The double lip oil seal is a crucial component in machinery and automotive industries, offering enhanced sealing capabilities that prevent unwanted fluid leaks. Its unique design features two distinct sealing lips, which provide a dual barrier against contaminants and fluids, making it an essential element in prolonging the life of equipment and ensuring efficient operation.
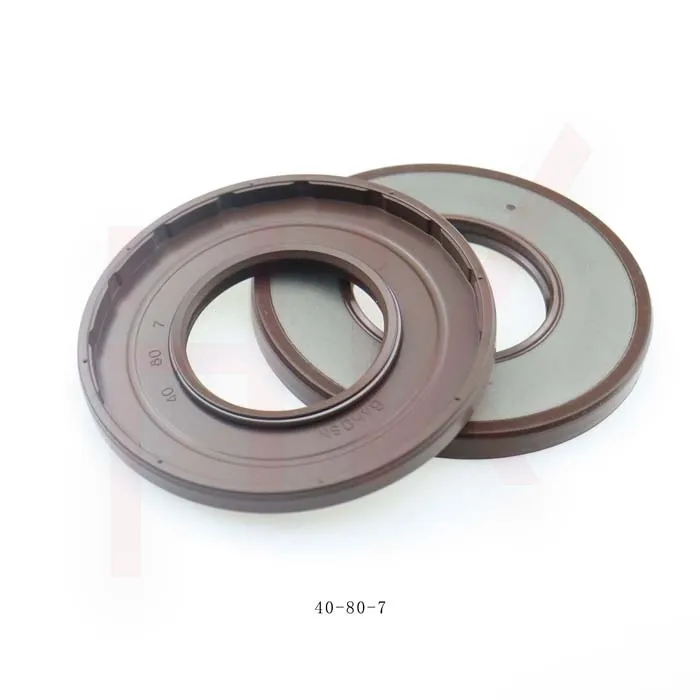
Incorporating double lip oil seals into machinery is not merely about preventing leaks; it is about ensuring that the machinery runs smoothly and efficiently. The dual-lip structure safeguards against dirt, dust, and moisture, which are common culprits in causing premature wear and tear of mechanical components. The primary lip maintains a tight seal against the rotating shaft, while the secondary lip offers additional sealing protection, resulting in a superior seal that extends the longevity of the machine parts.
The expertise behind the design and manufacturing of double lip oil seals involves a deep understanding of materials and engineering. Typically constructed from high-grade elastomers like NBR (Nitrile Butadiene Rubber) or FKM (Fluoroelastomer), these materials are selected for their resilience against various fluids and temperature ranges. The choice of material is determined by the specific operating conditions and the type of fluid that the seal will encounter, showcasing the necessity for expertise in material science and engineering in their development.
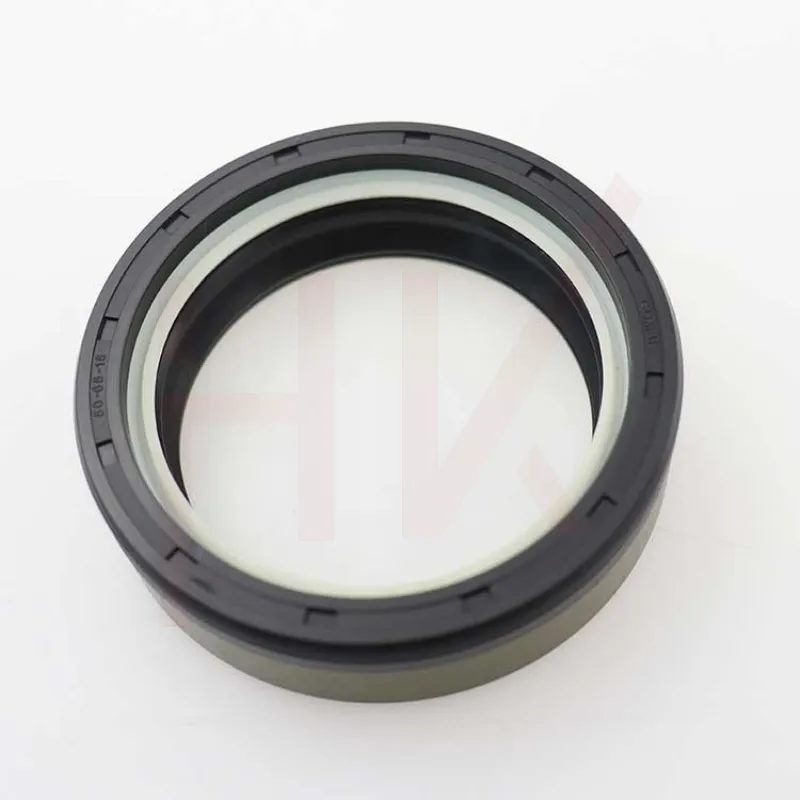
double lip oil seal
From an authoritative perspective, the significance of a double lip oil seal in heavy machinery or automotive applications cannot be overstated. Industry standards and safety regulations often prescribe the use of such seals due to their reliability and ability to function under high pressure and velocity environments. The use of double lip oil seals is a testament to a commitment to maintaining operational safety and efficiency, thereby reinforcing the manufacturer’s authority in producing high-quality, dependable equipment.
Trust in double lip oil seals is built on a foundation of rigorous testing and quality assurance practices. Manufacturers subject these seals to extensive testing, simulating real-world conditions to ensure they meet or exceed performance expectations. The industry's best practices involve lifecycle testing,
pressure resistance evaluation, and thermal testing, which build trust and confidence among end-users. When a product consistently performs as expected and withstands the rigorous demands of its intended environment, it becomes a trusted solution in the field.
In summary, the double lip oil seal is more than just a component; it is a pivotal element that embodies experience, expertise, authority, and trustworthiness. Its design intricacies and the precision in its deployment reflect decades of engineering advancements and a commitment to quality. By understanding and utilizing the full capabilities of double lip oil seals, businesses can significantly enhance the performance and reliability of their equipment, ensuring long-lasting and trouble-free operation across a multitude of applications.