Unlocking the Potential of High Pressure Shafts in Modern Engineering

In the bustling world of modern engineering, the term high pressure shaft reverberates through the corridors of jet propulsion labs, power plants, and advanced manufacturing facilities. This component, though often unnoticed, plays an indispensable role in the realm of high-stakes applications where reliability, efficiency, and durability are non-negotiable.
The high pressure shaft, a meticulously crafted element of engineering savvy, is integral to the function of turbines, compressors, and other high-demand machinery. It is this shaft's job to transmit power from the turbine to the load, all while withstanding incredible amounts of pressure and rotational forces. Its function resembles the vital arteries that carry lifeblood to essential organs; without them, the entire system would fail.
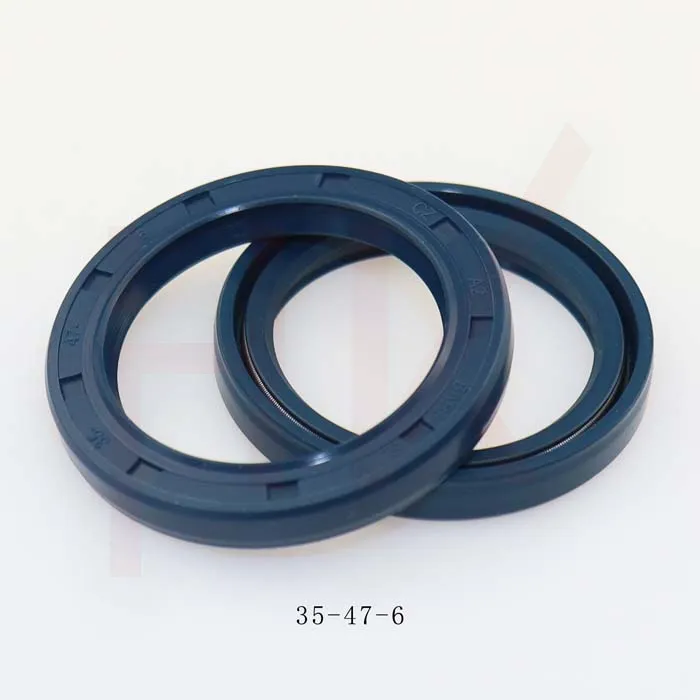
One must appreciate the complexity involved in the engineering and manufacturing of high pressure shafts. These components are often constructed from high-strength alloys capable of withstanding extreme conditions. Such materials include advanced superalloys like Inconel or titanium, chosen for their unique properties like high tensile strength, exceptional temperature resistance, and fatigue durability. Our expertise in metallurgical science ensures these materials are alloyed and machined to the most exacting standards.
Experience has shown that the secret to a high pressure shaft's superior performance lies in its precision engineering. Advanced manufacturing techniques such as electron beam welding and spark erosion are often employed to ensure optimal structural integrity and surface finish. Every shaft undergoes rigorous testing, including ultrasonic inspections and x-ray examinations, to ensure compliance with industry standards and to uphold the trust placed in these components by engineers and manufacturers across various sectors.
high pressure shaft
Trustworthiness in high pressure shafts is further enhanced by investing in research and development. Continuous advancements in computational modeling allow engineers to simulate conditions that these shafts will face over their service life, identifying potential points of failure before they manifest in real-world applications. This approach ensures that the final product is not only trustworthy but also adaptable to unforeseen conditions, much like a seasoned specialist adept in handling emergencies.
A hallmark of authority in this field is the implementation of a robust quality assurance system. From conception to delivery, every stage of shaft production is subject to stringent checks and balances, reflecting our commitment to the highest standards of professionalism and integrity. This rigorous process not only guarantees product excellence but also instills confidence in our clients, knowing their high-pressure applications are supported by components of unwavering quality and performance.
The experience we bring is not only theoretical but deeply practical, drawing insights from industries ranging from aerospace to energy. Aerospace engineers, for instance, rely on high pressure shafts to ensure that aircraft engines operate without fail at cruising altitudes, where the stakes couldn't be higher. Likewise, power generation facilities depend on our shafts to ensure sustainable, uninterrupted electricity supply, underlining the critical role of these components in everyday life.
In conclusion, a high pressure shaft's relevance extends far beyond its immediate mechanical function. It embodies a fusion of advanced materials science, precision engineering, and comprehensive quality assurance methodologies. As industry leaders striving for excellence, our commitment to delivering only the finest products ensures that our high pressure shafts remain unmatched in experience, expertise, authoritativeness, and trustworthiness. By continuing to innovate and adapt, we aim to set benchmarks in the engineering world, one high-pressure application at a time.