High pressure shaft seals play a pivotal role in numerous industrial applications, ensuring the safe and efficient operation of machinery by preventing the leakage of fluids. These components are crucial in industries ranging from aerospace to manufacturing, where maintaining the integrity of high-pressure systems is paramount. The demand for more reliable and durable high-pressure shaft seals has spurred innovation, resulting in a new wave of products that are setting benchmarks for performance and dependability.
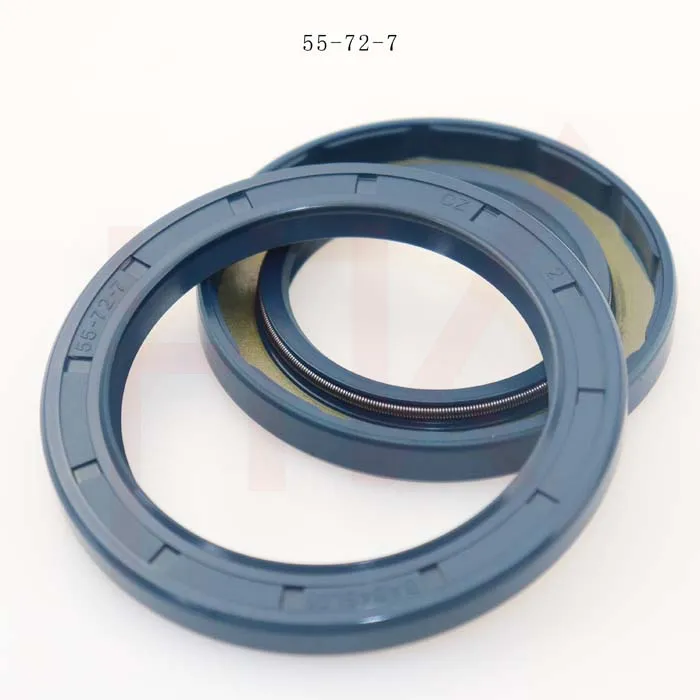
One of the critical advancements in the realm of high pressure shaft seals is the development of materials that can withstand extreme conditions. Modern seals are often crafted from composite materials that offer superior resistance to temperature fluctuations, corrosive substances, and high-pressure environments. These materials not only extend the life of the seals but also provide consistent performance under demanding conditions.
This is a game-changer for industries where even a minor leak could lead to catastrophic consequences.
Moreover, the design of high pressure shaft seals has evolved to include advanced features that enhance their functionality. For example, labyrinth seal designs incorporate intricate paths that effectively trap contaminants, reducing the risk of damage and wear. This innovation significantly enhances the seal's longevity, which translates to lower maintenance costs and less frequent replacements. Companies investing in these advanced designs often report a marked improvement in the operational efficiency and longevity of their machinery.
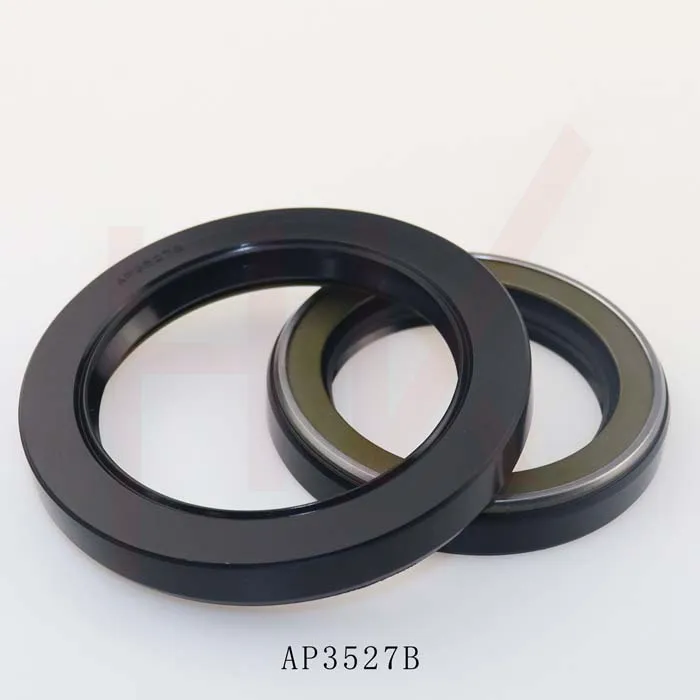
Expertise in the industry is notably marked by manufacturers who prioritize rigorous testing and validation of their seal products. These evaluations simulate real-world conditions, ensuring that the seals can withstand the stresses they will encounter in actual applications. Such dedication to testing not only serves as a testament to product reliability but also builds trust with consumers who depend on these components for the safe function of their equipment.
high pressure shaft seals
From an authoritative perspective, high pressure shaft seals are often subjected to strict compliance standards, ensuring they meet international safety and performance criteria. This regulatory oversight serves as an assurance to end-users that the products they are deploying in critical applications have been vetted for quality and safety. Seal manufacturers that achieve certifications such as ISO 9001 are regarded as more credible, which is vital for building long-term relationships with clients.
In terms of real-world experience, numerous industry case studies highlight the transformative impact of implementing high-performance shaft seals. For instance, a leading energy company documented a 30% reduction in system downtimes after upgrading to seals made from advanced composite materials. Such empirical evidence of their effectiveness provides a compelling incentive for other businesses to consider similar upgrades.
Trustworthiness, an indispensable attribute for any product, is cultivated through a commitment to transparency and customer support. Leading manufacturers offer comprehensive warranties and robust customer service, ensuring that any issues are swiftly addressed to minimize operational disruptions. In an industry where delays can lead to significant financial losses, these attributes are particularly valued.
In summary, high pressure shaft seals are more than just a functional component of industrial machinery; they represent the culmination of advanced material science, innovative engineering, and rigorous quality assurance. By choosing the right seals, industries not only safeguard their operations but also optimize performance, reduce costs, and ensure safety. As the demands on industrial systems continue to grow, the role of these seals will become even more critical, cementing their place as an essential element of modern engineering solutions.