A double lip seal, pivotal in ensuring the reliability and efficiency of various machinery, serves as a protective barrier against contaminants while retaining lubricants. Incorporated in diverse applications—from automotive to industrial machinery—these seals underscore the crucial aspects of durability and performance in equipment maintenance.
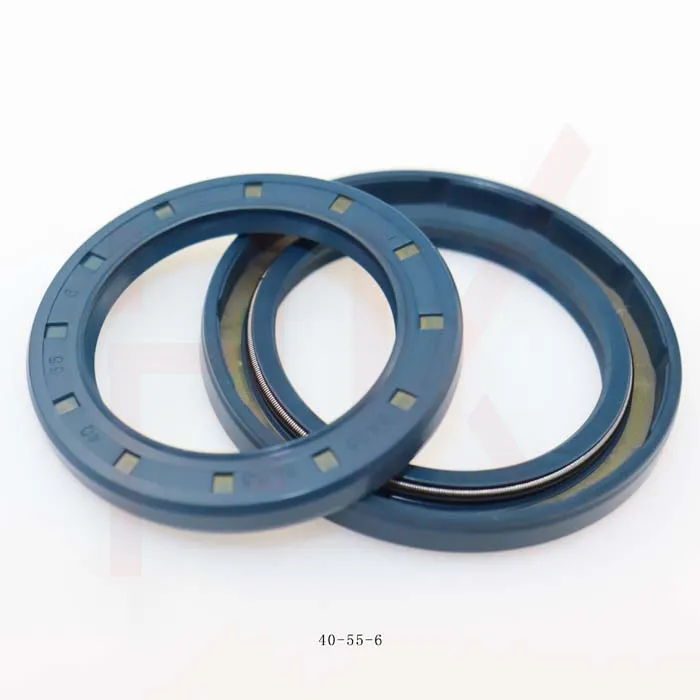
Drawing from extensive experience in the engineering field, the complexity of the double lip seal design stands out as a testament to its ingenuity. Consisting of two distinct sealing lips, one faces outwards to block external contaminants like dust and moisture, while the other faces inwards, maintaining lubricant integrity within the system. This dual action not only enhances the lifespan of machinery but also ensures efficient operation by minimizing friction and wear on mechanical components.
From an expertise standpoint, selecting the appropriate material for a double lip seal is critical. The choice of elastomers such as nitrile rubber,
silicone, or fluorocarbon depends heavily on the operational environment. Nitrile rubber, for instance, thrives in moderate temperature ranges and is resistant to oils, making it suitable for automotive applications. On the other hand, fluorocarbon is preferred in high-temperature settings due to its superior resistance to heat and chemicals, making it ideal for industrial applications.
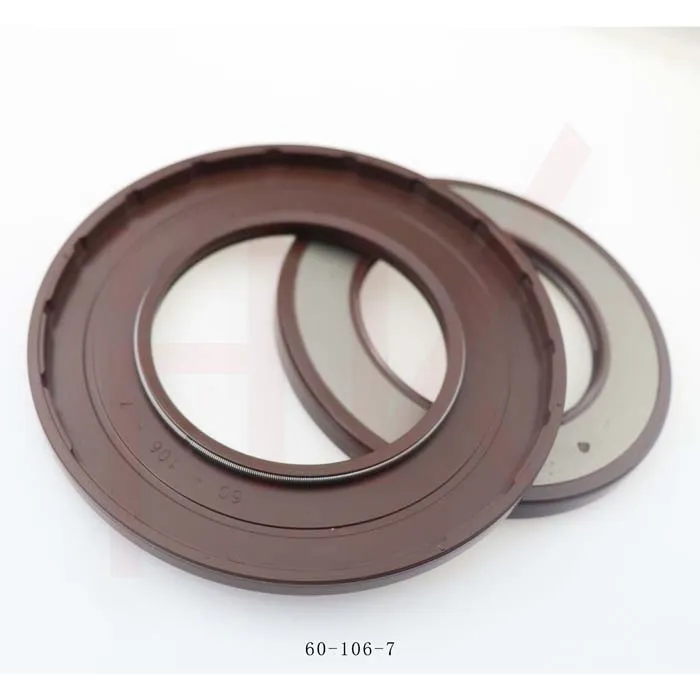
In terms of authoritativeness, double lip seals have become a cornerstone in precision engineering, often endorsed by leading manufacturers across sectors. Their role in preventing leakage and protecting inner engine components is widely documented in engineering journals and manufacturer manuals, establishing them as a reliable solution for enhancing the efficiency and durability of equipment.
double lip seal
Trustworthiness is intrinsically linked to the performance of double lip seals. It is imperative that these seals undergo rigorous testing to meet industry standards such as ISO and ASTM. These seals must demonstrate their resilience under various operational conditions, ensuring that they maintain their integrity and function effectively over prolonged periods. Users must rely on seals that have been verified by authorities in the field for assurance of quality and performance.
Incorporating double lip seals requires careful consideration of installation techniques to maximize their efficacy. Proper alignment and installation are crucial; an improperly installed seal can lead to premature failure, which not only hampers machinery performance but can also lead to costly downtime and repairs. Hence, it is recommended that installation be performed by experienced technicians who understand the nuances of seal placement and the specific needs of the machinery in question.
In conclusion, the double lip seal exemplifies a blend of sophisticated design and robust performance, essential for maintaining the integrity and efficiency of machinery across various sectors. Their capacity to provide superior sealing solutions paves the way for enhanced equipment longevity and reliability. By selecting the right seal for the specific operational environment and ensuring meticulous installation, industries can significantly reduce maintenance costs and optimize machinery performance, thereby driving productivity and ensuring operational excellence.