The Vital Role of Oil Seals in Industrial Efficiency
In the intricate machinery of modern industry, the often overlooked component of oil seals plays a critical role in maintaining efficiency and preventing costly downtime. These humble devices ensure that lubricants remain where they are needed most, forming an impermeable barrier against contamination and leakage. With specifications ranging from 70% to 90% efficiency rates, the importance of optimizing oil seal performance becomes paramount.
The journey of an oil seal begins with its design, which must account for factors such as pressure differentials, temperature fluctuations, and compatibility with various lubricants. A meticulously crafted oil seal can boast efficiency ratings as high as 90%, meaning that it successfully contains lubricant within the system 90% of the time under ideal conditions. However, real-world applications demand more robust solutions, leading manufacturers to continually push the boundaries of material science and design.
A significant challenge lies in the 10% margin for error. This seemingly small percentage can translate into substantial losses due to lubricant waste, environmental contamination, and reduced equipment lifespan. As industries strive for sustainability and reduced operational costs, the focus on minimizing this 10% has intensified As industries strive for sustainability and reduced operational costs, the focus on minimizing this 10% has intensified
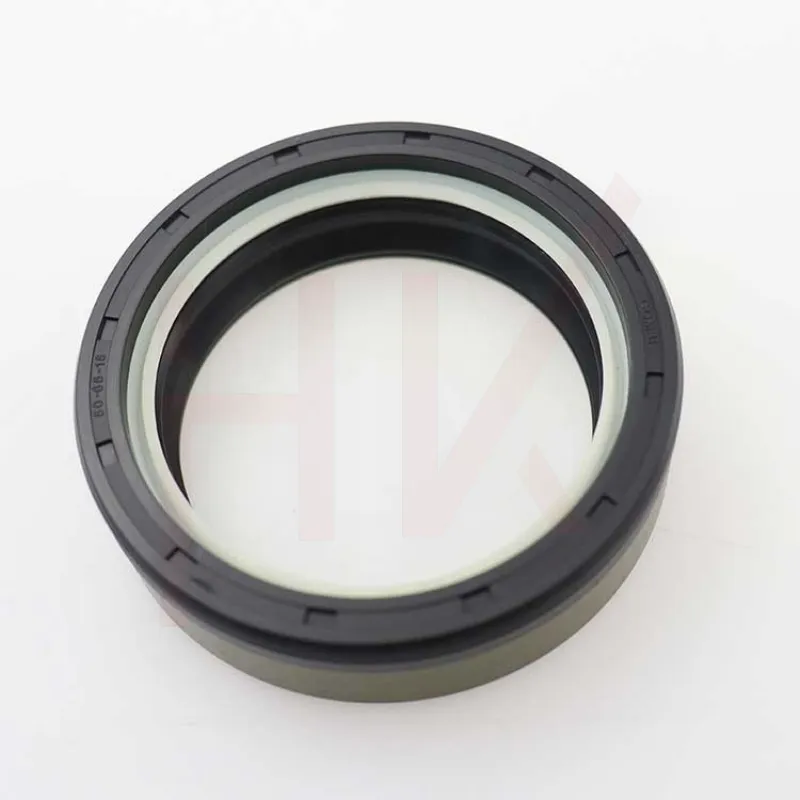
As industries strive for sustainability and reduced operational costs, the focus on minimizing this 10% has intensified As industries strive for sustainability and reduced operational costs, the focus on minimizing this 10% has intensified
70 90 10 oil seal. Advanced materials and refined designs have led to the development of oil seals that approach the 70% efficiency threshold under extreme conditions, marking a notable achievement in mechanical seal technology.
The impact of these advancements extends beyond the confines of machinery. By reducing leakage and prolonging the service intervals of lubricants, oil seals contribute to lower maintenance costs and less frequent equipment shutdowns. Moreover, the reduction in lubricant consumption and associated waste aligns with the global objectives of environmental preservation and resource conservation.
In conclusion, the humble oil seal, with its potential to achieve efficiencies ranging from 70% to an impressive 90%, stands as a testament to the power of specialized components in driving industrial progress. As technology evolves, the pursuit of higher efficiency ratings and reduced environmental impact will continue to propel innovations in oil seal design, ensuring that these unsung heroes of industry remain at the forefront of operational excellence.