High pressure oil seals are critical components across various industrial sectors, offering a pivotal role in maintaining system integrity under extraordinary conditions. Understanding the intricacies of these seals is essential not just for optimal system performance, but also for ensuring the longevity of the equipment they protect.
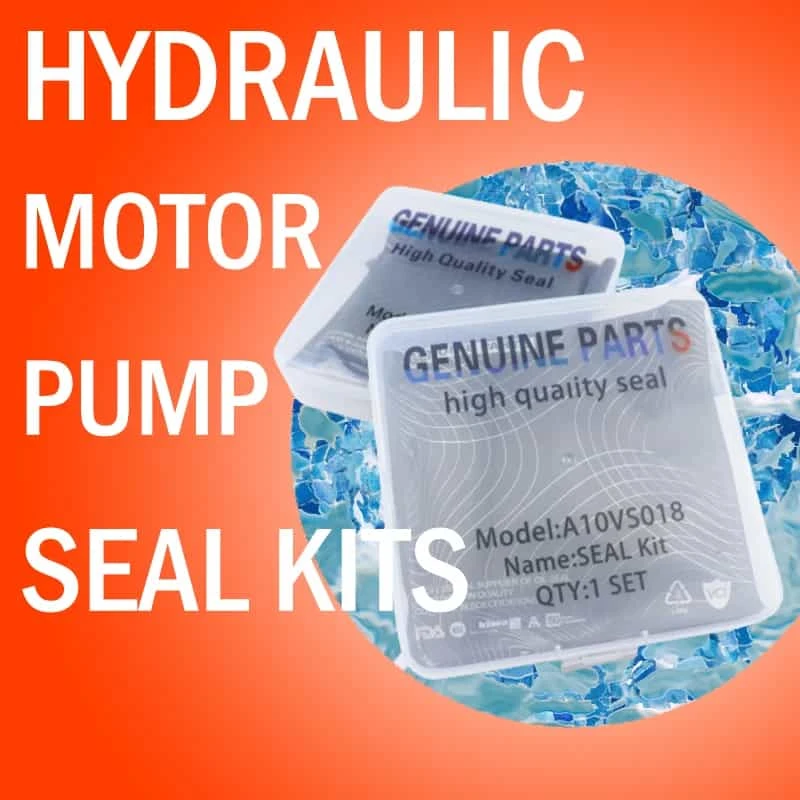
The principal function of high pressure oil seals is to prevent the leakage of fluids, particularly under demanding environmental and operational conditions. These seals act as a barrier, retaining lubricants within mechanical systems and preventing contaminants from entering. This dual functionality is crucial, as it helps reduce wear and tear on the machinery, ultimately leading to extended service life and enhanced efficiency.
Designing high pressure oil seals involves a meticulous process that takes into account the type of fluid, pressure levels, temperature conditions, and the operational environment. Common materials employed in the manufacturing of these seals include nitrile rubber, fluorocarbon, and silicone, each offering unique benefits. Nitrile rubber is renowned for its excellent oil resistance and low-temperature performance, while fluorocarbon excels under high temperatures with superior chemical resistance. Silicone, on the other hand, is often favored for its flexibility and resilience across a broad temperature range.
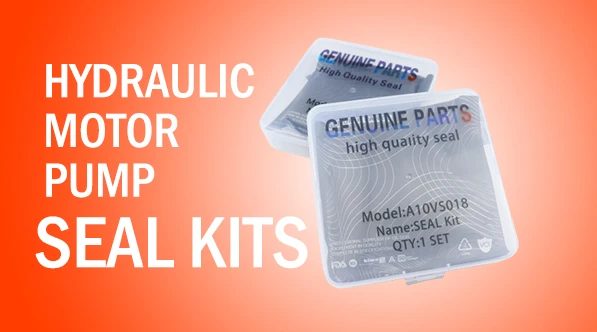
The manufacturing process also incorporates precision engineering to ensure that the seals can withstand high pressure without compromising their structural integrity. This precision is achieved through advanced production techniques and stringent quality control measures. Manufacturers rely on cutting-edge technology to produce seals that fit perfectly in various industrial applications, ranging from automotive to aerospace and marine industries.
Regular maintenance and timely replacement of high pressure oil seals are critical to ensure the smooth operation of machinery. Due to their constant exposure to high pressure and temperature fluctuations,
these seals can degrade over time, leading to potential leaks and system failures. By adhering to a robust maintenance schedule, operators can detect early signs of wear and replace the seals before they compromise system integrity.
high pressure oil seals
Selecting the right high pressure oil seals is not merely about material choice but also involves assessing the specific needs of the application. Factors such as rotational or reciprocating motion, exposure to different chemicals, and varying pressure dynamics can significantly influence the performance of these seals. Consulting with experienced professionals or manufacturers can provide valuable insights into selecting the most suitable seal for the task at hand.
Advancements in seal technology continue to push the boundaries of performance. Innovations in seal design, such as spiral wound gaskets and advanced lip configurations, are enhancing the capability of high pressure seals, allowing them to perform efficiently under ever-increasing pressure demands. These advancements not only boost the performance efficacy but also reduce maintenance costs by extending the seals' operational lifespan.
Industry professionals must stay abreast of these innovations and continuously evaluate the performance of their seals in operational contexts. Leveraging analytical tools and predictive maintenance strategies can provide foresight into seal performance, enabling proactive interventions that prevent unscheduled downtimes and costly repairs.
In conclusion, high pressure oil seals serve as vital components within various mechanical systems, assuring both efficiency and safety. Through careful selection, regular maintenance, and an understanding of the latest technological developments, businesses can maximize their investment in high pressure sealing solutions. Expertise in this domain can lead to enhanced system reliability, improved operational uptime, and ultimately, greater fiscal efficiency.