High temperature oil seals are crucial components in many industrial and automotive applications, where they play an indispensable role in maintaining the performance and durability of machinery. An understanding of the expertise required, their operational mechanics, and authoritative insights into their use can greatly enhance the effectiveness of equipment in high-temperature environments.
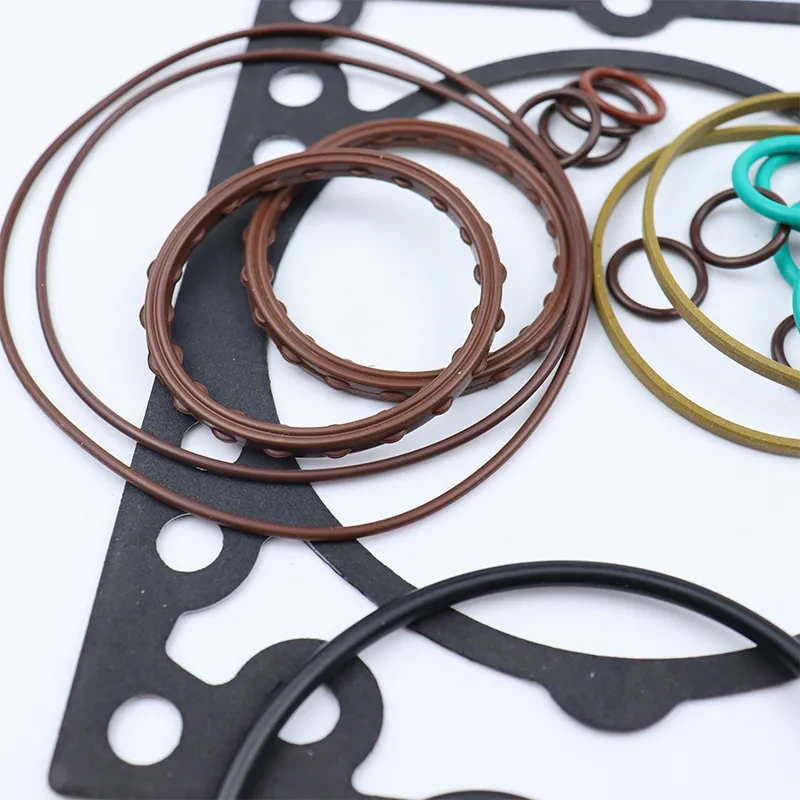
Experience with high temperature oil seals reveals that they are designed to withstand extreme conditions, including elevated temperatures that can reach up to 300°C or more. These seals are used in applications such as automotive engines, aerospace systems, and industrial machinery, where thermal stresses are common. Users often face challenges with regular oil seals under these conditions as they can suffer degradation, leading to leakage and eventual equipment failure. Real-world experiences underscore the importance of selecting the right seal, guided by an understanding of the operational environment and specific requirements of the machinery involved.
Expertise in the field of high temperature oil seals involves a comprehensive understanding of materials science and engineering. The seals are typically made from advanced materials like fluorocarbon rubber, silicone, and polytetrafluoroethylene (PTFE), which are known for their resistance to heat and chemical degradation. Professionals in this area must possess knowledge about the mechanical properties of these materials, as well as insights into how they interact with lubricants and other substances at high temperatures. It's imperative for engineers to stay updated with the continuous advancements in material technology, ensuring their choices are both innovative and practical.
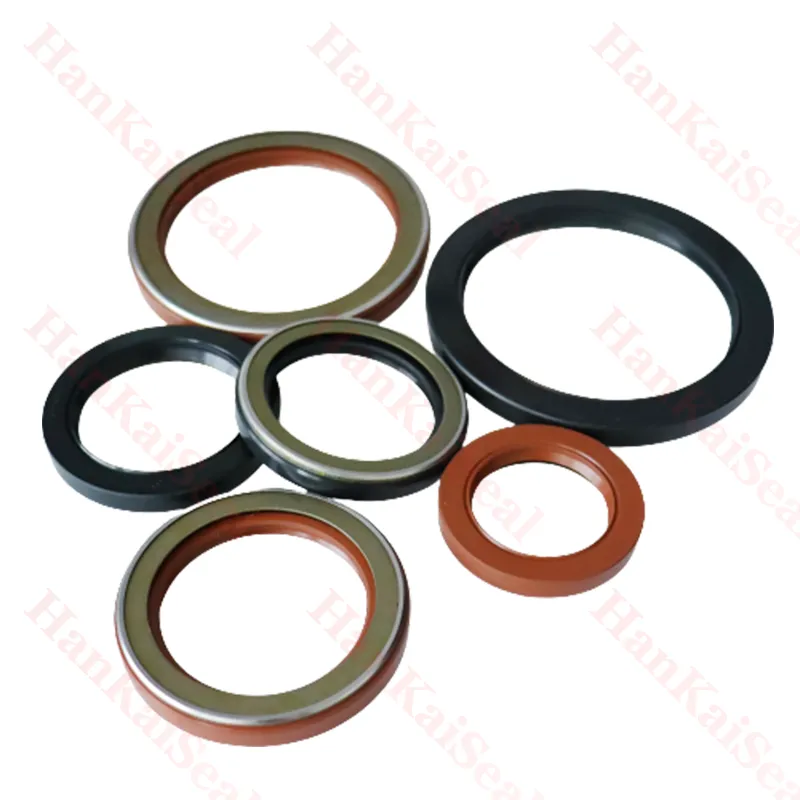
high temperature oil seal
Authoritativeness comes into play as industry standards and certifications guide the production and application of high temperature oil seals. Renowned organizations, such as the Society of Automotive Engineers (SAE) and the International Organization for Standardization (ISO), provide guidelines and benchmarks to ensure quality and reliability. Industry experts often point to the adherence to these standards as a sign of a trustworthy product. Engaging with authoritative voices, through technical seminars or professional forums, can also provide valuable insights, helping practitioners make informed decisions that enhance operational efficiency while minimizing risks.
Trustworthiness in high temperature oil seals is fundamental, as failure can lead to significant downtime and costly repairs.
Trust is built through rigorous testing and validation processes. Many manufacturers conduct extensive trials, simulating real-world conditions to ensure their products can withstand the claimed temperature ranges and stresses. Testimonials from industry professionals who have successfully used these products further add to the credibility. Moreover, a transparent customer service approach by manufacturers, offering technical support and clear information on product specifications, strengthens the trust customers place in high temperature oil seals.
In conclusion, the selection and use of high temperature oil seals require a blend of experience, expertise, authoritativeness, and trustworthiness. By drawing on comprehensive knowledge of material properties, adhering to industry standards, and engaging with credible sources, businesses can optimize the performance of machinery operating under extreme temperature conditions. Whether it's prolonging engine life or ensuring the efficiency of an industrial process, the right high temperature oil seal is a vital piece of the puzzle in modern engineering challenges.