The Significance of 25%, 35%, and 7% in Oil Seal Technology
In the realm of engineering and mechanics, oil seals play a critical role in ensuring the efficient functioning of machinery. They prevent lubricants from leaking out while simultaneously keeping contaminants at bay. A key aspect that significantly impacts their performance is the composition of their materials, particularly the percentage ratios of different components. Among these, the percentages 25%, 35%, and 7% hold particular importance, referring to the proportion of rubber, reinforcement, and oil in an oil seal.
The rubber component, typically constituting around 25% of the oil seal, serves as the primary barrier against fluid leakage. It is the elastomeric material that provides the seal's flexibility and resilience. Rubber, with its inherent ability to stretch and return to its original shape, ensures a tight fit around rotating or static shafts, thereby preventing oil from escaping.
The reinforcement layer, usually accounting for 35% of the seal, is embedded within the rubber. This layer, often made of materials like fabric or steel, enhances the seal's strength and durability. It helps withstand high pressures and temperatures, preventing deformation or damage under extreme conditions. It also provides additional support to the rubber, maintaining its structural integrity over time It also provides additional support to the rubber, maintaining its structural integrity over time
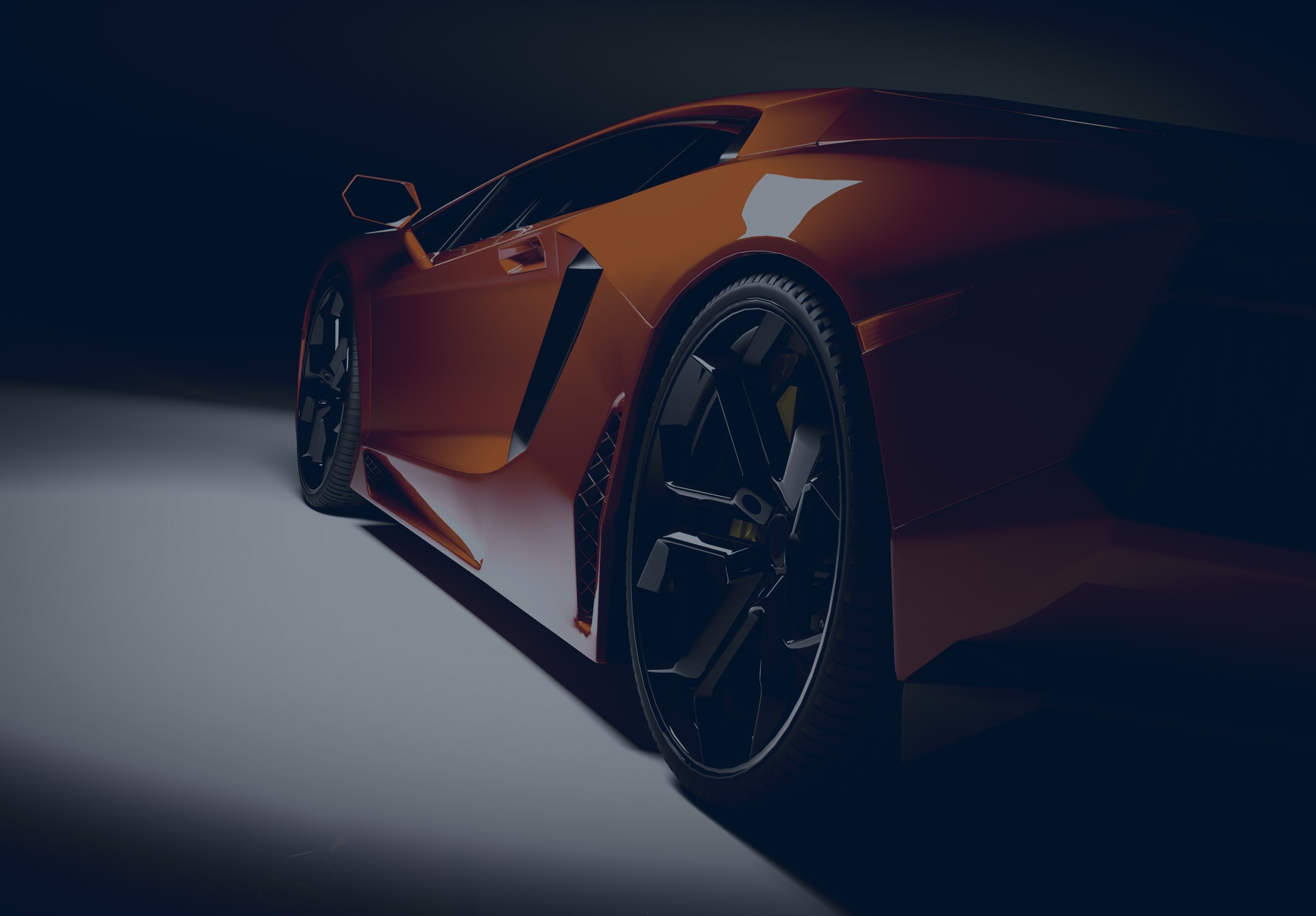
It also provides additional support to the rubber, maintaining its structural integrity over time It also provides additional support to the rubber, maintaining its structural integrity over time
25 35 7 oil seal.
Lastly, the oil content, making up about 7% of the oil seal, acts as a lubricant and a protective agent. It not only ensures smooth operation by reducing friction between the seal and the shaft but also prevents the rubber from drying out, extending the seal's lifespan. The specific type of oil used can vary depending on the operating environment and the properties required for optimal performance.
Understanding the significance of these percentages is crucial for engineers and technicians when selecting the right oil seal for a specific application. Each percentage contributes uniquely to the overall performance, sealing effectiveness, and longevity of the oil seal. Therefore, a precise balance between these components is vital to ensure the seal can endure various mechanical stresses, temperature fluctuations, and chemical exposures.
In conclusion, the percentages 25%, 35%, and 7% are more than just numbers in oil seal technology; they represent a delicate balance of functionality, durability, and efficiency. By meticulously controlling these proportions, manufacturers can tailor oil seals to meet the diverse demands of industries ranging from automotive to aerospace, ensuring reliable and safe operation of machinery.