High pressure lip seals are increasingly becoming crucial components in various industrial applications, offering superior performance compared to traditional sealing solutions. These seals are designed to withstand extreme pressures, prevent leakages, and prolong the life of equipment by maintaining optimal functioning even under the toughest conditions.
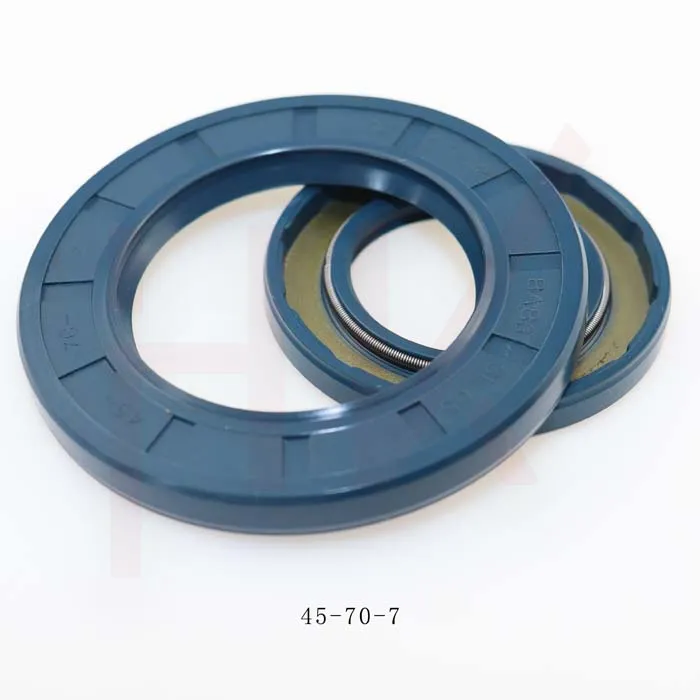
Industries such as automotive, aerospace, and oil & gas heavily depend on these reliable seals for applications that involve rotating components under high-pressure environments. The flawless operation in these critical applications is often contingent on the performance of the seal, making high pressure lip seals indispensable.
Users with extensive experience in automotive manufacturing have noted the significant difference high pressure lip seals make in engine and powertrain efficiency. These seals are adept at handling the intricate needs of engines that run at high RPMs, ensuring that lubricants stay within the designated areas while contaminants are kept out. This not only enhances engine performance but also contributes to maintenance cost reduction and extended machinery lifespan.
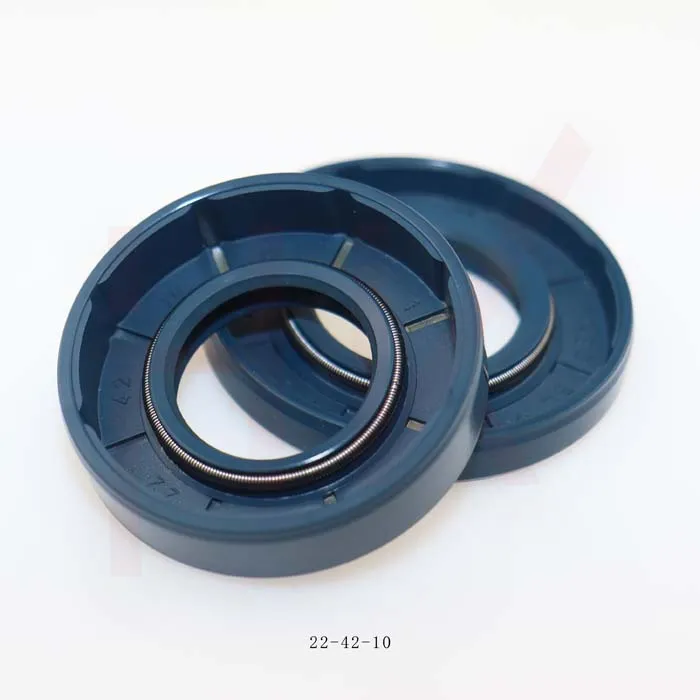
The unique construction of high pressure lip seals incorporates advanced materials specifically engineered to provide superior durability and resilience. Materials such as fluoroelastomers, PTFE (Polytetrafluoroethylene), and various high-grade elastomers are commonly used. Recognized experts in material science affirm that these substances offer excellent chemical resistance and temperature stability, essential for effective sealing in demanding applications.
From a technical standpoint, the design of high pressure lip seals involves sophisticated engineering to perfectly match the operational dynamics of the equipment. Specialists emphasize the importance of features like hydrodynamic aids in the seal lips, which enhance sealing performance by generating a pumping action that helps maintain a tight seal even under varying pressure conditions. These improvements have been validated through rigorous testing and user feedback, solidifying their authoritative presence in the field.
high pressure lip seal
Engineers from established aerospace companies report that high pressure lip seals are crucial not only for their sealing capabilities but also for ensuring reliability and safety in flight operations. Seal failures in aerospace components can be catastrophic, and the trustworthiness of these seals is proven through their successful application in numerous aircraft models over the years.
The trust in high pressure lip seals extends from impeccable manufacturing practices to their traceability and compliance with international standards. Top suppliers provide extensive documentation and certification, guaranteeing that their products meet stringent quality requirements.
This traceability is an added layer of reassurance for users across industries.
Moreover, the seals' adaptability to custom requirements underscores their versatility. Manufacturers provide bespoke solutions tailored to specific needs, ranging from adjustments in seal dimensions to custom material formulations, ensuring optimal functionality in diverse operational environments.
In conclusion, the growing reliance on high pressure lip seals across various sectors is testament to their exceptional performance, reliability, and adaptability. Whether it's preventing fluid leakage in high-performance engines or maintaining pressure integrity in aerospace applications, these seals stand out as critical components. As industries evolve, the demand for high pressure lip seals is anticipated to increase, driven by innovations that promise even greater levels of efficiency and reliability. Thus, businesses looking to enhance their operational efficiency and product reliability can greatly benefit from investing in high pressure lip seals, securing a competitive edge in today's demanding markets.