The significance of cylinder oil seals in mechanical applications cannot be overstated. These seals serve as a crucial component in machinery, ensuring optimal performance and longevity. Cylinder oil seals are designed to prevent fluid leakage and protect against the ingress of contaminants, thereby enhancing machine efficiency and safeguarding investment in industrial equipment.
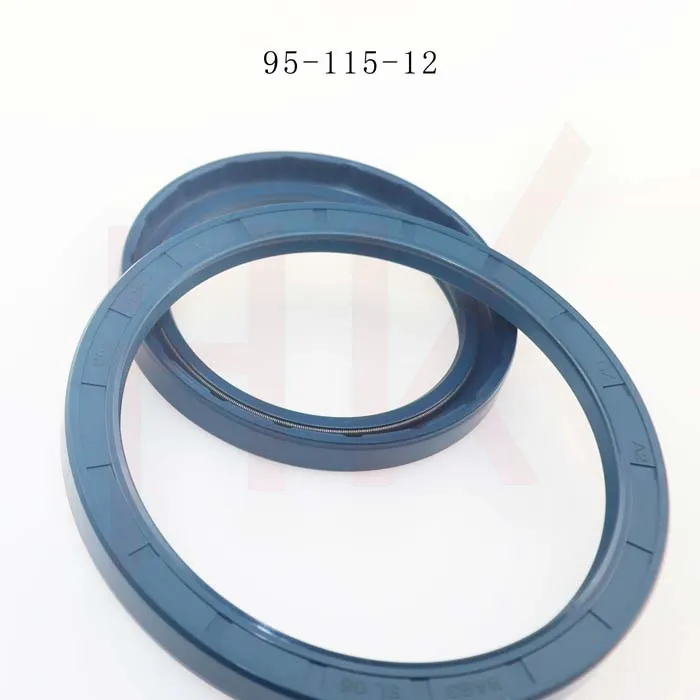
From an experience standpoint, choosing the right cylinder oil seal can dictate the level of performance and maintenance requirements a business might encounter. Experienced maintenance technicians understand that mismatched seals can lead to catastrophic failure, costing organizations significant time and resources. On-the-ground experience has shown that regular inspection and timely replacement of oil seals can drastically reduce downtime in industrial operations, thereby increasing productivity.
Expertise in cylinder oil seal selection and installation is indispensable for engineers and maintenance personnel. Various types of seals are available, such as lip seals, radial seals, and axial seals, each suited for specific applications. Understanding the nuances of these types can empower professionals to make informed choices. Engineered from materials like Nitrile, Viton, or Teflon, these seals offer different levels of heat resistance, chemical compatibility, and durability. Professionals with expertise in seal technology will consider factors such as the working environment, pressure levels, and rotational speeds to select an appropriate seal that minimizes friction and wear, thereby extending the operational life of equipment.
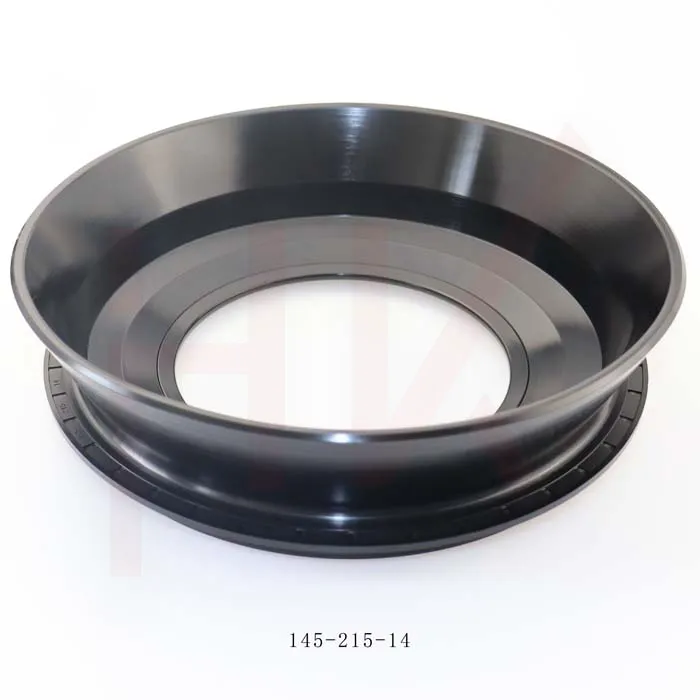
From an authoritativeness perspective, cylinder oil seal manufacturers and suppliers play a pivotal role in establishing standards and guidelines. Certified manufacturers adhere to industry norms set by authoritative bodies such as the International Organization for Standardization (ISO) or the American Society for Testing and Materials (ASTM). These certifications assure users of the product's reliability and robustness. Moreover, engaging with certified distributors ensures that customers receive authoritative advice on the latest technological advancements and best practices in oil seal applications.
cylinder oil seal
Trustworthiness is closely linked to the reputation of oil seal manufacturers and their adherence to quality assurance processes. Trustworthy suppliers invest in rigorous testing protocols to assess the performance of oil seals under simulated stress conditions, providing buyers with confidence in the reliability of their purchases. User testimonials and customer reviews often serve as indicators of a product’s trustworthiness, highlighting the real-world performance and customer satisfaction achieved through these products.
Insights from the field suggest that adopting a proactive maintenance strategy that includes regular oil seal checks can prevent unexpected failures. Industries such as automotive, aerospace, and manufacturing emphasize routine seal replacement schedules to maintain optimal machinery performance. In the automotive industry, for instance, strategic placement of cylinder oil seals within engines ensures lubrication retention, minimizing wear and enhancing fuel efficiency.
In conclusion, cylinder oil seals are pivotal in maintaining the efficacy and reliability of mechanical systems across various industries. By leveraging experience, expertise, authority, and trust, stakeholders can make informed decisions regarding the selection and maintenance of these essential components. Investing in high-quality oil seals not only ensures prolonged machinery life but also supports sustainable operational practices, enhancing overall business performance. Recognizing the critical role that cylinder oil seals play can lead to smarter, cost-effective maintenance strategies and improved system reliability.