The Art and Science of Custom-Made Oil Seals
In the intricate world of mechanical engineering, where precision meets functionality, custom-made oil seals stand as both a testament to human innovation and a crucial component in ensuring the smooth operation of machinery. These bespoke seals are not merely afterthoughts in design; they are carefully crafted solutions that prevent lubricants from escaping while keeping contaminants at bay.
The process of designing and manufacturing custom oil seals is a blend of art and science. It begins with an understanding of the machine's unique needs—be it speed, temperature, pressure, or chemical resistance. Engineers must also consider the physical dimensions of the seal's environment, ensuring an exact fit within often hair-thin tolerances. This meticulous approach guarantees that each seal performs flawlessly under the specific conditions it was designed for.
Material selection is another critical aspect. Elastomers such as Buna-N or silicone might be chosen for their flexibility and resistance to oil degradation, while polytetrafluoroethylene (PTFE) could be used for its low friction properties. The material must not only withstand the vagaries of the operating environment but also preserve its integrity over extended periods.
Once the design is finalized, the manufacturing phase takes over. Advanced technologies like computer-aided design (CAD) and computer-aided manufacturing (CAM) play pivotal roles here, enabling precise cuts and shapes that would be unachievable by hand Advanced technologies like computer-aided design (CAD) and computer-aided manufacturing (CAM) play pivotal roles here, enabling precise cuts and shapes that would be unachievable by hand
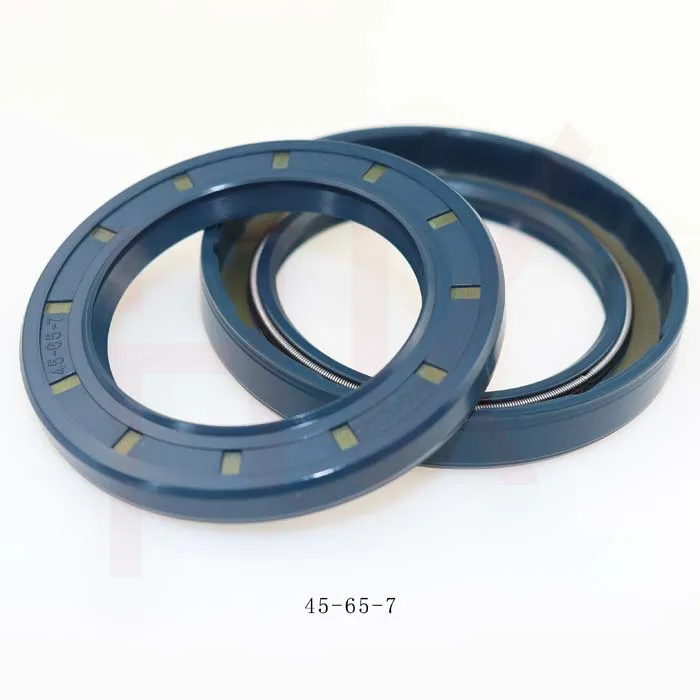
Advanced technologies like computer-aided design (CAD) and computer-aided manufacturing (CAM) play pivotal roles here, enabling precise cuts and shapes that would be unachievable by hand Advanced technologies like computer-aided design (CAD) and computer-aided manufacturing (CAM) play pivotal roles here, enabling precise cuts and shapes that would be unachievable by hand
custom made oil seals. Stringent quality control measures then ensure that each seal meets the high standards set forth in its design.
The benefits of custom-made oil seals are multifaceted. They offer a level of performance tailor-made to the machine's specifications, reducing leaks and prolonging equipment lifespan. In turn, this reduces maintenance costs and downtime, providing a solid return on investment. Moreover, these seals contribute to sustainability efforts by curtailing oil waste and preventing potential environmental damage.
In conclusion, custom-made oil seals represent a confluence of engineering expertise and material science. They are not just protective barriers but optimized components that enhance machine efficiency and longevity. By embracing custom designs, industries can move towards more reliable operations, financial savings, and environmental stewardship—a trifecta that defines modern mechanical excellence.