Selecting the optimal hydraulic cylinder oil seal is a crucial component in ensuring efficient and leak-free performance in hydraulic systems. These seals prevent the escape of fluids or the ingress of contaminants, maintaining the pressure needed for the system's effective operation. When exploring the subject of hydraulic cylinder oil seals, it becomes paramount to consider various factors such as material composition, design specifications, and operational conditions to enhance system reliability and durability.
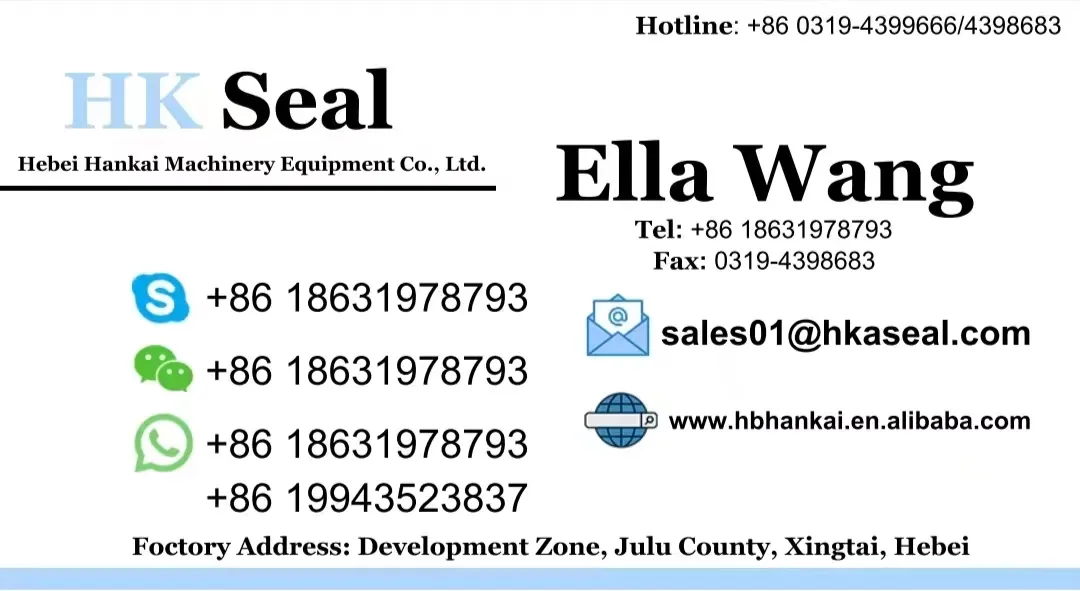
In the realm of hydraulic systems, oil seals are indispensable due to their role in preserving the integrity and functionality of the machinery. These components are crafted from an array of materials including nitrile rubber (NBR), Viton, polyurethane, and PTFE, each suited for specific operational environments. For instance, nitrile rubber’s resistance to oil and its cost-effectiveness make it a popular choice for general applications, whereas Viton offers superior thermal stability and chemical resistance for high-temperature operations.
The design and selection of a hydraulic cylinder oil seal should align meticulously with the system’s operational parameters. Considerations include the working pressure, temperature ranges, and fluid compatibility. High-pressure environments demand seals designed to withstand significant stresses without deforming. Similarly, the seal material must maintain its structural integrity and prevent leakage under fluctuating temperatures and in contact with hydraulic fluids, which may contain different additives that can affect seal performance.
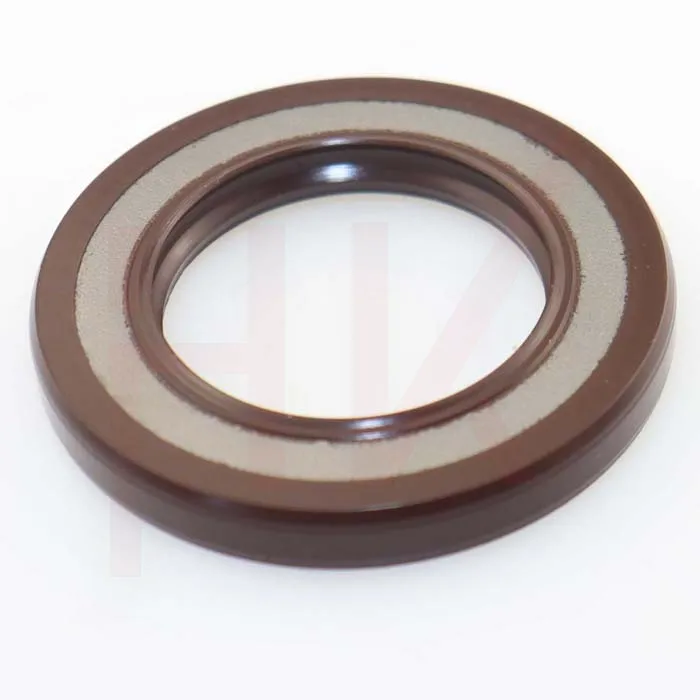
Furthermore, the installation and maintenance of hydraulic cylinder oil seals require adherence to precise standards. Improper installation can lead to premature wear, reduced efficiency, or even catastrophic system failure. It is critical to ensure that the seal is properly seated within the gland and that the surface finish and dimensions match the specifications. Regular inspections are also necessary to detect signs of wear or damage that could compromise the seal’s functionality.
hydraulic cylinder oil seal
A comprehensive understanding of the hydraulic system’s dynamics is essential for selecting the optimal oil seal. Factors such as the rate of reciprocation, lateral forces acting on the cylinder, and the presence of contaminants all influence seal performance. For systems exposed to harsh environments, additional protection such as wipers or scrapers may be required to prevent external contaminants from breaching the seal.
Beyond the physical attributes and installation practices, partnering with reputable manufacturers or suppliers is critical for acquiring high-quality seals. Reliable providers often offer seals that comply with industry standards and are subjected to rigorous testing to ensure performance under specified conditions. Access to technical support and customization options further enhances the suitability of seals for specific applications.
Incorporating advanced sealing technology is another avenue through which the efficacy of hydraulic cylinder oil seals can be boosted. Innovations such as integrated pressure relief or multi-zone sealing strategies can yield significant improvements in leak prevention and longevity. Additionally, the implementation of monitoring systems to assess seal performance in real-time can preempt potential failures and extend operational life.
Trust in the chosen hydraulic cylinder oil seal emerges from a combination of informed selection, thorough understanding, and dedicated maintenance. By placing emphasis on these areas, industries can significantly diminish downtime and enhance the overall efficiency of their hydraulic systems. This approach not only elevates system performance but also reinforces the commitment to quality and reliability that underpins successful engineering practices.