Dust Seal vs Oil Seal A Comparative Analysis
In the world of mechanical components, seals play a crucial role in ensuring the smooth functioning of various systems. Among the different types of seals available, dust seals and oil seals are two popular options. While both serve the purpose of sealing, they differ in their design, application, and performance. This article aims to explore the differences between dust seals and oil seals, highlighting their unique features and benefits.
Dust seals, as the name suggests, are designed to prevent the entry of dust and other contaminants into a mechanical system. They are typically made of materials such as rubber or plastic and feature a flexible lip that creates a tight seal around a shaft or rotating component. Dust seals are commonly used in applications where there is a risk of dust or debris entering the system, such as in automotive suspension systems, industrial machinery, and aerospace equipment.
On the other hand, oil seals are specifically designed to prevent the leakage of oil or lubricant from a mechanical system. These seals are usually made of materials like elastomers or metals and feature a rigid structure with a lip that creates a barrier against oil leakage. Oil seals are commonly used in engines, gearboxes, pumps, and other lubricated components where oil retention is critical.
One significant difference between dust seals and oil seals is their ability to handle pressure. Dust seals are not designed to withstand high pressures and are primarily focused on preventing contaminants from entering the system Dust seals are not designed to withstand high pressures and are primarily focused on preventing contaminants from entering the system
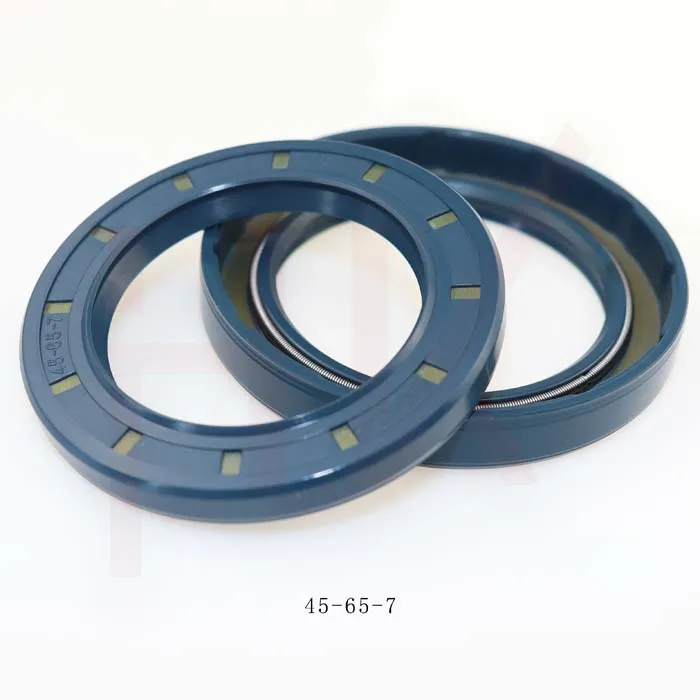
Dust seals are not designed to withstand high pressures and are primarily focused on preventing contaminants from entering the system Dust seals are not designed to withstand high pressures and are primarily focused on preventing contaminants from entering the system
dust seal vs oil seal. In contrast, oil seals are designed to handle higher pressures and prevent oil from leaking out of the system under these conditions.
Another key difference lies in their compatibility with different types of fluids. Dust seals are generally not compatible with oils or lubricants, as they are not designed to handle these fluids. Oil seals, however, are specifically designed to be compatible with various types of oils and lubricants, ensuring effective sealing without any leakage.
In terms of installation and maintenance, both dust seals and oil seals require proper fitting and regular inspection for wear and damage. However, oil seals may require more frequent maintenance due to their exposure to high temperatures and pressures, which can cause them to degrade over time.
In conclusion, while both dust seals and oil seals serve the purpose of sealing, they differ significantly in their design, application, and performance. Dust seals are best suited for applications where contaminant exclusion is crucial, while oil seals are ideal for lubricated components where oil retention is essential. By understanding the unique features and benefits of each type of seal, engineers and technicians can make informed decisions when selecting the appropriate seal for their specific application.