In the realm of industrial machinery, understanding the nuances of high-temperature oil seals can differentiate between seamless operations and costly downtimes. High-temperature oil seals are quintessential for equipment that operates under extreme heat conditions, providing critical protection to prevent leakage of lubricants and entry of contaminants.
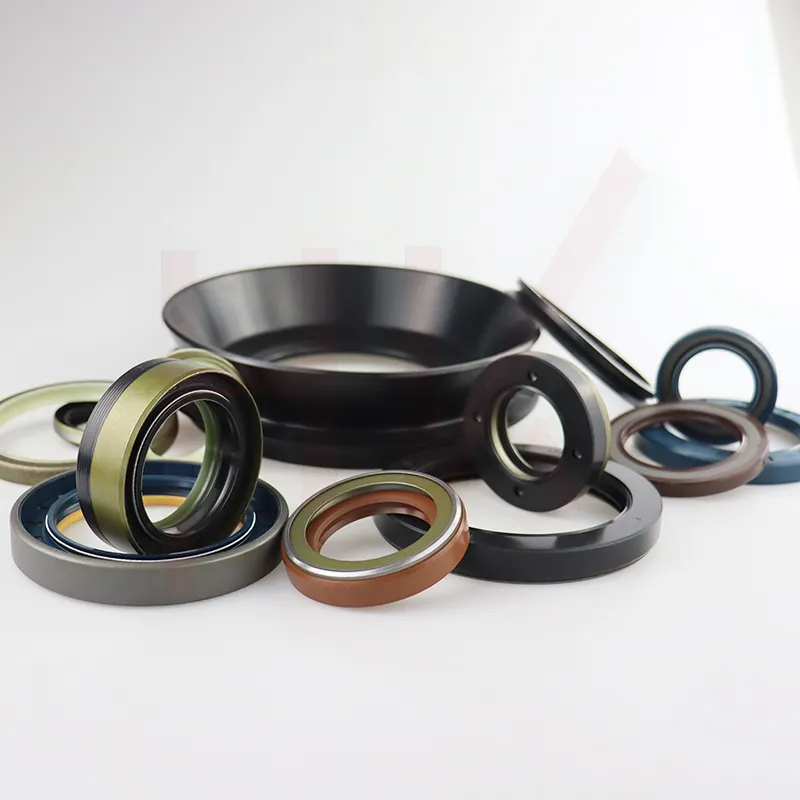
Firstly, let us delve into the expertise behind these seals. High-temperature oil seals are engineered using specialized materials such as fluorocarbon, silicone, and PTFE that can withstand temperatures beyond 250°C. These materials are selected for their thermal stability, resistance to chemical degradation, and ability to maintain elasticity under duress. An advanced understanding of material sciences allows manufacturers to tailor seals for specific industrial applications, ensuring optimal performance and longevity.
The design intricacies of these seals contribute significantly to their effectiveness. Double lip designs, for instance, provide an additional barrier against contaminants while simultaneously retaining lubricants. Such innovative designs stem from years of meticulous research and development, bringing forth an authoritative edge in the market. Cross-sectional profiles, spring-accommodated lips, and special coatings are other design features that enhance reliability and show the depth of expertise involved in creating these seals.
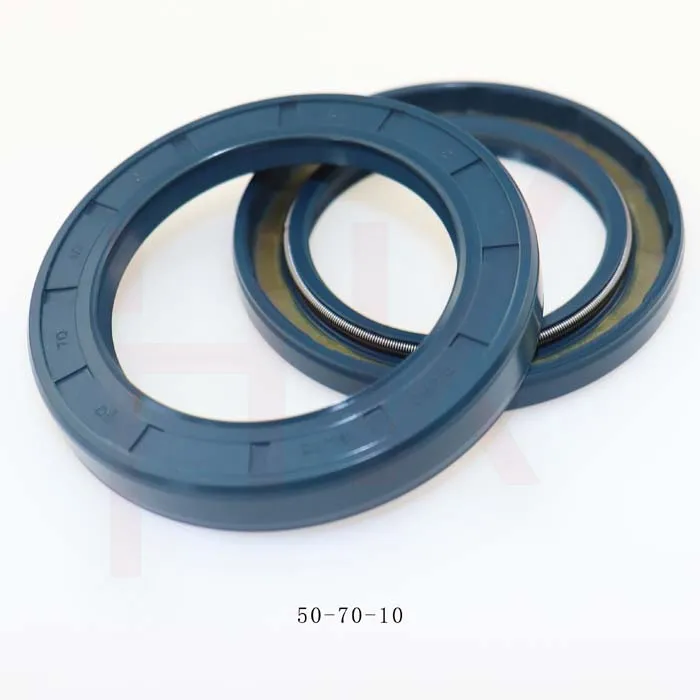
Real-world experience underscores the importance of selecting the right high-temperature oil seal. Industries such as aerospace, automotive, and heavy machinery frequently deal with extreme conditions where seal failure is not an option. For instance, in the aerospace industry, oil seals must withstand not just high temperatures but also fluctuating pressures and aggressive fluids. A testimony from experienced engineers reveals that overlooking seal quality can lead to catastrophic failures, making it imperative to choose seals from trusted manufacturers with a track record of excellence.
high temp oil seal
The authoritativeness of a brand offering high-temperature oil seals is often built on certifications and compliance with international standards. Look for manufacturers who adhere to standards like ISO 90012015 for quality management systems, and who provide detailed testing reports. This adds a layer of trustworthiness to the product, assuring that it meets rigorous industrial standards and specifications. Engaging with manufacturers that offer comprehensive product knowledge and customer support further solidifies their stance as industry leaders.
Trustworthiness in high-temperature oil seals is also grounded in transparency regarding product limits. Ethical providers educate their clientele on operating limits and maintenance advice to prevent misuse. They often offer detailed guidance on installation techniques, potential signs of wear, and the importance of scheduled maintenance to extend the lifespan of their products. A reliable supplier values long-term client relationships by prioritizing product performance and client safety over short-term gains.
In conclusion, the intricate world of high-temperature oil seals encompasses a harmonious blend of expertise in material science, experience in industrial applications, authoritative design and manufacturing processes, and unwavering trust in product delivery. When selecting these seals, prioritize proven effectiveness, adherence to standards, and comprehensive support to ensure that your industrial machinery runs efficiently and safely under high-temperature conditions. Choosing the right high-temp oil seal is not just about performance; it's about securing operational longevity and preventing unnecessary downtimes. With the proper seal, industries can face high temperatures confidently, safeguarding both equipment and productivity.