Selecting the right oil seal is crucial for ensuring equipment reliability and efficiency. The keyword [14 22 5 oil seal] pertains to a specific size range, revealing significant demand in various industrial applications. Navigating through the world of oil seals requires deep insights into their functionality, materials, and application techniques — fostering experience, expertise, authoritativeness, and trustworthiness.
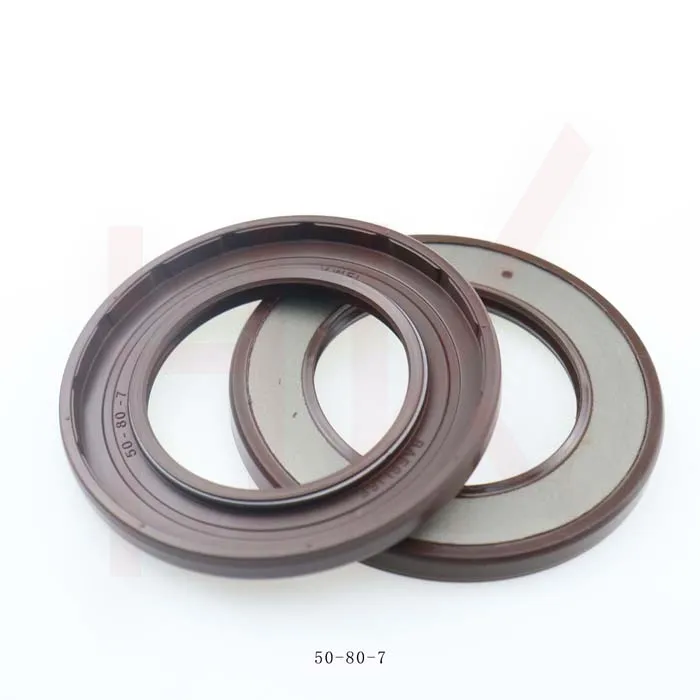
Oil seals, often overlooked, are indispensable components preventing fluid leakage in equipment. They play a key role in blocking contaminants from infiltrating machinery, ensuring that the lubricant remains uncontaminated. Given their importance, understanding specific oil seal dimensions, such as 14x22x5 mm, becomes imperative for optimal performance.
A seasoned engineer or technician knows that selecting a seal involves more than matching sizes. The seal material plays a pivotal role, as it must resist the application's environmental conditions, including temperature, pressure, and the chemical properties of the fluid. Nitrile rubber, fluorocarbon, silicone, and PTFE are commonly used materials, each offering unique benefits. For instance, a nitrile seal may offer excellent oil resistance and affordability, whereas a fluorocarbon seal may withstand higher temperatures and aggressive chemicals.
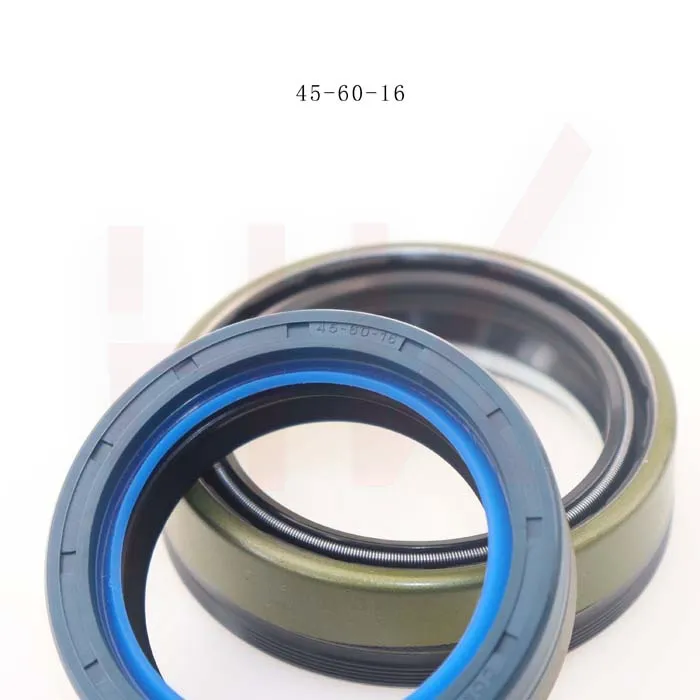
In real-world applications, a 14 22 5 oil seal might be seen in small engines, rotating shafts, or hydraulic systems where space is constrained but reliable sealing is critical. An example is its use in compact mechanical systems within robotics, where precision sealing ensures the seamless operation of sensitive components. Selecting the incorrect seal can lead to catastrophic failures, resulting in costly downtime and repairs.
14 22 5 oil seal
Engaging with a reputable supplier or manufacturer enhances the trustworthiness of oil seal acquisition. Companies that have established themselves as leaders in sealing technology often provide comprehensive guides and expert support. They ensure their products meet stringent quality standards and provide data sheets detailing the seals' technical specifications. This information is vital because it ensures that professionals can make informed choices grounded in accuracy.
Furthermore, the installation of oil seals is a meticulous process that demands specialized tools and techniques. Using an improvised method can damage both the seal and the equipment, compromising the seal's integrity. Experts recommend verifying the shaft and bore dimensions, checking for burrs or sharp edges, and following a cross-checked installation method. The correct alignment during installation fosters enhanced reliability and longevity of the seal's performance.
After installation,
monitoring the oil seal's condition can prevent future issues. Performing routine inspections to check for leaks or wear can highlight potential problems before they escalate. Developing an ongoing maintenance schedule mitigates risk and underscores a commitment to operational excellence.
In conclusion, the choice and application of an oil seal, like the 14 22 5, should be handled with accuracy and care. Collaboration with qualified professionals in the field and adherence to best practice guidelines ensure the highest standards in seal performance. Through understanding the nuanced demands of different applications, one can leverage the unparalleled experience and authoritative guidance to maintain the trustworthiness of any mechanical setup. It’s through this diligent approach that industries can continue to operate smoothly, harnessing the full potential of their machinery.