Oil seals, often overlooked in the grand landscape of machinery components, serve as vital guardians of lubrication systems. These unsung heroes of industrial and automotive applications ensure that lubricants stay where they belong, preventing contamination while maintaining the efficiency and lifespan of equipment. As we delve into the realm of oil seals, we uncover the depth of their importance and the nuances of selecting the right product to enhance performance and reliability.
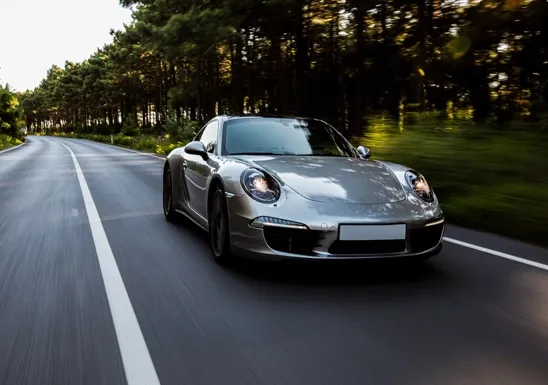
In the world of mechanical components, oil seals, also referred to as rotary shaft seals or radial lip seals, are essential for ensuring that oil does not leak out of the machinery. They simultaneously stop contaminants from getting inside, a dual action that keeps machinery running smoothly. Their applications span across various industries, from automotive to aerospace, and from manufacturing to marine environments. Each of these environments presents different challenges, necessitating the need for expertise in selecting the appropriate oil seal tailored to specific conditions.
Choosing the right oil seal involves a thorough understanding of the operational environment. Temperature, pressure, lubricant type, and the nature of the contaminants to be kept out all play significant roles. For instance, in high-temperature environments, seals made from fluorocarbon elastomers might be preferred due to their ability to withstand elevated temperatures. Conversely, for applications involving exposure to aggressive chemicals, seals made from a robust material like polytetrafluoroethylene (PTFE) offer superior resistance.
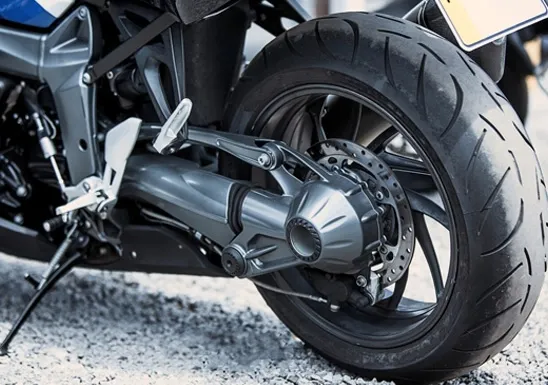
The expertise in oil seal selection also extends to the design and fitment, ensuring a precision fit to prevent leaks. This involves considerations of the shaft and housing dimensions, shaft speed, and the expected pressure. Manufacturers looking to customize oil seals for niche applications should partner with suppliers who possess deep technical expertise and industry knowledge. These suppliers can provide bespoke solutions that not only meet the technical specifications but also enhance operational efficiency.
Moreover, the authority of oil seal manufacturers often stems from their commitment to innovation and quality assurance. Established brands invest significantly in research and development to improve seal performance, often leading to breakthroughs in seal materials and design.
These advancements contribute to extended service intervals and reduced maintenance costs for end-users. Companies that consistently adhere to international quality standards, like ISO 9001, demonstrate a dedication to maintaining high levels of trustworthiness and reliability.
oil seal
Real-world experience also highlights the importance of regular maintenance and inspection of oil seals. Even the most advanced seals can experience wear over time, leading to potential leaks if not addressed promptly. Maintenance personnel should be trained to recognize the early signs of seal failure, such as oil residue around the sealing area or unusual noises emanating from machinery. Timely replacement and adherence to installation best practices are crucial in ensuring long-term machine reliability.
In the realm of product application, case studies and testimonials can act as powerful trust-building tools. Success stories from industries where oil seals have significantly enhanced operational efficiency serve as endorsements of the product’s efficacy. These narratives, particularly when backed by quantitative data showcasing improvements in equipment lifespan or reductions in maintenance downtime, fortify the trust users place in their oil seal solutions.
As machinery continues to evolve, the dynamics of oil seals will adapt to meet new challenges. The seamless integration of technology, such as predictive maintenance sensors that monitor seal condition in real-time, is on the horizon. These technological advancements promise a future where oil seal maintenance is proactive rather than reactive, ensuring even greater reliability and efficiency in equipment operations.
In summary, oil seals are foundational to the performance and reliability of machinery across various industries. Selecting the right seal requires an intricate balance of experience and technical expertise, ensuring that they not only fit the current needs but also adapt as requirements change. Through innovation and a commitment to quality, oil seals will continue to be trusted elements in the machinery of tomorrow.