High pressure pump seals are integral to the efficiency and longevity of any system that relies on a high pressure pump. These critical components ensure that fluids are contained securely within the system, preventing leaks and maintaining consistent operational performance. Through years of hands-on experience, it's evident that choosing the right seal can significantly impact system reliability, maintenance costs, and even safety.

A high pressure pump seal functions by creating a barrier between the high pressure environment within the pump and the outside. Its primary purpose is to prevent the escape of the medium being pumped, whether it's a liquid or gas. Inefficient sealing can lead to system downtime, environmental contamination, and potentially hazardous conditions. Selecting a seal that's engineered specifically for high pressure conditions is crucial.
When selecting a high pressure pump seal, several factors must be considered to ensure optimal performance. First, understanding the operating environment is key. This includes noting the temperature,
pressure, and the chemical nature of the fluid. For instance, seals used in petroleum industries must withstand high temperatures and corrosive materials, whereas those in food processing must be able to maintain integrity in both high pressure and varying temperature scenarios.
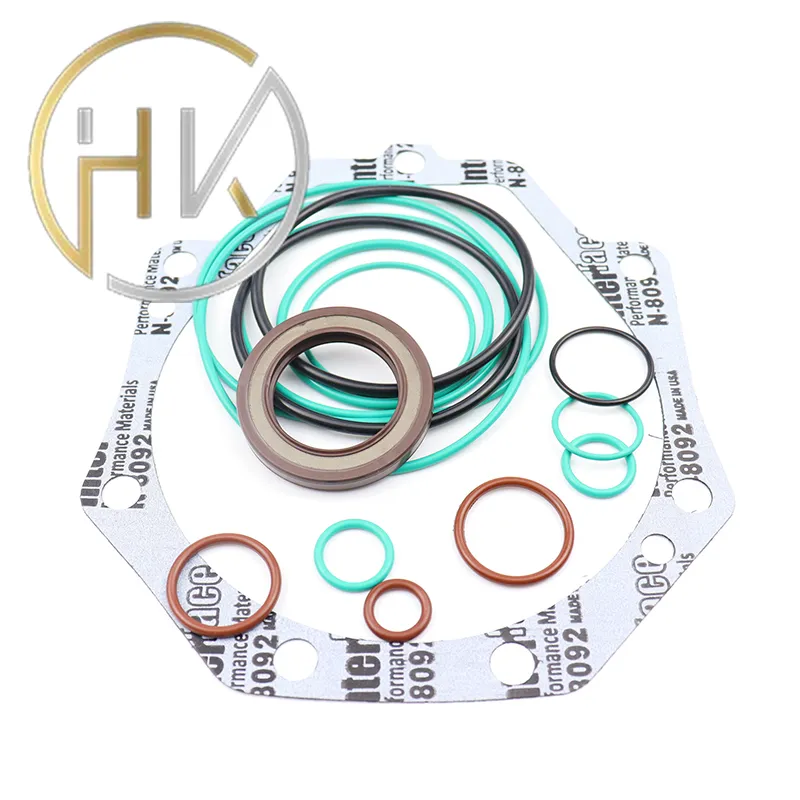
Material choice plays a pivotal role in the seal's effectiveness. For high pressure applications, materials such as polytetrafluoroethylene (PTFE), ethylene propylene diene monomer (EPDM), and fluorocarbon are preferred due to their robust resistance to pressure, temperature extremes, and chemical exposures. These materials ensure a long-lasting seal, reducing maintenance intervals and increasing the system's uptime.
Moreover, the design of the seal is paramount. Mechanical seals, for instance, offer excellent sealing capabilities for high pressure environments. They are composed of two precision-engineered surfaces a stationary surface and a rotating-ring surface. The interaction between these surfaces, maintained by a fluid film, prevents leakage even under extreme pressures. Given their complexity, it’s imperative that these seals are installed and maintained by professionals with extensive expertise.
high pressure pump seal
Advanced sealing technologies have emerged in recent years, offering innovative solutions to industries facing particularly challenging high pressure applications. Bi-directional seals, for example, are designed to hold pressure from both directions, accommodating systems that experience fluctuating pressure levels.
Trustworthiness in a high pressure pump seal is built through rigorous testing and certification processes. Reputable manufacturers not only comply with industry standards such as API or ISO but often seek additional certifications that validate their seal's reliability under specified high pressure conditions. It’s essential to assess these credentials when choosing a seal provider to ensure that the product has been tested under realistic conditions.
Understanding the financial and operational impact of high pressure pump seals is equally important. A high-quality seal reduces unexpected maintenance and replacement costs, providing comprehensive protection against operational failures that could lead to costly downtime. In industries where high pressure pumps are critical to operations, the cost of a seal is a fraction of the value it protects.
In summary, high pressure pump seals are not mere accessories but are critical components ensuring the safe and efficient operation of high pressure systems. Expertise in selecting the right seal involves understanding material compatibility, pressure and temperature ratings, as well as the demands of specific applications. Relying on seals from authoritative, certified manufacturers builds trust and assurance in system reliability. Well-chosen, expertly-installed seals promise improved operational longevity and safety, which is the hallmark of effective high pressure systems in diverse industrial applications.