High-Pressure Rotary Seals A Comprehensive Guide
In the realm of industrial machinery, high-pressure rotary seals play a crucial role in maintaining the integrity of systems that operate under extreme conditions. These seals are designed to withstand high pressures, ranging from a few hundred PSI to several thousand PSI, and rotate at high speeds, often exceeding 1000 RPM. Their primary function is to prevent the leakage of fluids or gases from the system while allowing for smooth rotation.
The construction of high-pressure rotary seals is typically a combination of materials that can withstand both the mechanical stresses imposed by rotation and the chemical assaults of the fluids being sealed. The seal face, which comes into direct contact with the rotating shaft or housing, is usually made of a material with excellent wear resistance, such as carbon, silicon carbide, or tungsten carbide. The backup ring, which provides support and helps maintain the seal's shape under pressure, is often made of a softer material like nitrile rubber orPTFE (polytetrafluoroethylene).
One of the key challenges in designing high-pressure rotary seals is to create a seal that can accommodate the dynamic movements of the shaft without compromising its sealing capabilities. To achieve this, many seals incorporate features such as flexible lip seals, spring-loaded seals, or hydrodynamic grooves that allow the seal to conform to the shaft's surface and maintain a tight seal even under fluctuating conditions.
Another important consideration when selecting a high-pressure rotary seal is the fluid being sealed. Different fluids have different properties that can affect the seal's performance Different fluids have different properties that can affect the seal's performance
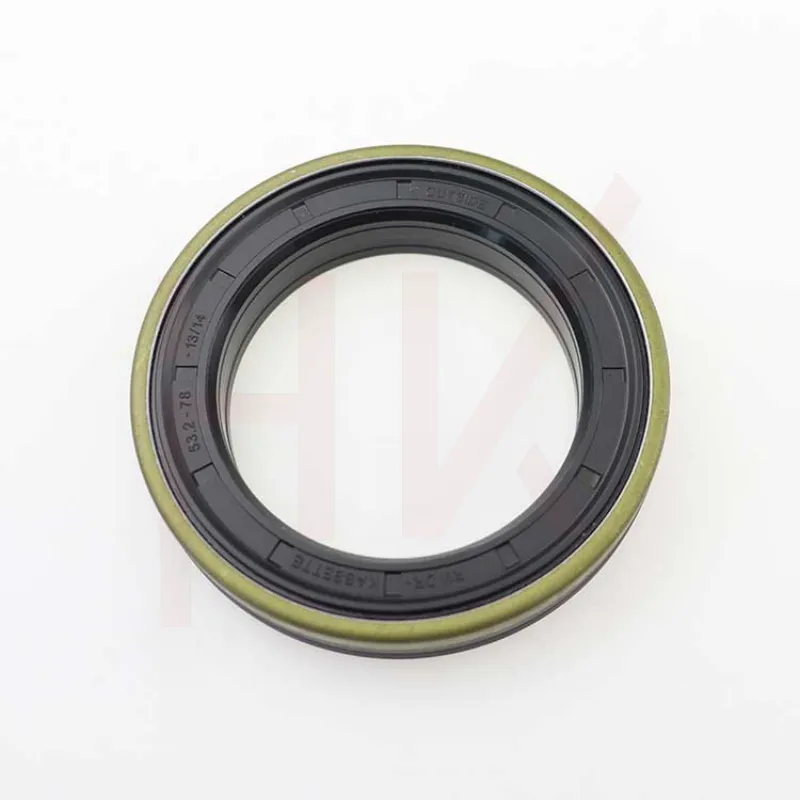
Different fluids have different properties that can affect the seal's performance Different fluids have different properties that can affect the seal's performance
high pressure rotary seal. For example, oils and greases may require a different type of seal than water or chemicals. It is essential to choose a seal that is compatible with the fluid and can withstand its specific properties, such as viscosity, temperature, and corrosiveness.
Maintenance is also a critical aspect of ensuring the longevity and reliability of high-pressure rotary seals. Regular inspection and replacement of worn or damaged components can prevent leaks and costly downtime. It is recommended to follow the manufacturer's guidelines for maintenance and to consult with a professional if any issues arise.
In conclusion, high-pressure rotary seals are essential components in many industrial processes that demand reliable sealing under extreme conditions. By understanding their design, materials, and maintenance requirements, engineers and operators can select the right seal for their application and ensure the long-term success of their operations.