When it comes to ensuring the longevity and optimal performance of machinery, the importance of reliable sealing solutions cannot be overstated. The 22 40 7 oil seal is a key component in the world of mechanical engineering, serving as a critical barrier to protect essential components from contaminants and leakage. This article delves into the nuances of oil seals, focusing on this specific dimension, and explores why this seal is integral to machinery operation and maintenance.
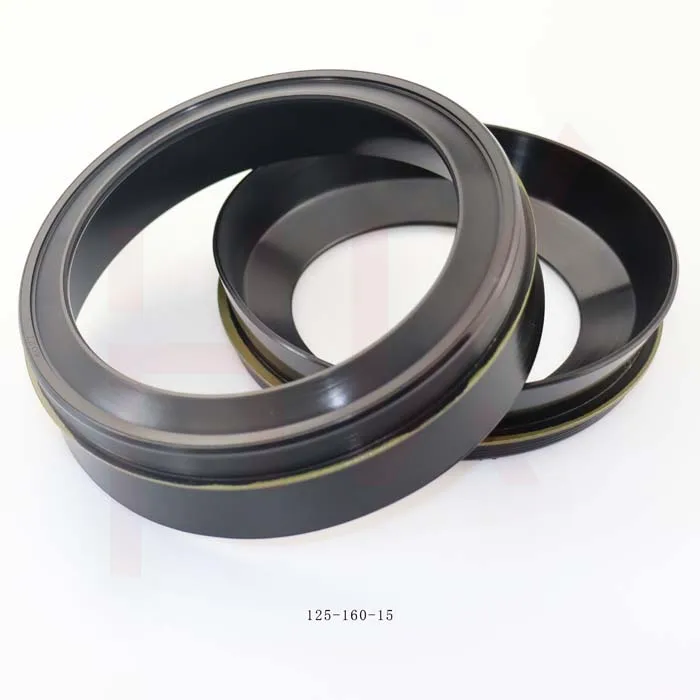
Understanding Oil Seals Oil seals, often referred to as rotary shaft seals, are designed to close the spaces between stationary and moving components in mechanical equipment. They prevent lubricants from leaking out and contaminants such as dirt, dust, and water from seeping in. This dual-purpose functionality not only enhances the operational lifespan of machinery but also ensures efficiency and prevents costly downtimes.
The 22 40 7 Dimension Explained The numbers 22 40 7 in our key phrase are not just random figures. In the context of oil seals, these numbers provide crucial information about the seal's dimensions. The first number, 22, represents the inner diameter (ID) in millimeters, which corresponds to the shaft diameter the seal will envelop. The second number, 40, refers to the outer diameter (OD), indicating the size of the housing bore in which the seal will be installed. Lastly,
the number 7 signifies the thickness or width of the seal. These measurements are essential in ensuring the proper fit and function of the seal within a device.
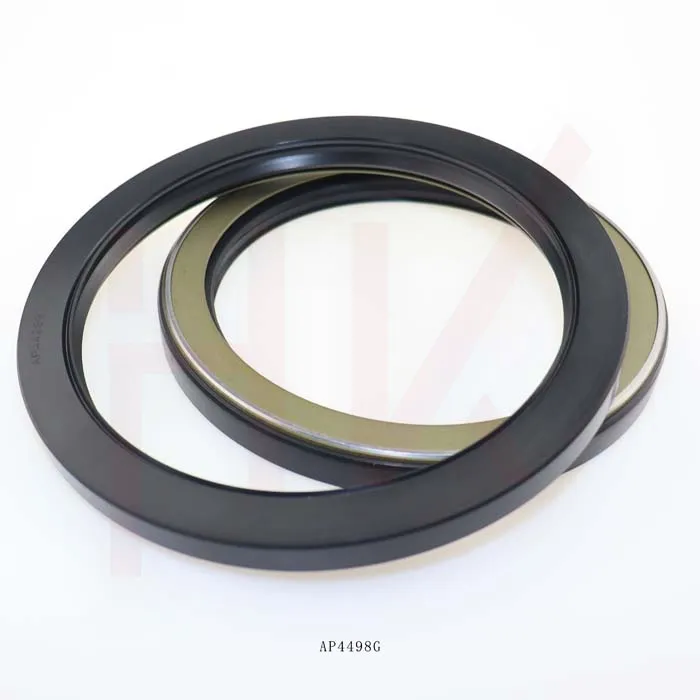
Application Areas The versatility of the 22 40 7 oil seal makes it suitable for a multitude of applications. It is commonly used in automotive, agriculture, and industrial machinery. For instance, in automotive engines, this seal can be found in crankshafts and camshafts, ensuring the oil remains within the engine’s lubrication system while keeping out harmful contaminants. This is crucial for maintaining engine performance and extending the engine's lifespan. In agricultural machinery, such as tractors, these seals protect against the ingress of dirt and moisture during fieldwork, playing a vital role in safeguarding the machinery's complex components.
Materials and Durability The material composition of oil seals is a critical factor in their performance. The 22 40 7 oil seal is typically manufactured using materials such as nitrile rubber (NBR), silicone, or fluoroelastomer (FKM), each chosen based on the application environment. Nitrile rubber is renowned for its excellent resistance to oil, its affordability, and its durability in temperatures ranging from -40°C to 120°C. Silicone seals offer significant temperature range advantages, making them ideal for automotive applications with temperature extremes. Meanwhile, FKM provides exceptional resistance to heat, chemicals, and oils, and is used in more demanding scenarios.
22 40 7 oil seal
Installation and Best Practices Correct installation of the 22 40 7 oil seal is imperative for its effectiveness. Professionals recommend inspecting the shaft and bore surfaces for burrs or damage before installation. Using the appropriate tools for installation prevents deformation of the seal, which can otherwise lead to premature failure. Practicing proper lubrication and handling techniques during installation further ensures the seal functions as intended.
Maintenance and Replacement Regular inspection of oil seals is advisable, especially in high-performance or mission-critical machinery. Key signs that a seal may require replacement include visible oil leaks, unusual machinery noise, and vibration. Adopting a proactive maintenance approach by periodically checking seals can prevent unexpected equipment failure and extend overall machinery life.
The Role of Innovation in Oil Seal Technology The field of sealing technology constantly evolves with advancements in materials science and engineering. Modern oil seals, including the 22 40 7 variants, are designed to offer enhanced performance, lower frictional losses, and extended service intervals. Improving seal design and utilizing cutting-edge materials contributes significantly to energy efficiency and machine reliability.
In summary, the 22 40 7 oil seal stands out as an indispensable element in the arena of mechanical systems. Its role in preventing leakage, keeping contaminants at bay, and enhancing system longevity cannot be undermined. Whether in automotive, agricultural, or industrial applications, understanding its dimensions, material properties, and best installation practices is vital for engineers, technicians, and maintenance professionals alike. As technology advances, so too will the capabilities of oil seals, ensuring that they remain a pivotal component in mechanical systems across various industries.