The 17x40x7 seal is a critical component in various industrial applications where precise sealing and reliability are paramount. Understanding its attributes and applications can significantly impact its effectiveness in reducing downtime and enhancing operational efficiency. Drawing on years of expertise and sector experience, this article breaks down the essential elements of the seal, providing a comprehensive overview that fosters trust in its capabilities.
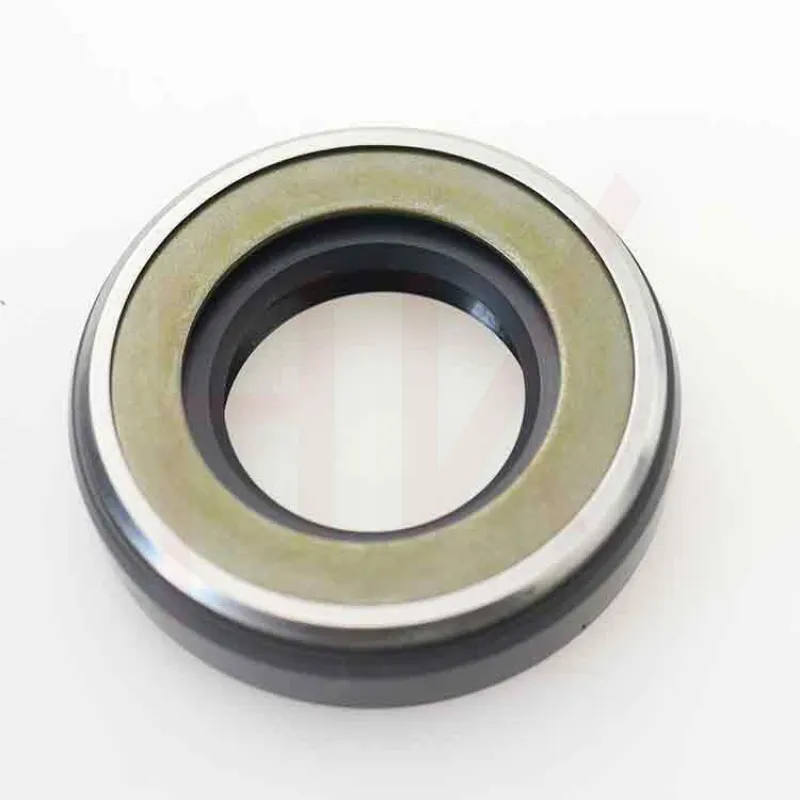
The 17x40x7 seal is precisely designed for use in environments that demand the highest standards of durability and performance. Its dimensions, 17mm inner diameter, 40mm outer diameter, and 7mm width, make it an ideal fit for specific machinery components, ensuring that it provides a tight and secure fit. This precision size is critical in applications to prevent leakage of lubricants and ingress of contaminants, which can cause premature wear or failure of components.
Experts in mechanical systems will acknowledge that the material composition of seals is crucial. The 17x40x7 seal is typically composed of high-grade rubber or synthetic compounds, which offer excellent resistance to heat, oil, and other chemicals. This ensures longevity even in challenging environments, such as those encountered in automotive or heavy machinery industries. Furthermore, the flexibility and resilience of these materials help accommodate slight misalignments without compromising the sealing effectiveness, an essential feature for maintaining operational continuity.
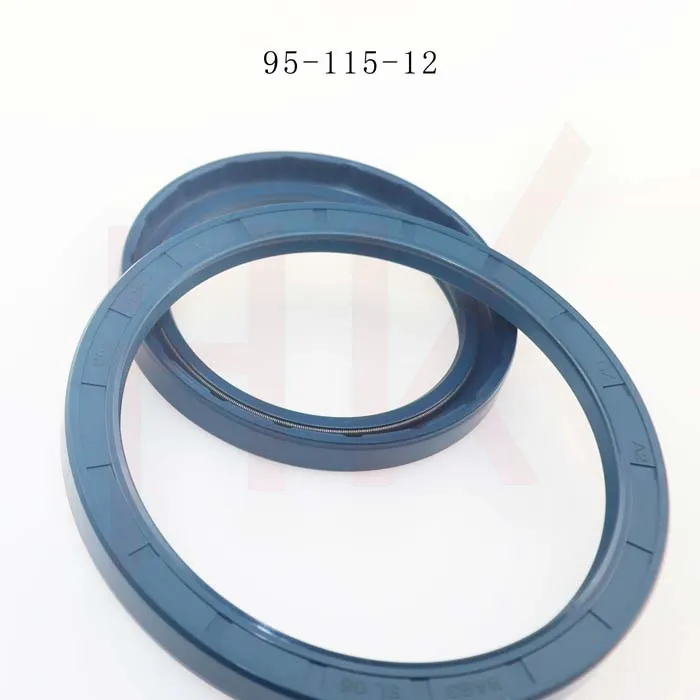
The authoritative performance of the 17x40x7 seal is not only a result of its material properties but also its engineering design. The lip design of the seal plays a pivotal role in maintaining zero-leakage performance. An effective seal lip can minimize friction and wear, which are critical factors for applications involving rotating shafts. The design also aids in reducing energy loss by ensuring that the mechanical movement within the system remains as efficient as possible.
17x40x7 seal
Trust in the 17x40x7 seal is further enhanced by rigorous testing and quality control measures that manufacturers adhere to. Each seal produced is typically subjected to a series of stress tests to guarantee its reliability and robustness under specified conditions. This commitment to quality provides users with the assurance that the seal will perform as expected, minimizing the risk of unexpected failures that could lead to costly repairs or operational downtime.
For those incorporating the 17x40x7 seal into their systems, experience has shown that proper installation and maintenance are key. Ensuring that the seal is fitted correctly, using recommended tools and techniques, can significantly extend its service life. Additionally, regular inspection and maintenance routines can help detect early signs of wear or potential failure, allowing for proactive measures to be taken, thus safeguarding the integrity and efficiency of the machinery.
In summary, the 17x40x7 seal exemplifies the intersection of expert engineering and practical application. Its precise dimensions, coupled with advanced materials and design, make it a trusted choice in demanding industrial settings. Professionals relying on this component can expect enhanced operational reliability, contributing to improved productivity and reduced maintenance costs. By integrating the seal with best practices in installation and upkeep, operators can fully leverage its benefits, thereby achieving greater efficiency and longevity in their machinery operations.