Selecting the right hydraulic oil seal material is a critical aspect of ensuring the efficiency and longevity of hydraulic systems. In industries ranging from automotive to aerospace, hydraulic systems are the linchpin, ensuring precision, reliability, and safety. The choice of the right seal material can be the dividing line between optimal performance and mechanical failure.
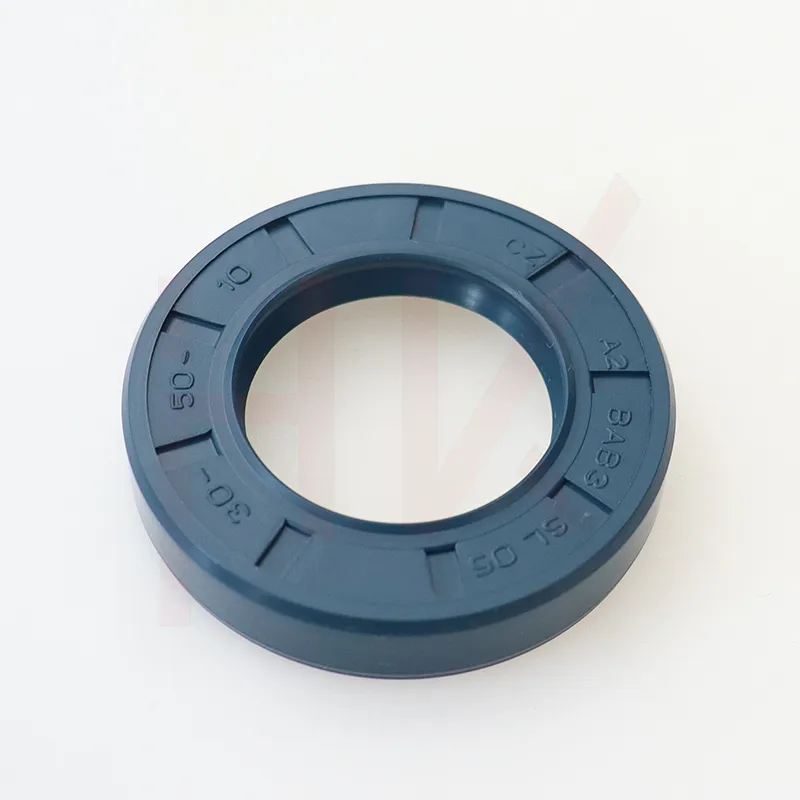
Hydraulic oil seals serve as a barrier, preventing leakage and contamination while sustaining high pressure. They come in contact with hydraulic fluids, which can vary in chemical composition and temperature. Therefore, the material must not only withstand these variables but also retain its flexibility and strength over time.
1. Nitrile Rubber (NBR) Among the most widely used materials, nitrile rubber provides excellent resistance to mineral oils, greases, and hydraulic fluids. It maintains integrity in a temperature range of -40°C to +120°C, though this can extend to +135°C with special formulations. NBR’s affordability and widespread availability make it a popular choice; however, exposure to ozone or sunlight can degrade its properties without proper additives.
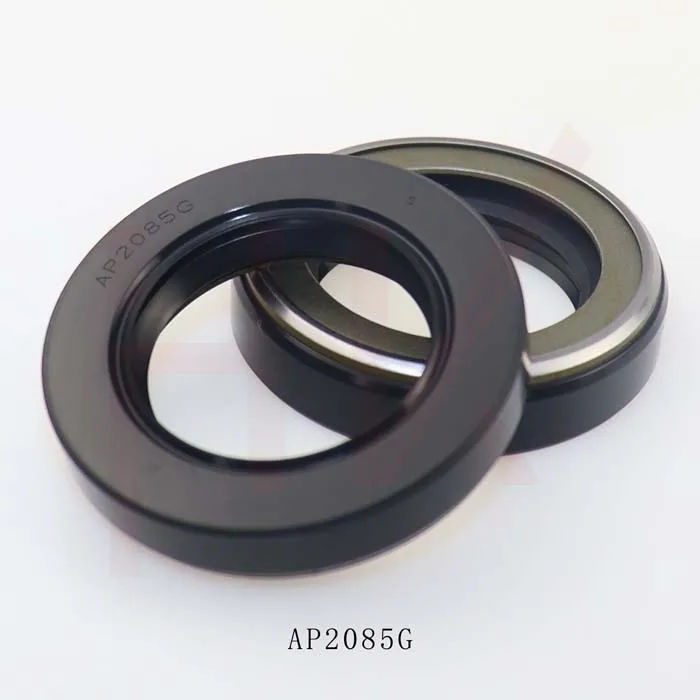
2. Fluorocarbon (FKM/Viton) For hydraulic systems operating at higher temperatures or involving aggressive fluids, fluorocarbon seals are preferred. Withstanding temperatures up to +200°C, FKM demonstrates formidable resistance to diverse oils, lubricants, and fuels. It also maintains sealing effectiveness and mechanical properties in extreme environments, thus ensuring consistent operation in demanding applications like automotive, chemical processing, and power generation.
3. Polyurethane (AU, EU) Known for its exceptional abrasion and tear resistance, polyurethane is ideal for dynamic seals in hydraulic cylinders. It serves environments where there is potential for mechanical damage or particulate contamination without compromising its elasticity or hydraulic fluid compatibility. Its temperature resilience varies, typically ranging from -45°C to +90°C, making it versatile yet limited in certain high-temperature applications.
hydraulic oil seal material
4. PTFE (Teflon) When chemical resistance and low friction are paramount, PTFE seals are exemplary. They function well across a wide temperature range, from -200°C to +260°C, complementing high-speed operations and chemically aggressive fluids. However, PTFE lacks elasticity, often necessitating the incorporation of an elastomeric part to improve sealing capabilities.
5. Silicone Rubber This material is favored in static sealing applications or where there are high temperatures up to +200°C. Its significant advantage lies in its ability to maintain flexibility at very low temperatures (-60°C), making it suitable for cold environments. However,
resistance to oils and fuels is lower compared to materials like fluorocarbon.
The decision-making process should also consider environmental factors and application-specific conditions. Consulting with seal manufacturers or specialists ensures a harmonious balance between performance and cost-effectiveness. Advanced hybrid materials and proprietary blends further augment this landscape, offering tailored solutions for novel or extreme environments.
Emphasizing regular maintenance and inspection regimes is paramount. Even the most resilient materials will falter under neglected conditions. Establishing a protocol to monitor signs of wear, chemical damage, or thermal degradation ensures timely replacements and adjustment, mitigating operational risks.
Hydraulic oil seals are more than mere components; they are the unsung heroes safeguarding machinery efficiency. The complexity and variability in material science offer tailored solutions, meriting careful analysis and selection befitting the system’s demands. By leveraging these insights and staying abreast of technological advancements, industry professionals can harness the full spectrum of hydraulic seal performance, ensuring operational excellence and technological innovation.