Choosing the right high temperature oil seal is essential for ensuring the longevity and efficiency of machinery operating under extreme conditions. These seals play a critical role in preventing leaks and contaminants from entering the machinery, thus safeguarding its optimal performance. Derived from firsthand experiences and years of expertise in the field, here are some authoritative insights into selecting high temperature oil seals.
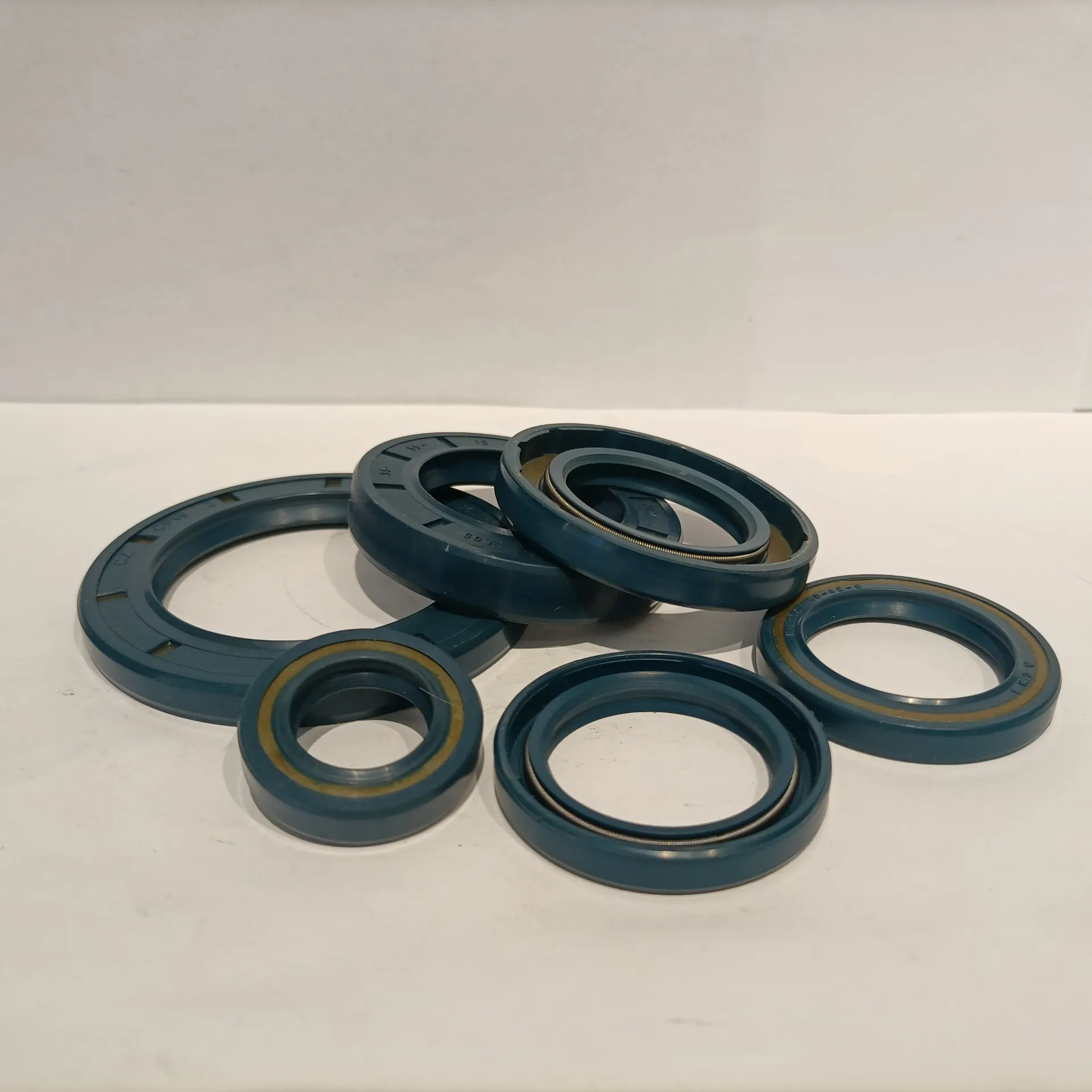
Understanding the Material The choice of material is paramount when it comes to high temperature oil seals. Materials such as Viton, Silicone, and PTFE stand out due to their exceptional heat resistance. Viton, for instance, can handle temperatures up to 400°F, making it ideal for automotive and aerospace applications. Silicone seals, on the other hand, offer flexibility and resilience over a wide temperature range, outlasting many other materials in harsh environments. For extreme conditions, PTFE seals can withstand temperatures up to 500°F, offering both robustness and chemical inertness.
Application-Specific Design Different applications demand specific seal designs to handle various loads, shaft speeds, and fluid types. In the automotive industry, where high-speed shafts are common, seals with auxiliary lips and enhanced materials may be required to handle the dynamic environments. Conversely, for static applications in heavy machinery, seals designed with a focus on pressure and environmental resistance are more suitable.
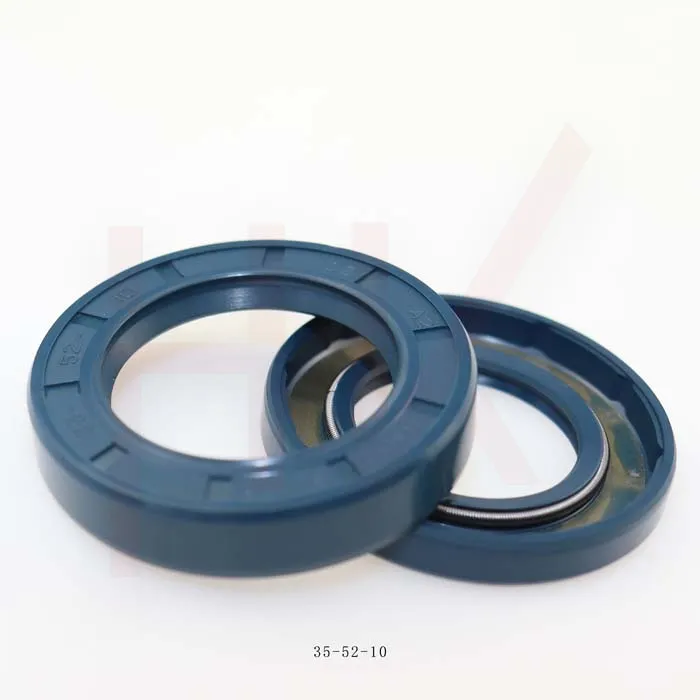
Performance Under Pressure High temperature oil seals are often used in pressurized environments. The balance between maintaining a seal against high-temperature fluids and ensuring minimal friction is a delicate one. Modern designs incorporate features such as hydrodynamic aids, which enhance seal performance by creating a thin film of lubricant between the seal and the shaft, reducing wear and extending the seal's life.
high temperature oil seal
Long-Term Reliability Experience teaches that the longevity of high temperature oil seals is not just a function of their material but also their compatibility with the operating environment. Using seals in environments with unexpected chemical exposures or beyond their rated temperature range often results in premature failure. Therefore, it is crucial to understand the entire operating environment—including fluid types, pressures, and any potential contaminants—to ensure the chosen seal can withstand all conditions it may encounter.
Maintenance and Inspection Regular maintenance and inspection of high temperature oil seals contribute significantly to their reliability and performance. During inspections, checking for signs of wear, thermal degradation, and chemical damage can prevent costly downtimes. Early identification of issues allows for proactive maintenance strategies, which is far more beneficial than reactive approaches that could lead to unexpected machinery failures.
Trust in Proven Brands While there are numerous manufacturers of high temperature oil seals, opting for products from reputable brands provides an added layer of confidence. Established brands have extensive testing procedures and quality control measures, ensuring that their seals provide the expected performance under demanding conditions. Collaborating with these brands often offers technical support and guidance, enhancing the overall reliability of the machinery using these seals.
In conclusion, while selecting a high temperature oil seal for any machinery, prioritizing material composition, application compatibility, and brand reliability creates a sturdy foundation for achieving optimal performance and longevity. By adhering to these expert guidelines, industries can not only prevent operational inefficiencies and premature machinery failures but also enhance their productivity and maintain a competitive edge.