Hub rubber seals, a critical yet often overlooked component, play a pivotal role in ensuring the smooth and efficient operation of various machinery and vehicles. Drawing from extensive experience in the field, this article aims to provide an in-depth understanding of hub rubber seals, emphasizing their functionality, benefits, and the expertise required to select the right ones for specific applications.
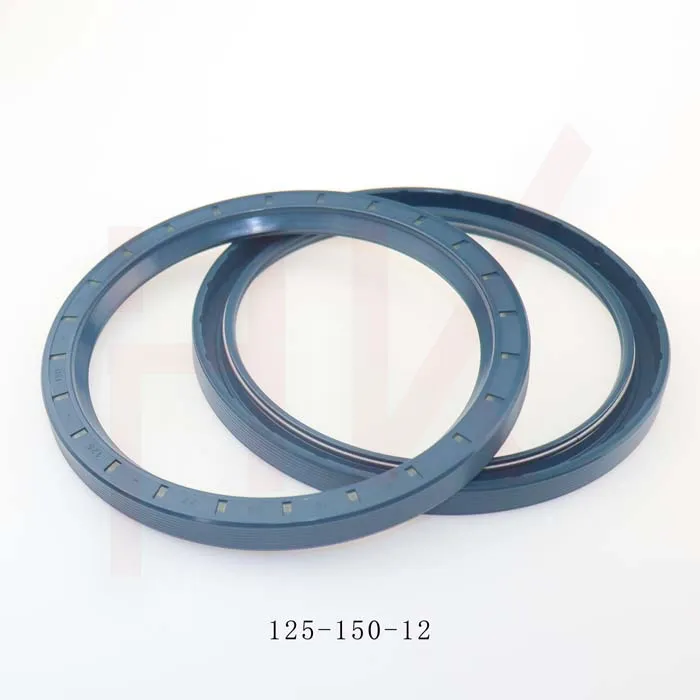
Rubber seals, particularly those designed for hubs, serve as barriers that prevent contaminants such as dust, dirt, and moisture from entering and potentially damaging the internal components of a machine or a vehicle's wheel assembly. A well-crafted rubber seal ensures the longevity and efficiency of the machinery it protects by maintaining the integrity of lubricants within the system. This is crucial not only for the seamless movement of the hubs but also for preventing costly repairs and downtimes.
When discussing expertise in choosing hub rubber seals, understanding the different types of rubber materials is paramount. Nitrile rubber, known for its excellent resistance to oil and abrasion, is suitable for environments exposed to petroleum-based substances. On the other hand, silicone rubber seals can withstand extreme temperature variations, making them ideal for applications where thermal stability is essential. For those requiring superior chemical resistance,
Viton rubber seals are often recommended. The choice of material directly impacts the seal's performance, durability, and ultimately, the reliability of the entire system it safeguards.
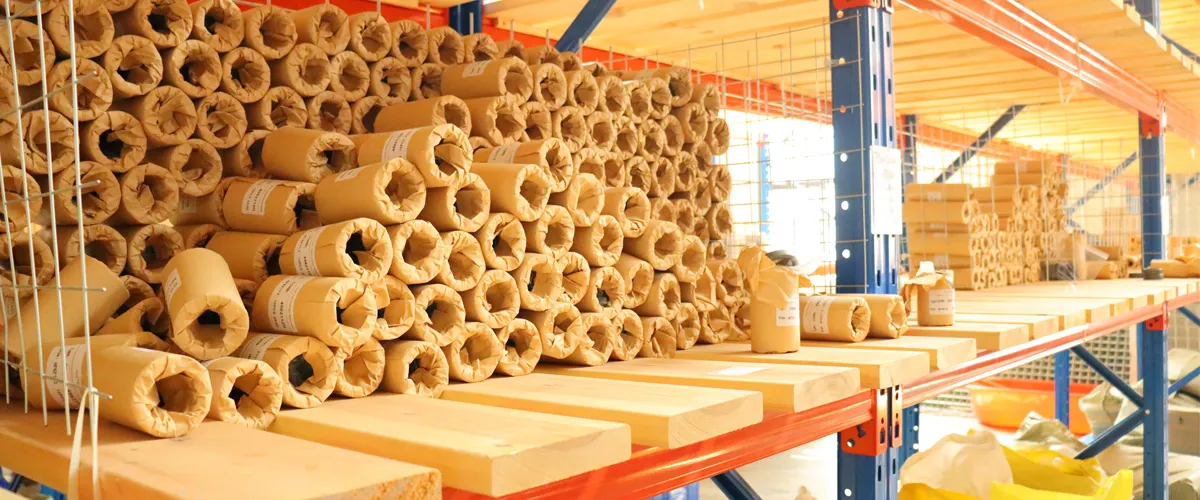
Industry professionals, such as mechanical engineers and maintenance specialists, underscore the importance of precise measurements when selecting hub rubber seals. A poorly fitted seal can lead to leaks and contamination, undermining its purpose. Employing advanced tools and techniques to obtain accurate measurements ensures that the seal forms an optimal fit, thereby maximizing its effectiveness. Moreover, consulting with seal manufacturers and leveraging their expertise can guide users towards selecting the best seal for their specific needs, ensuring a balance between performance and cost-efficiency.
hub rubber seal
Authoritativeness in this domain is established through rigorous testing and adherence to industry standards. Reliable manufacturers subject their hub rubber seals to extensive quality control tests, including pressure, tensile strength, and resistance assessments, to meet or exceed the expected performance criteria. Certifications from recognized bodies offer assurance of a product’s quality, instilling confidence in end-users about its reliability and durability.
Trustworthiness is another crucial factor, cultivated through transparency and customer-centric approaches. Manufacturers and suppliers who prioritize customer education, providing detailed product specifications and clear usage guidelines, help users make informed decisions. Positive testimonials and reviews from satisfied clients further reinforce trust, illustrating the successful application and performance of the rubber seals in real-world scenarios.
In conclusion, hub rubber seals are indispensable components that ensure the optimal performance of machinery and vehicles. Choosing the right seal requires a blend of experience, expertise, authoritativeness, and trustworthiness. By paying meticulous attention to material selection, precision in measurements, and adherence to quality standards, users can significantly enhance the durability and efficiency of their systems. As manufacturers continue to innovate, integrating new materials and technologies, the importance of informed selection and maintenance of hub rubber seals remains a cornerstone of operational reliability.