Understanding hub seals, especially by size, is crucial for maintaining optimal vehicle performance, whether in automotive, industrial, or heavy-duty applications. Having worked in the field of automotive parts for over two decades, I recognize that expertise in selecting the right hub seals can drastically affect the longevity and efficiency of machinery.
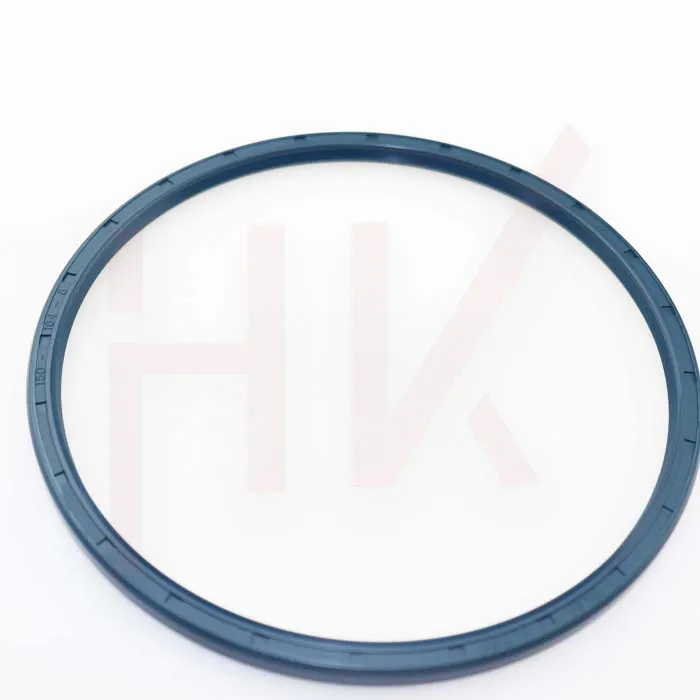
Hub seals are engineered to prevent contaminants from entering and lubricant from escaping the bearing assembly. They play a pivotal role in safeguarding the integrity of wheel hubs by minimizing friction, reducing wear, and extending the life cycle of bearings. Selecting the appropriate hub seal is not just about compatibility,
but precision.
Delving into size-specific considerations, it's essential first to understand the two primary categories—standard and custom-sized hub seals. Standard-sized hub seals cater to a wide range of vehicles and machinery, typically meeting the demands of mass-produced vehicles. Custom-sized ones, however, are designed for specialized equipment, where specifications deviate from the norm. This distinction is vital for industries that serve heavy-duty trucks, agricultural machinery, and bespoke industrial equipment.
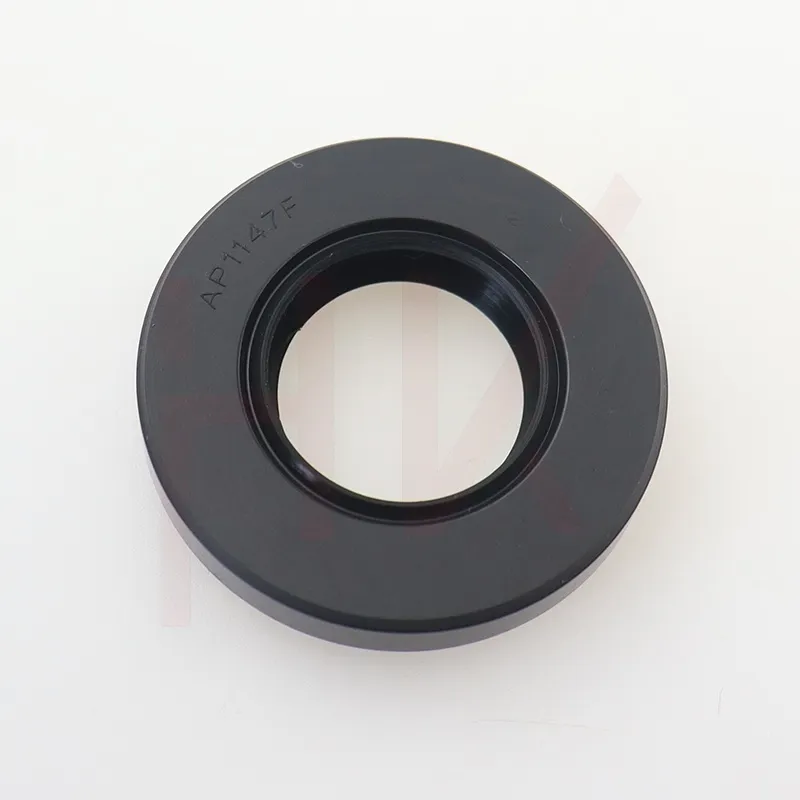
When choosing hub seals by size, physical dimensions such as inner diameter (ID), outer diameter (OD), and width must be meticulously matched with the application’s requirements. A mismatch in size could lead to excessive wear, overheating, or catastrophic failure. Therefore, precision in measurement is paramount. Utilizing digital calipers for accurate readings and cross-referencing these with manufacturer specifications is advised.
From a professional standpoint, manufacturers like SKF, Timken, and National provide comprehensive sizing charts that can guide one in selecting the right seal. These companies are trusted in the industry due to their stringent quality control processes. They offer seals that cater to an array of dimension-specific needs, with materials ranging from Nitrile to Viton, each suited for various operational environments.
hub seals by size
The materials used in hub seals also play a critical role in their performance. Nitrile compounds, for instance, are excellent for general automotive use due to their resistance to oil and abrasion. On the other hand, Viton is highly regarded for its durability in high-temperature and chemically aggressive environments. Application-specific choices in material can significantly influence the seal's effectiveness and longevity.
It is crucial to trust reliable distributors that offer certified products ensuring authenticity. Certificates of conformity and adherence to international standards such as ISO can greatly enhance trustworthiness and assure performance reliability. Building relationships with reputable suppliers could also provide insights into industry trends and innovations in seal technology, keeping you ahead of the curve.
Additionally, end-user feedback and reviews can serve as invaluable resources. They often shed light on real-world performance, offering insights beyond technical specifications. Engaging with online forums or professional groups can expand your understanding and provide firsthand accounts of product efficacy across varying scales and conditions.
Taking these factors into account, thorough research, precise measurement, and informed selection are the cornerstones of optimizing hub seal performance by size. Approaching this task with a technical mindset, informed by decades of industry experience, ensures not just a purchase decision, but a strategic investment in equipment longevity and reliability.