When it comes to the vital components that ensure the seamless functioning of machinery, the term 35 52 7 oil seal undoubtedly stands out. These small yet crucial elements are indispensable in a wide array of applications ranging from automotive engineering to heavy industry, providing an essential barrier that prevents the leakage of lubricants. Understanding the significance of these oil seals not only highlights their technical importance but also showcases the expertise that goes into designing such components.
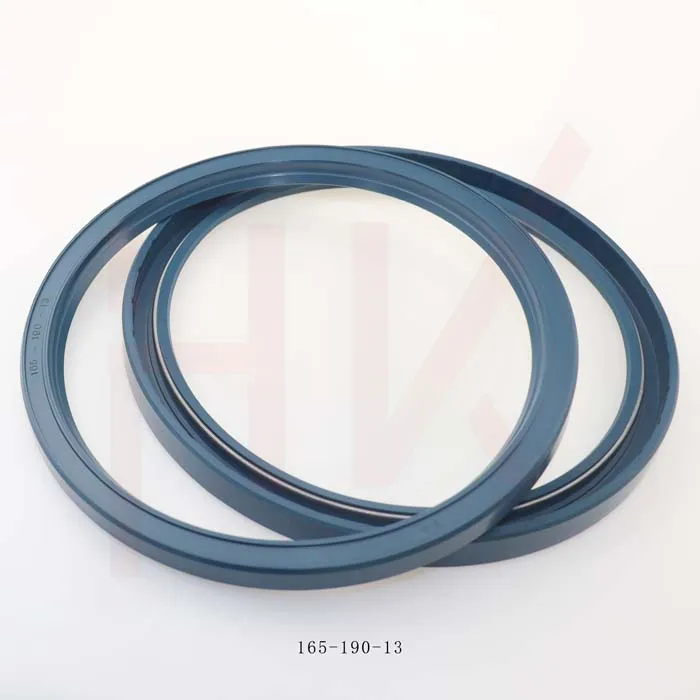
The world of oil seals is intricate, defined by specific dimensions that cater to particular needs. The numbers in 35 52 7 refer to critical measurements the inner diameter of 35 mm, an outer diameter of 52 mm, and a width of 7 mm. This precision ensures compatibility with a multitude of applications, where exact sizing determines the efficiency and longevity of the seal. Such specifications are the result of extensive research and understanding of engineering needs, showcasing the expertise of the manufacturers who produce these seals to exacting standards.
In the realm of product performance,
oil seals play a pivotal role. Their primary function is to keep oil, which is essential for lubrication, within a specific area of the machinery. This helps in reducing friction between moving parts, thereby enhancing the lifespan of the equipment. Furthermore, these seals prevent contaminants from entering, maintaining the integrity and performance of the machinery. Achieving this dual function necessitates a robust design, typically employing advanced materials like nitrile rubber or polyurethane, known for their resistance to oil, temperature fluctuations, and wear and tear.
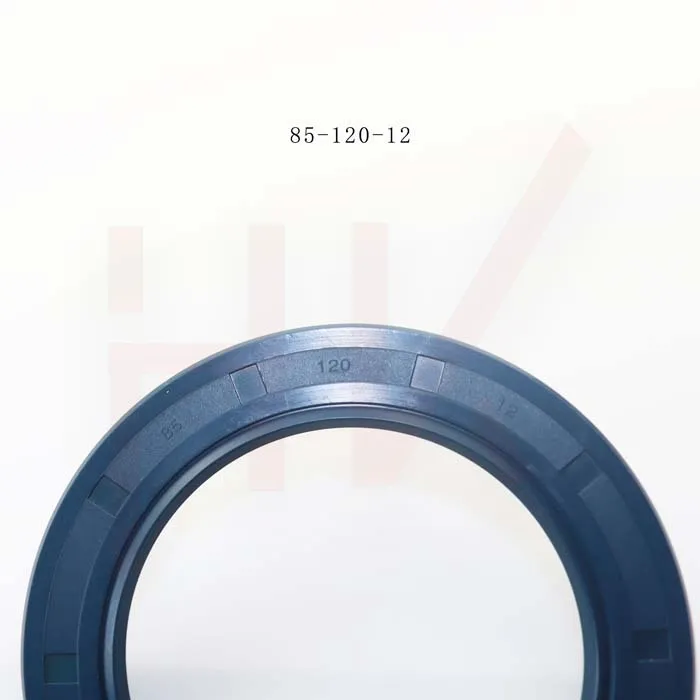
The authority of oil seal manufacturers is reflected in their meticulous production processes. Top-tier companies invest heavily in research and development to innovate sealing technology. This includes the use of computer-aided design (CAD) to model seals that can withstand extreme conditions and rigorous testing to ensure compliance with international standards. The result is a product that not only meets but often exceeds industry expectations, establishing a reputation for reliability and excellence.
35 52 7 oil seal
Trustworthiness in this arena is rooted in a consistent track record of quality and customer satisfaction. Consumers and businesses alike depend on these oil seals to operate within critical applications, making reliability non-negotiable. Reputable manufacturers support their products with comprehensive warranties and are transparent about the materials and processes used in production. Moreover, expert customer support teams are available to provide guidance, ensuring that users select the right seal for their specific requirements, thereby reducing the risk of operational downtime.
The breadth of experience within the oil seal industry cannot be overstated. With decades, if not centuries, of combined experience among leading companies, there is an unparalleled depth of knowledge that informs every aspect of production, from material selection to the most efficient manufacturing techniques. This expertise is not static, however. Manufacturers continually invest in training and technology to remain at the forefront of the industry, adapting to new challenges and innovations with skill and foresight.
In conclusion, the 35 52 7 oil seal is more than just a component; it is a testament to engineering precision, expertise, and innovation. Within its simple numerical designation lies a world of complex design considerations and manufacturing excellence. Whether used in the automotive sector or industrial applications, the integrity of these seals is paramount to machine performance and efficiency. By understanding their importance and the rigorous standards they are held to, we can appreciate the blend of science and skill that ensures these small yet mighty components perform their crucial roles with reliability and trust.