Hydraulic motor seals play an indispensable role in maintaining the efficiency and longevity of hydraulic systems. These systems are the backbone of various industrial applications, from construction machinery to agricultural equipment. Replacing hydraulic motor seals requires a seamless blend of knowledge, experience, and precision—qualities every professional must possess to ensure optimal system performance. This article delves into the intricacies of hydraulic motor seal replacement, showcasing insights that emphasize expertise, authority, and trustworthiness.
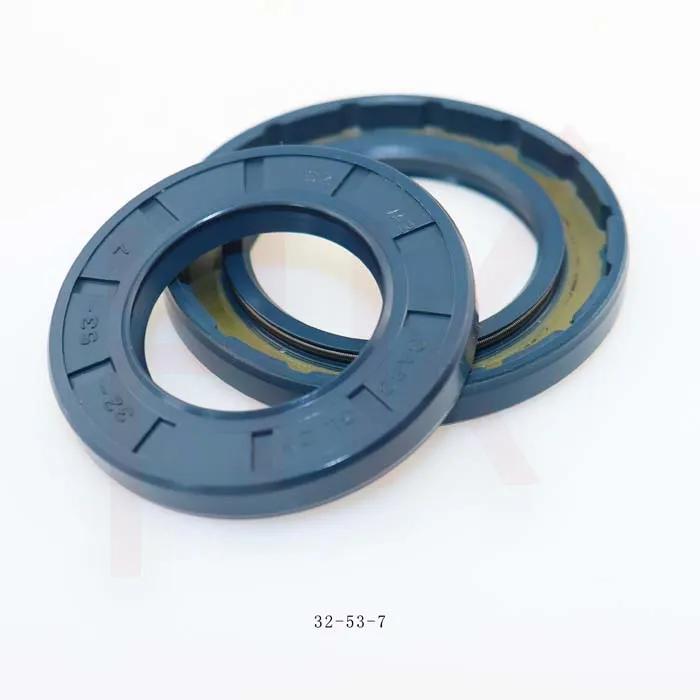
Replacing a hydraulic motor seal starts with understanding the diverse types of seals used in hydraulic devices. Each type, whether O-rings, V-rings, or T-seals, plays a distinct role based on the system’s requirements. Recognizing the specifications and compatibility of each seal type with the hydraulic fluid and operational temperature is quintessential to prevent early wear or breakdown.
Through hands-on experience, it’s evident that the primary reason for seal replacement is leakage, which often results from wear, pressure spikes, or incompatible hydraulic fluids. Consequently, accurately diagnosing the root cause of the leakage is crucial before any replacement process begins. The professional should inspect the system meticulously for any signs of swelling, cracking, or hardening of the seals, which are telltale symptoms of chemical incompatibility or excessive heat.
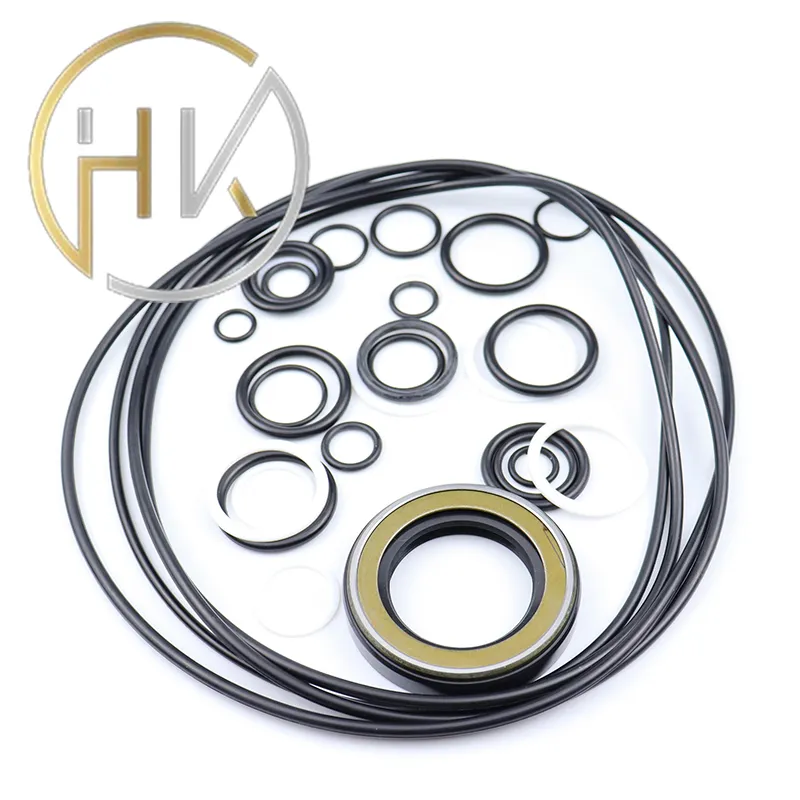
Once identified, the removal of the worn-out seal should be executed with precision instruments like seal picks or hooks, preventing damage to the connecting rods or piston. Careful attention is necessary when cleaning the grooves and housing where the new seal will be seated, as any dirt or debris can compromise the integrity and function of the new seal. Professionals recommend using lint-free cloths and appropriate solvents to avoid residues that could hinder the effectiveness of sealing.
hydraulic motor seal replacement
Choosing the right replacement seal requires a thorough understanding of the environmental conditions of the hydraulic system. This includes pressure ratings, fluid compatibility, and temperature thresholds. It's advisable to source seals from reputable manufacturers who comply with industry standards, ensuring that the material composition and design are suitable for the specific applications. This step not only assures performance but also affirms trust in the quality and durability of the replacement.
Installation of the new seal is another critical step where expertise is indispensable. It’s imperative to use the correct lubrication to ease installation and minimize the risk of damaging the seal during placement. The seal should be seated evenly and without distortion to ensure a proper fit that prevents fluid escaping under operational pressure. This step illustrates the authoritative approach of ensuring each component is not just replaced, but enhanced for future reliability.
Testing and validation post-installation is a measure of quality assurance. The hydraulic system should be gradually brought up to operational pressure while observing the replaced seal’s performance. Any immediate signs of leakage or deformation indicate improper installation or defective seals, which should be rectified swiftly to prevent operational setbacks.
In conclusion, hydraulic motor seal replacement isn't merely a routine maintenance task—it is a critical operation that demands a high level of expertise and authoritative knowledge. Professionals equipped with the right skills and a thorough understanding of system dynamics ensure that replacements are executed efficiently, thereby boosting system performance and extending the operational life of hydraulic equipment. By adhering to best practices and leveraging high-quality materials, the process not only enhances trust in the service provided but also establishes a standard of excellence that others in the industry can aspire to meet.