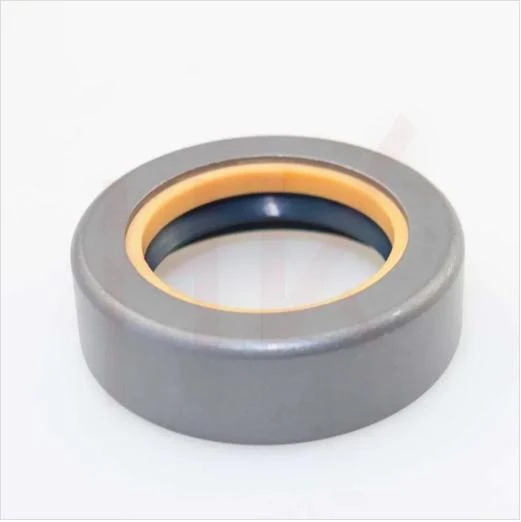
Hydraulic press oil seals are designed to contain hydraulic fluid, preventing it from leaking out of the system. Made from durable materials such as rubber, PTFE, or composite polymers, these seals must withstand extreme pressures and temperatures while maintaining flexibility and resilience. The choice of material significantly impacts the seal’s performance; therefore, understanding the environment in which the seal will operate is critical. For instance, seals operating in high-temperature environments require materials like Viton or silicone that can sustain performance under such conditions.
One often overlooked but essential aspect of hydraulic press oil seals is their design and structural integrity. These seals typically consist of a metal casing for stability, an elastomeric sealing lip for flexibility, and sometimes a spring to maintain contact force against the rotating shaft. Seals are categorized as either dynamic or static, depending on the type of application—dynamic seals are used in applications where there is movement between the sealing and counter surfaces, whereas static seals are used where surfaces do not move relative to each other.
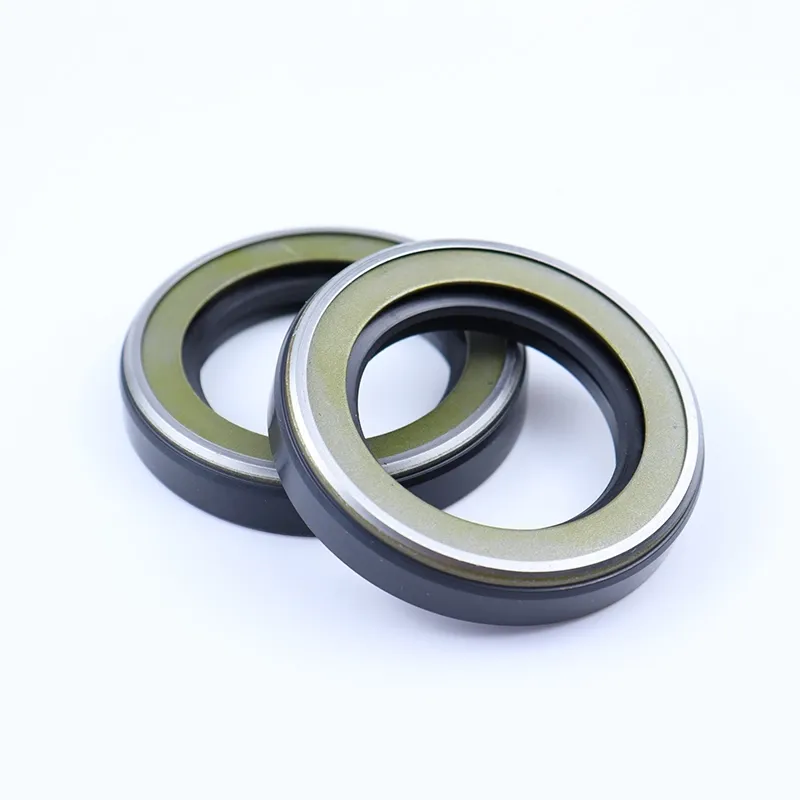
The importance of proper installation and maintenance cannot be overstated. Incorrect installation of an oil seal can lead to premature failure, resulting in costly downtime and repairs. Thus, consulting authoritative installation guides and, if needed, employing experienced technicians can mitigate this risk. Additionally, regular inspection of seals as part of the maintenance routine is mandatory. Checking for wear and tear, inspecting for signs of leakage, and replacing seals at the first indication of damage are practices that enhance system reliability and longevity.
hydraulic press oil seal
To establish expertise in hydraulic press oil seal selection and application, it is crucial to understand the specifications of your hydraulic system meticulously. Parameters such as pressure ratings, operating temperatures, fluid type, and shaft speeds directly influence the selection process. A comprehensive specification sheet from reputable manufacturers can provide trusted guidance in matching seal properties with system requirements.
Expert reviews and case studies are excellent resources for gaining authoritative knowledge about hydraulic press oil seals' performance in different scenarios. Engaging with industry experts or joining professional forums can supply practical insights and testimonials, reflecting real-world experience and trustworthiness.
In conclusion, managing hydraulic press oil seals with expertise involves a blend of technical knowledge, practical experience, and continuous learning about material advancements and industry standards. By prioritizing these elements, one can ensure efficient performance, enhanced longevity, and reduced downtimes of hydraulic systems. As hydraulic technology evolves, staying informed about the latest innovations and maintaining a proactive approach to system management will enable one to leverage the full potential of their hydraulic applications.