Understanding the technicalities and the importance of oil seals is crucial for maintaining the efficiency and longevity of machinery and automotive components. The 35x52x7 oil seal represents a specific size that is vital across various machinery applications. Let's explore the distinctive characteristics, applications, and the industry's best practices to ensure the optimal use of these seals.
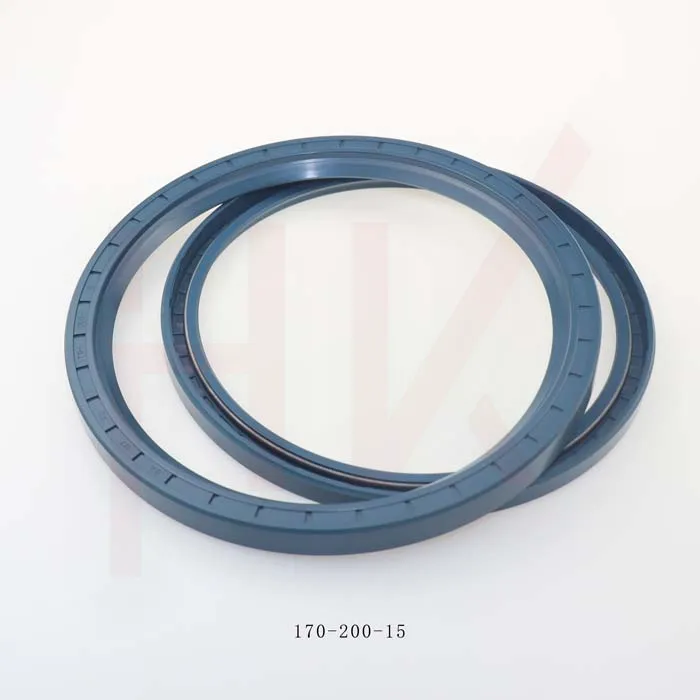
Oil seals, often referred to as rotary shaft seals or just shaft seals, are indispensable in preventing contaminants like dirt, dust, and moisture from entering the machinery while also retaining the lubricants inside. The integrity of an oil seal directly influences the performance and lifespan of mechanical assemblies.
The dimensions 35x52x7 denote a seal with a 35mm inner diameter, a 52mm outer diameter, and a 7mm thickness. Such precise specifications are essential for fitting the seal correctly between components, ensuring no leakages and robust protection against external contaminants. The choice of these dimensions can significantly impact the functionality of the machinery, given that an improper fit could lead to oil leaks and component damage.
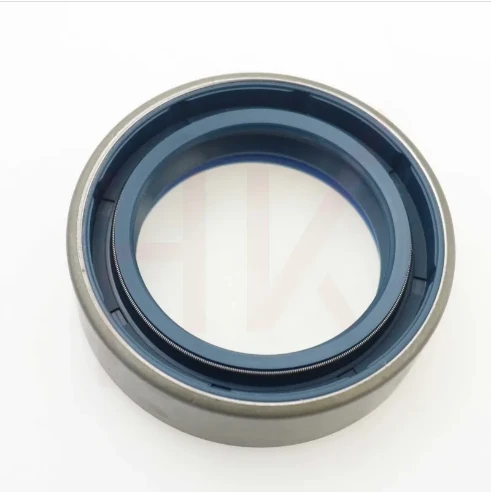
When discussing the construction of oil seals, materials play a critical role in their durability and effectiveness. The 35x52x7 oil seal is often manufactured from high-quality nitrile rubber (NBR), which is known for its excellent resistance to oil and other petroleum products. NBR is also resistant to wear and tear, making it a preferred choice for seals that are likely to endure constant exposure to lubricants and environmental challenges. Alternative materials like silicone or fluorocarbon rubber (FKM) are used for more specialized applications where extreme temperatures or chemical exposure are factors.
35x52x7 oil seal
Implementing the correct oil seal requires expert knowledge of the machinery. A mechanical engineer or a professional with technical expertise should assess the operational environment, including the temperature range, pressure conditions, and speed at which the seal will function. Ensuring that these factors align with the seal's capabilities is paramount for maintaining equipment reliability.
From the perspective of maintenance and reliability engineering, regular inspections of oil seals can drastically reduce downtime caused by unexpected failures. An oil seal may show signs of wear over time, such as flattening, hardening, or cracking, which can compromise its sealing capability. Keeping a schedule for checking and replacing oil seals as part of routine maintenance is crucial for avoiding costly repairs and prolonging the service life of machinery.
The applications for the 35x52x7 oil seal are vast, spanning industries like automotive, aerospace, and industrial machinery. In the automotive sector, these seals are commonly found in engines, gearboxes, and axles. In industrial machinery, they are critical for hydraulic cylinders, pumps, and compressors. Each application demands specific characteristics from the seal, thus requiring thorough assessment during the planning and installation phases.
In conclusion, the 35x52x7 oil seal is not just a simple mechanical component but a critical element that ensures the seamless operation of complex machinery. Utilizing expertise in selecting, installing, and maintaining these seals builds trust in their performance, increases machine efficiency, and significantly reduces the risk of mechanical failures. Acknowledging the importance of oil seals in the broader context of mechanical design and maintenance allows for the successful application of these seemingly simple yet highly significant components in modern engineering.