Understanding the intricacies of industrial equipment can be a daunting task, especially when it comes to choosing the right components for maintaining efficacy and longevity. One small yet crucial component that often requires attention is the oil seal, particularly the 35x47x7 oil seal. This indispensable element ensures the smooth and safe operation of machinery, playing a pivotal role in preventing leaks and contamination while maintaining the integrity of the lubricants.
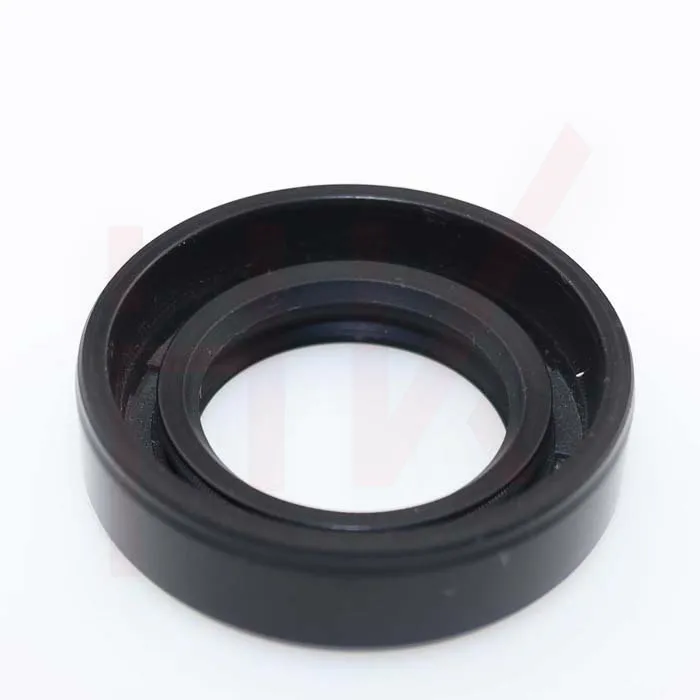
An oil seal, also commonly known as a radial lip seal, is integral in maintaining the effectiveness and life span of industrial machinery. The specific dimensions of the 35x47x7 oil seal imply a critical fit for machinery requiring high precision. Understanding these specifications - with a 35mm interior diameter, a 47mm exterior diameter, and a 7mm width - is essential for ensuring a proper fit and function in your machinery.
The true value of the 35x47x7 oil seal lies in its ability to contain lubricants and block contaminants. In mechanically demanding environments, the correct application of oil seals prevents the ingress of dirt, dust, and moisture, which can drastically shorten the lifespan of internal components. In addition, by retaining oil or grease, it eliminates the risk of wear due to insufficient lubrication, thereby ensuring seamless operational efficiency.
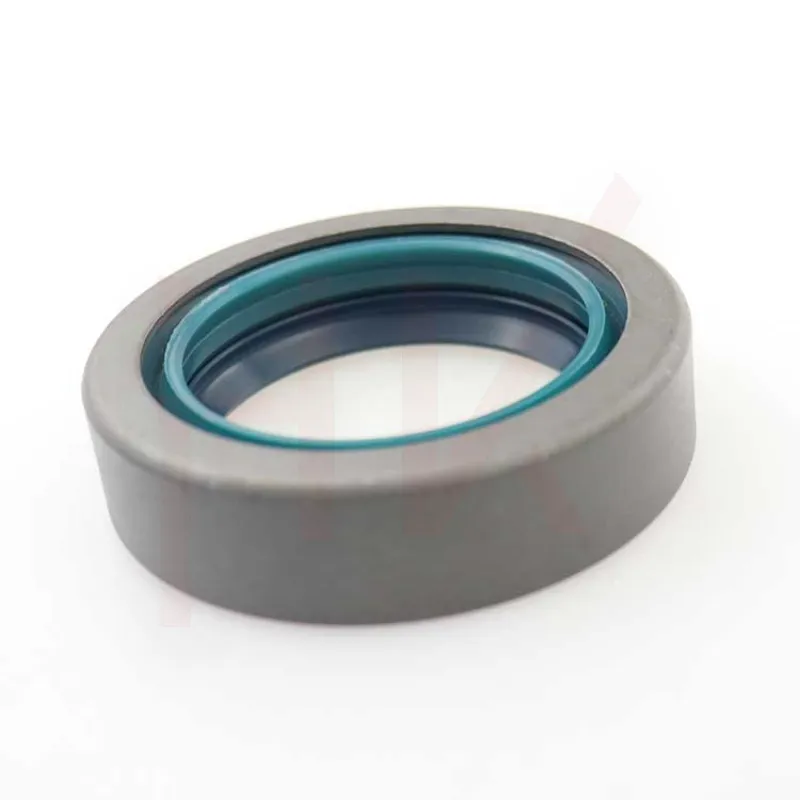
From an expertise perspective,
selecting the right material for the oil seal is paramount. Nitrile rubber (NBR) is an economical choice, suitable for most general applications involving oils and greases. It works efficiently at temperatures ranging from -30°C to +100°C, making it a versatile option for various industrial needs. However, for situations that demand resistance to higher temperatures or specific chemicals, selecting a seal made from fluorocarbon rubber (FKM) might be preferable. FKM seals can withstand temperatures between -26°C to +204°C, providing excellent heat resistance for more demanding applications.
Ensuring that your oil seal is made from the appropriate material enhances its performance, offering reliability under diverse conditions. It's crucial for end-users to consult with professionals when selecting an oil seal material, especially if the machinery operates under unique or extreme conditions.
35x47x7 oil seal
From a real-world experience standpoint, routine inspection and maintenance of oil seals should not be overlooked. Over time, oil seals can suffer from degradation due to material fatigue, contamination, or improper installation. Regular monitoring can prevent unscheduled downtimes by identifying wear and tear early, allowing for timely replacements. Ensuring that the seal housing remains free from burrs and scratches during installation can prevent premature seal failure. Comprehensive inspection during routine maintenance checks serves to confirm that all seals are intact and functioning optimally.
Authoritativeness is demonstrated by the choice of suppliers and manufacturers. Renowned brands consistently deliver high-quality products engineered to meet the rigorous standards of industrial applications. Suppliers with ISO certifications and adherence to industry standards offer a level of assurance regarding the quality of their oil seals. Selecting products from trusted manufacturers can mitigate risks, assuring that your machinery operates at peak performance with minimal disruptions.
Finally, trustworthiness involves looking at customer reviews and testimonials. Users often discuss their experiences with specific oils seals, providing valuable insights into performance and durability that aren't always apparent from specifications alone. Consider seeking advice from peers or professionals who have extensive experience with the 35x47x7 oil seal in similar applications.
Incorporating this nuanced understanding of oil seal technology into your purchasing and maintenance strategies can extend the life of your machinery, ensuring robust performance and reliability. A focused approach, informed by experience, expertise, authoritative sources, and trustworthiness, will undoubtedly lead to better decision-making and operational success.