Hydraulic motor seals are pivotal components in the world of fluid-driven systems, playing an essential role in maintaining efficiency and operational stability. These seals, often crafted from high-performance materials, are designed to prevent leaks, maintain pressure balance, and protect internal components from contamination or wear. Their reliability is not just significant but imperative in ensuring the longevity and effectiveness of hydraulic motors, commonly used across diverse industries such as construction, agriculture, and manufacturing.
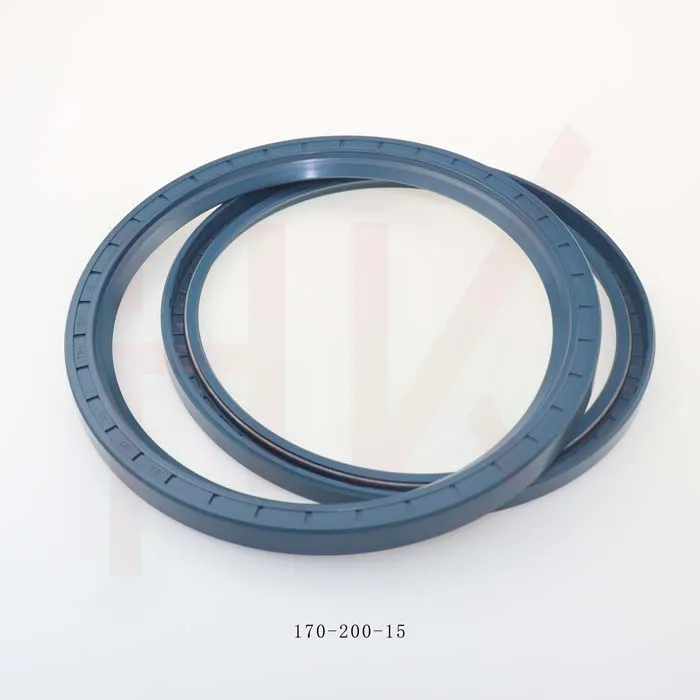
The durability of hydraulic motor seals directly correlates with their ability to withstand extreme environmental conditions. Extreme temperatures, pressure fluctuations, and exposure to various hydraulic fluids demand seals that are not only robust but also versatile. Selecting the right seal involves a deep understanding of the specific application requirements, which include pressure ratings, temperature ranges, and chemical compatibility. Engineers and technicians should prioritize seals with proven resistance to wear, extrusion, and thermal degradation to ensure optimal performance.
In the extensive array of hydraulic systems, the compatibility of seals with hydraulic fluids is crucial. Fluids vary in their chemical composition, and an incompatible seal can lead to premature failure, compromising the entire system. Fluorocarbon, nitrile, and polyurethane are popular materials due to their excellent chemical resistance and ability to maintain integrity under stress. Each material offers unique properties, and selecting one entails a comprehensive assessment of the operational environment and fluid interactions.
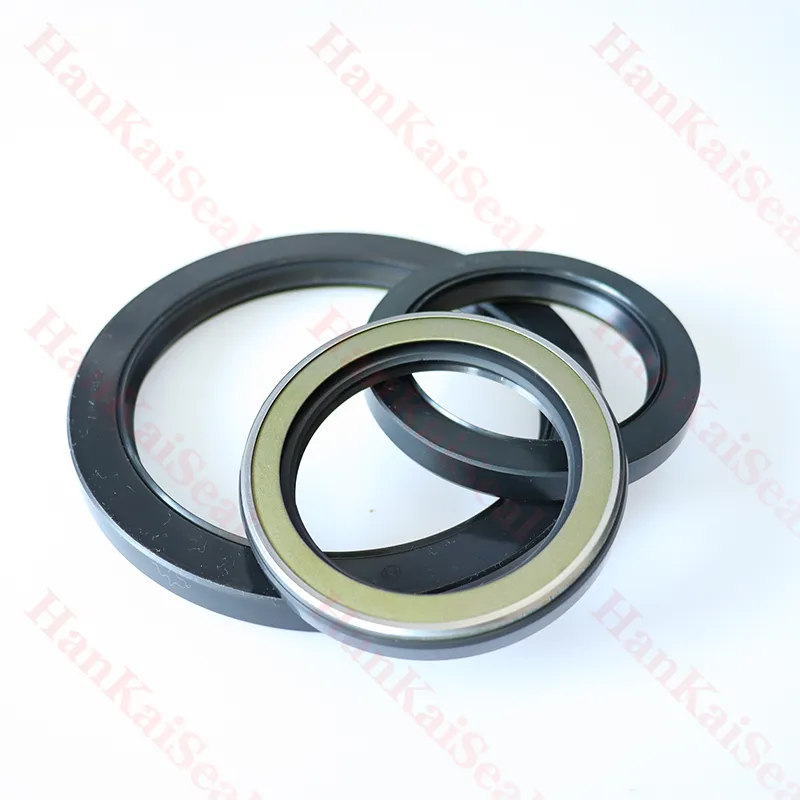
Maintenance practices significantly impact the lifespan and functionality of hydraulic motor seals. Regular inspections and timely replacements are necessary to avoid unscheduled downtimes. Signs of seal failure, such as fluid leaks or pressure drops, should be addressed immediately. This proactive approach not only extends the life of the seals but also enhances the overall efficiency of the hydraulic system. Proper installation techniques, correct sizing, and alignment are critical to prevent installation-related damages.
hydraulic motor seals
Emerging technologies and innovations are continually shaping the development of hydraulic motor seals. Advances in material science have led to the creation of seals that exhibit improved endurance and adaptability. Innovations such as self-lubricating seals and temperature-resistant variants are becoming increasingly prevalent, offering extended service life and reduced maintenance needs. Staying informed about the latest technological developments ensures that industries can re-evaluate traditional practices and adopt more contemporary, efficient solutions.
Collaborating with respected manufacturers and suppliers is another profound aspect that influences the quality and performance of hydraulic motor seals. Reputed brands tend to offer extensive research and testing to ascertain the reliability of their products under variable conditions. Partnering with such entities not only guarantees product authenticity but also provides access to expert technical support and comprehensive after-sales service, contributing significantly to the system's trustworthiness and resilience.
In conclusion, hydraulic motor seals are more than just functional components—they are the guardians of hydraulic system integrity. Their precise selection, maintenance, and implementation can vastly improve system efficiency, reduce operational costs, and prevent potential failures. As industries increasingly rely on advanced hydraulic systems, embracing innovation in seal technology and maintaining best practices will remain pivotal in harnessing the full potential of these essential components.