The Importance of Hydraulic Seal Replacement A Comprehensive Guide
Hydraulic systems are the backbone of numerous industrial and engineering applications, from heavy machinery to aerospace technology. A critical component in these systems is the hydraulic seal, which ensures efficient operation and prevents fluid leakage. Over time, seals can wear out or become damaged, necessitating replacement. This article delves into the significance of hydraulic seal replacement and the process involved.
Hydraulic seals are designed to maintain system integrity by sealing the interface between moving components and stationary parts. They prevent fluid loss, minimize contamination, and enhance overall system performance. However, factors such as pressure fluctuations, temperature changes, and mechanical stress can cause seals to degrade, leading to leaks, reduced efficiency, and potential equipment failure. It's crucial to recognize the signs of seal wear, such as fluid leakage, unusual noises, or decreased performance, as they indicate the need for a replacement.
The process of hydraulic seal replacement requires precision and expertise. Firstly, the system must be depressurized and drained to ensure safety during the operation. Once the affected component is accessible, the old seal is carefully removed without damaging the housing or adjacent parts. It's essential to clean the sealing surfaces thoroughly to remove any debris that could compromise the new seal's effectiveness.
Choosing the right replacement seal is paramount. Seals come in various types, including O-rings, lip seals, rod seals, and piston seals, each designed for specific applications and operating conditions Seals come in various types, including O-rings, lip seals, rod seals, and piston seals, each designed for specific applications and operating conditions
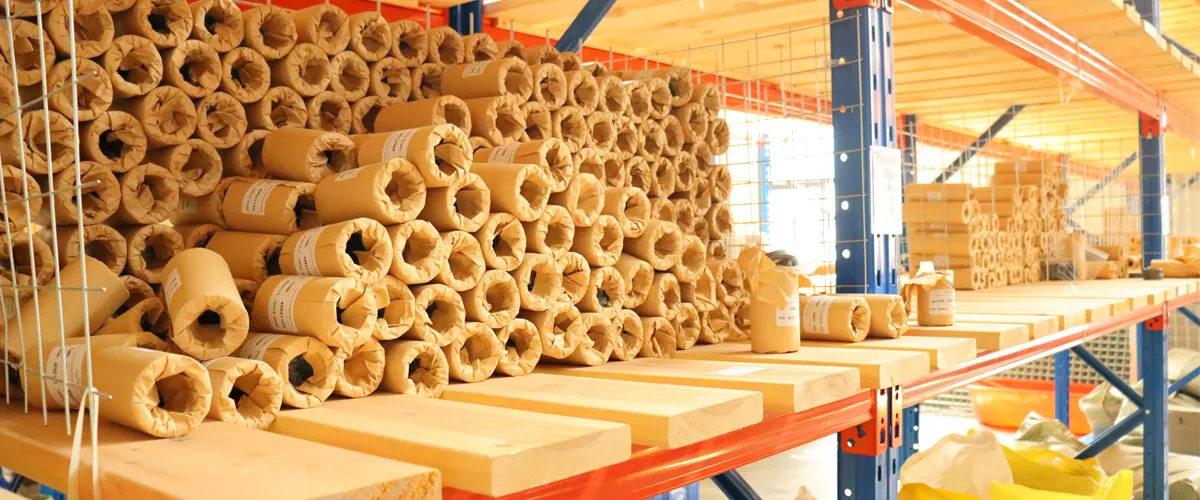
Seals come in various types, including O-rings, lip seals, rod seals, and piston seals, each designed for specific applications and operating conditions Seals come in various types, including O-rings, lip seals, rod seals, and piston seals, each designed for specific applications and operating conditions
hydraulic seal replacement. Compatibility with the fluid, temperature range, and pressure levels should be considered when selecting a new seal. Consulting manufacturer guidelines or seeking professional advice can help ensure the correct choice.
Installation of the new seal is another critical step. Incorrect installation can lead to premature failure or ineffective sealing. Following proper installation techniques, such as using lubricants to ease insertion, avoiding over-stretching, and ensuring proper alignment, is crucial. After installation, it's advisable to perform a leak test before returning the system to operation.
Regular maintenance and timely hydraulic seal replacement not only prolong the life of the equipment but also reduce downtime and maintenance costs. Neglecting seal issues can lead to more severe problems like component damage, increased energy consumption, and even complete system failure. Therefore, proactive seal management should be an integral part of any hydraulic system's maintenance routine.
In conclusion, hydraulic seal replacement is a vital aspect of maintaining the functionality and reliability of hydraulic systems. Understanding the signs of seal wear, choosing the appropriate replacement, and executing the replacement process correctly can significantly contribute to the overall efficiency and longevity of the equipment. As with all aspects of machinery maintenance, prevention is often more cost-effective than cure, making hydraulic seal replacement a strategic investment in the health of your hydraulic system.