The TCN type oil seal is an essential component in the world of mechanical engineering and machinery maintenance. Known for its ability to prevent contamination and ensure the longevity of machinery, this specific oil seal plays a critical role in various industrial applications. From its design intricacies to its functional benefits, the TCN type oil seal is a testament to engineering precision and reliability.
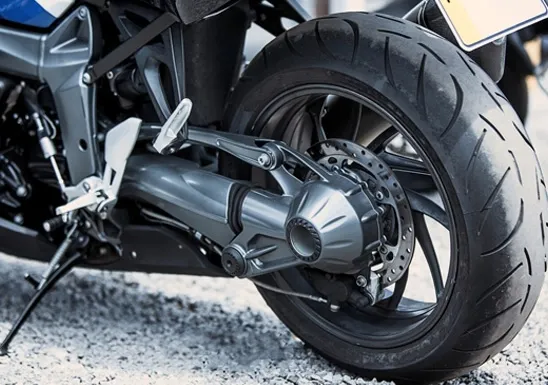
Understanding the TCN Type Oil Seal
A TCN type oil seal is a robust, advanced model that effectively seals lubricants within machinery while keeping out impurities such as dirt and moisture. What sets the TCN type apart from other seals is its specialized construction, typically composed of high-grade rubber and reinforced with inner metal rings. This configuration not only provides superior sealing capability but also guarantees durability and resistance to wear and tear even in extreme conditions.
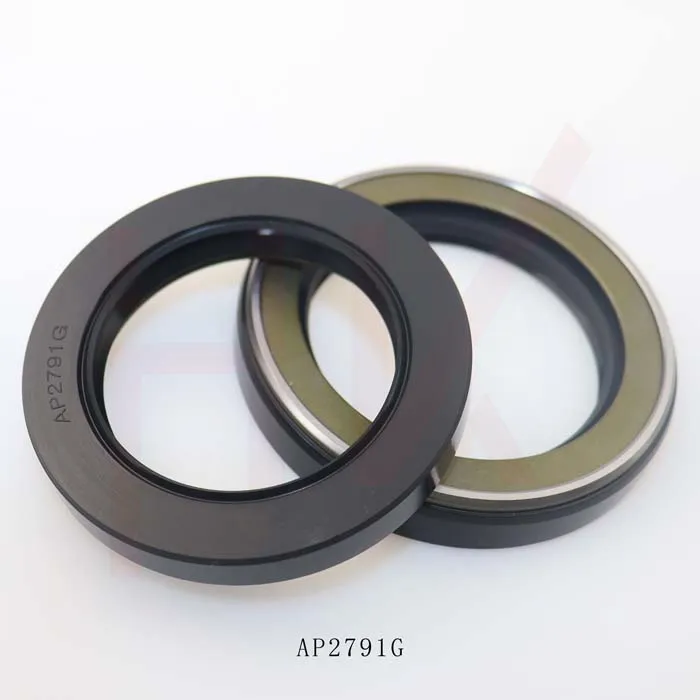
The primary function of the TCN oil seal is to maintain the lubricating oil within a bearing assembly. By preventing oil leakage, it ensures that the machinery operates smoothly and efficiently. Furthermore, by keeping debris and contaminants at bay, it minimizes the risk of mechanical failure, which can result from abrasive particles entering the machinery.
Expertise in Design and Functionality
Professionals in the field of mechanical engineering understand the importance of selecting the right oil seal for their equipment. The TCN type oil seal is engineered to accommodate radial and axial motion while maintaining a tight seal. It features a flexible lip that is in constant contact with the rotating shaft, providing consistent pressure and minimizing the risk of oil leakage.
One of the noteworthy design attributes of the TCN oil seal is its spring-loaded lip. This element enhances the seal’s effectiveness by compensating for any shaft misalignment or dimensional variances that might occur over time. Such a feature highlights the expertise poured into the design of the TCN type, making it a preferred choice for engineers and maintenance professionals alike.
Unparalleled Reliability and Trustworthiness
tcn type oil seal
Industries that require high-performance machinery often rely on the TCN type oil seal due to its reliability. Its ability to function under high temperatures and pressures without degrading is noteworthy, providing confidence to those who manage critical machinery.
The trust placed in these seals stems from rigorous testing and quality assurance measures that manufacturers adhere to. They are often subjected to simulated wear-and-tear scenarios and extreme conditions to ensure that each seal performs as expected once installed. This commitment to quality and performance cements the TCN type oil seal’s position as an authoritative choice in both industrial and commercial applications.
Real-world Applications and Benefits
TCN type oil seals are used extensively across various sectors, including automotive, marine, aerospace, and heavy machinery manufacturing. In these fields, the cost of mechanical failure can be exorbitant, making the selection of high-quality components like the TCN type oil seal even more critical.
For instance, in the automotive industry, these seals are often employed in engines and transmissions, where they play a pivotal role in preventing lubricant leakage that could lead to significant engine damage. In marine applications, where machinery is frequently exposed to harsh environmental conditions, the TCN type’s resistance to corrosion and longevity proves invaluable.
Investing in TCN type oil seals also translates to cost-effective maintenance for industries. Reduced downtime, fewer lubricant top-ups, and lower risk of component replacement all contribute to more efficient operations and significant cost savings over time.
In conclusion, the TCN type oil seal represents the pinnacle of engineering effectiveness, blending expertise, reliability, and trustworthiness into a single product that serves as the backbone of efficient machinery operation. Its thoughtful design and proven performance make it an indispensable element in ensuring that industrial machinery continues to operate smoothly and efficiently, securing its status as a critical component in contemporary mechanical systems.