In the world of industrial machinery and automotive maintenance, the term oil seal often surfaces, yet it remains misunderstood by many. One specific type — the 35 72 10 oil seal — has garnered attention for its crucial applications and reliability. Let’s delve into a comprehensive exploration of this remarkable product, emphasizing its applications, functionality, and its vital role in ensuring efficient machinery operation.

Oil seals, also known as rotary shaft seals, are instrumental in preventing the leakage of lubricants from components, safeguarding mechanical systems from contaminants like dirt, dust, and moisture. The 35 72 10 oil seal stands out as a medium-sized seal with specific dimensions; 35 mm inner diameter, 72 mm outer diameter, and 10 mm width. These specific measurements make it an ideal choice for use in numerous industries, including automotive and heavy machinery.
The durability of the 35 72 10 oil seal can be ascribed to its robust construction materials. Typically manufactured from nitrile rubber or fluoroelastomer, these materials offer excellent resistance to oil, hydraulic fluid, and extreme temperatures. This ensures the oil seal's performance remains uncompromised, even in harsh environments and demanding applications.
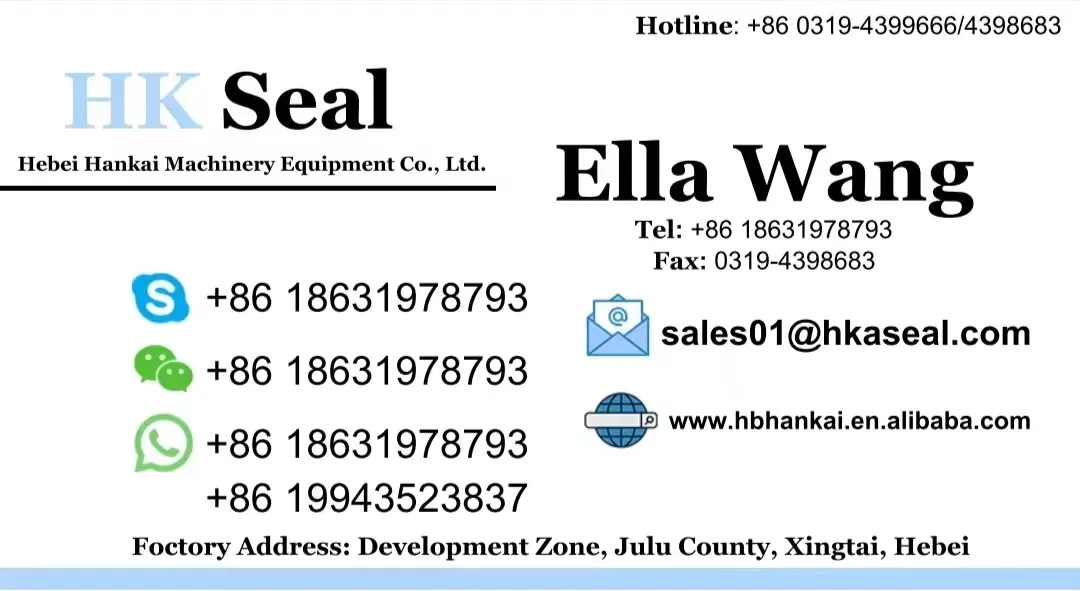
Expertise in installing oil seals like the 35 72 10 is critical. Proper installation involves ensuring the shaft is clean and free of debris, as well as applying a thin layer of lubricant to aid the fitting and reduce friction. Failure to adhere to these guidelines may result in premature wear or failure, which could lead to costly repairs or downtime.
The 35 72 10 oil seal is a paragon of reliability, making it indispensable in the automotive sector. Commonly found in engines, transmissions, and differentials, it acts as a guardian, maintaining vital lubrication within parts that run at high speeds and high pressure. In heavy machinery, oil seals of this specification are crucial in preventing leaks in pumps, compressors, and hydraulic systems, all of which require strict operational efficiency to maximize output and longevity.
35 72 10 oil seal
Trustworthiness and authority in the manufacturing process are paramount for oil seals. Reputable manufacturers undergo rigorous quality control processes to ensure that each product meets stringent industry standards. Certifications such as ISO 9001 validate a manufacturer’s commitment to quality and can provide customers with peace of mind regarding the reliability of the 35 72 10 oil seal.
Further enhancing its reputation is the oil seal's ESS—experience, specificity, and security. The extensive experience that manufacturers and distributors bring to the table translates into better product design and customer support, ensuring that users have the necessary tools and information to select the right seal for their needs. Specificity, in terms of dimensions and material composition, ensures compatibility with a wide range of machinery, while security denotes the product’s capacity to offer long-lasting protection against leakage and contamination.
Investing in high-quality oil seals can significantly reduce maintenance costs and extend the life of machinery. By keeping components well-lubricated and free from external contaminants, the 35 72 10 oil seal plays a critical role in maximizing the operational efficiency of equipment. It helps minimize the risk of breakdowns, ultimately ensuring that businesses maintain productivity and profitability.
In conclusion, the 35 72 10 oil seal exemplifies the intersection of engineering excellence and practical application. Its precise dimensions and high-quality materials make it indispensable across various sectors, from automotive to heavy machinery. Its role in safeguarding systems, enhancing efficiency, and reducing downtime cannot be understated. For businesses and engineers seeking reliability and robustness, the 35 72 10 oil seal remains a trusted component, securing its position as a preferred choice in the field.