High pressure rotary seals are a critical component in many industrial applications, primarily serving the purpose of maintaining a seal in environments where fluids are subjected to intensive pressure and rotary motion. Understanding these seals requires a deep dive into their design, functionality, and application in real-world operations.
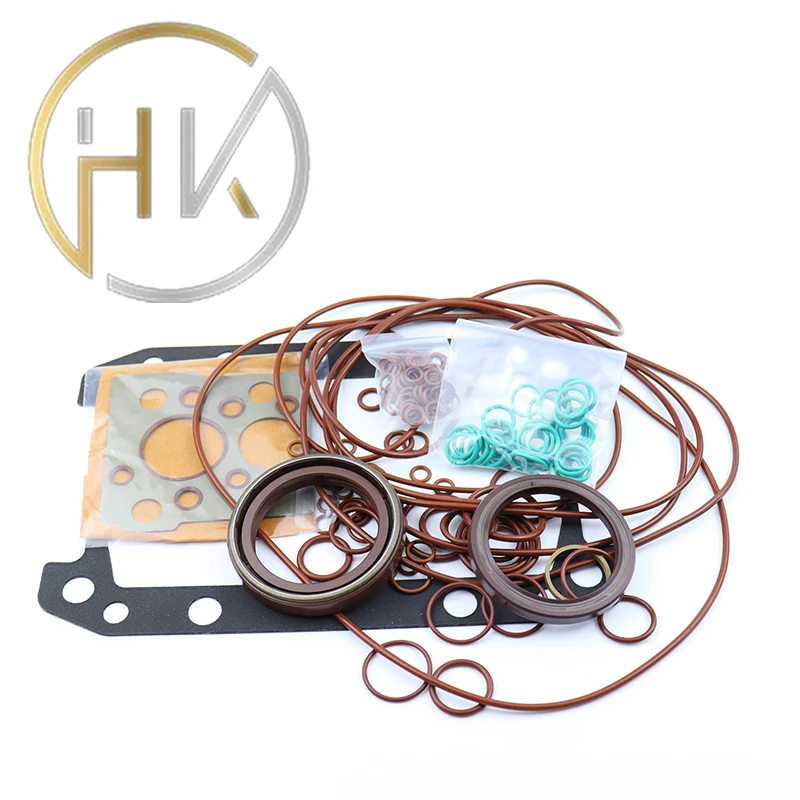
Rotary seals are engineered to facilitate the transfer of fluid or gas between two distinct systems while preventing contamination and leakage.
In high-pressure scenarios, their role becomes even more vital. Such environments might involve handling hydraulic fluids in manufacturing machinery or ensuring effective power transmission in heavy-duty equipment. The meticulous design of high-pressure rotary seals is what sets them apart, typically employing advanced materials capable of withstanding not only the pressure but the friction and heat generated by continuous rotary action.
A vital experience when dealing with high-pressure rotary seals is the understanding of material selection. The unique properties of elastomers or polymers used in these seals are crucial. PTFE (polytetrafluoroethylene), FKM (fluorocarbon rubber), and other proprietary compounds are popular due to their resilience and ability to perform under extreme temperatures and pressures. In certain high-speed applications, the introduction of specialized bearing elements within the seals can further reduce friction and wear, enhancing the seal's longevity.
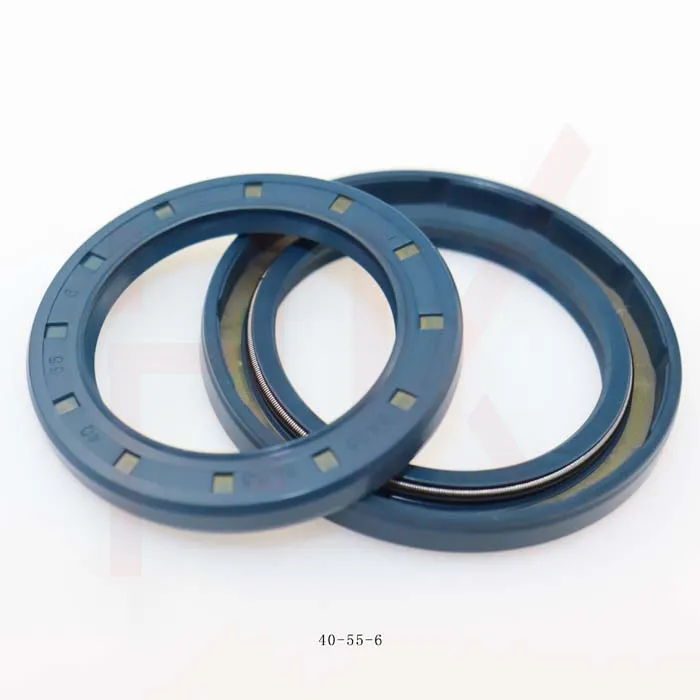
In terms of expertise, an emphasis on precision engineering cannot be overstated. The development of rotary seals involves rigorous testing to ensure that they can handle the specific demands of an application. This includes extensive stress testing, analysis of material fatigue, and trials in simulated environments that mimic actual operational conditions. Manufacturers invest significantly in research and development to push the boundaries of what these seals can do, ensuring they meet the highest standards of efficiency and reliability.
high pressure rotary seal
The authority of high-pressure rotary seals lies in their widespread adoption across multiple industries. Consider the automotive industry, where they play a pivotal role in power steering systems, and the oil and gas sector, where their integrity is essential in pipeline systems subject to high pressures. This cross-industry application reflects the comprehensive trust placed on these seals by engineers and technologists. Such seals are designed according to industry standards, such as ISO and SAE, providing peace of mind that they will perform as intended under the most challenging conditions.
Trustworthiness is further established by the extensive field testing and failure analysis studies conducted by leading seal manufacturers. These studies help in understanding the failure modes that seals might encounter and devising strategies to mitigate them. Customers are encouraged to look for manufacturers who provide detailed data on the testing conducted as well as customer testimonials and case studies, which add an additional layer of trust.
For professionals seeking to implement high-pressure rotary seals in their systems, collaboration with seal manufacturers during the design phase can lead to customized solutions tailored specifically to operational requirements. This collaboration ensures that seals not only meet the design specifications but also can handle unexpected variances in operating conditions. Furthermore, the inclusion of monitoring systems to track wear and tear in real-time can preemptively address maintenance concerns, further enhancing the operational reliability of these seals.
In conclusion, high-pressure rotary seals are indispensable components in modern machinery, embodying a blend of advanced material science, engineering precision, and tested reliability. Their ability to perform in challenging environments while maintaining system integrity makes them a cornerstone of various industrial applications. Whether in automotive, aerospace, or heavy machinery, the right high-pressure rotary seal can significantly enhance operational efficiency and longevity, underscoring the importance of selecting the right partner for your sealing needs.