Understanding gearbox seals and their vital role in machinery functionality is essential for anyone involved in mechanical engineering or industrial maintenance. Gearbox seals are crucial components that ensure the longevity and performance of any mechanical system.
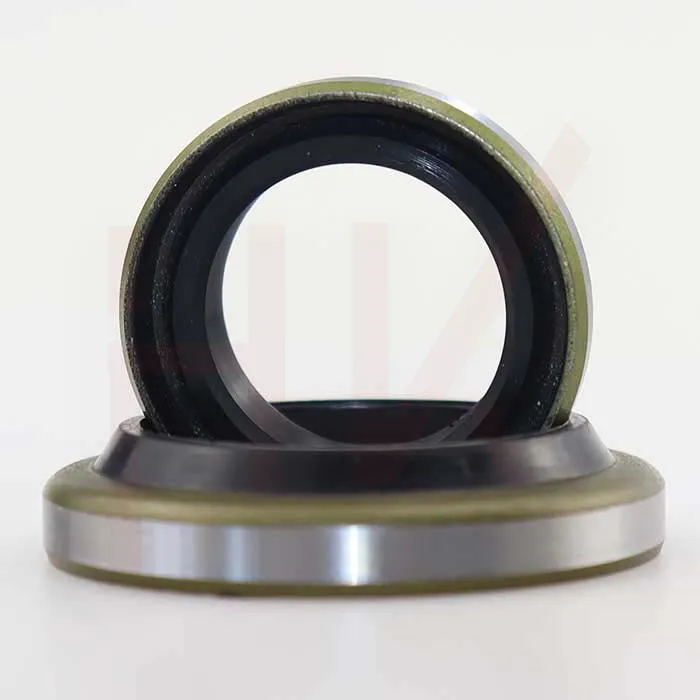
Gearbox seals prevent lubricant leakage and protect internal components from external contaminants like dust, dirt, and moisture. This dual function is essential in maintaining operational efficiency and reducing the risk of mechanical failures. A malfunction in a gearbox seal can lead to significant consequences such as increased wear and tear, overheating, and even complete system breakdowns. Therefore, understanding the different types of gearbox seals and how to choose the right one is paramount for ensuring optimal operational efficiency.
Gearbox seals are not universally interchangeable. They must be carefully selected based on the specific requirements of the application. Factors to consider include temperature range, pressure, rotational speed, and chemical compatibility of the lubricant. These parameters determine the suitability of a seal for a particular application. For instance, seals intended for high-speed applications must be able to withstand greater centrifugal forces without losing their seal integrity. Similarly, seals used in environments with aggressive chemicals must resist corrosion and degradation.

The most commonly used gearbox seals are lip seals, labyrinth seals, and magnetic seals. Lip seals, often made from synthetic rubber, are used in applications requiring a tight seal and where rotational speed is a critical factor. Their design allows them to maintain contact with the shaft, preventing leakage even under varying pressure conditions. Labyrinth seals, on the other hand, are non-contact seals that use a series of passages to create a maze for the fluid, significantly reducing the likelihood of leakage. They are ideal for applications where minimizing friction is important. Magnetic seals are the latest innovation in gearbox sealing technology. They utilize magnetic fields to maintain a seal at the molecular level, offering superior leak prevention even under extreme conditions.
gearbox seals
Installation and maintenance of gearbox seals also play a crucial role in their effectiveness. Improper installation can lead to premature seal failure and unplanned downtime. It's crucial to follow manufacturer guidelines and use the correct tools and techniques during installation. Regular maintenance checks should include visual inspections for signs of wear, cracking, or deformation. Spotting these issues early can prevent more severe problems and extend the life of both the seal and the gearbox itself.
Moreover, relying on reputable manufacturers for gearbox seals is fundamental to ensuring reliability and performance. Trusted manufacturers provide seals that adhere to rigorous quality standards and are subjected to comprehensive testing to verify their reliability under various conditions. Additionally, these manufacturers often offer expert guidance in selecting the most appropriate seals for a given application, thereby enhancing the trustworthiness and authority of your machinery setup.
Incorporating high-quality gearbox seals into your machinery not only enhances performance but also contributes significantly to overall cost savings. Well-functioning seals reduce the frequency and extent of repairs needed and extend the lifespan of your machinery. This translates to lower operational costs and a reduced need for expensive, time-consuming overhauls. Furthermore, by ensuring the optimal performance of gearboxes, seals also contribute to energy efficiency, reducing power consumption and thereby supporting sustainability efforts within your operations.
In conclusion, gearbox seals are indispensable for ensuring the reliability and efficiency of mechanical systems. By understanding the various types of seals, their applications, and maintenance, businesses can significantly reduce operational risks and costs. Investing in quality seals and adhering to best practices in installation and maintenance strengthens machinery performance and aligns with sustainable operational objectives. As technology advances, the continued evolution of gearbox seals promises even greater efficiencies and application possibilities, making them an essential focus for mechanical engineers and plant operators aiming to attain excellence in their operational outcomes.