In the world of mechanical engineering and industrial applications, sealing rings are an unsung hero. These simple yet crucial components ensure the smooth operation of countless machines and systems, from automobile engines to sophisticated robotics. Understanding the importance and intricacies of sealing ring kits is not just beneficial; it’s essential for anyone involved in maintenance, manufacturing, or engineering.
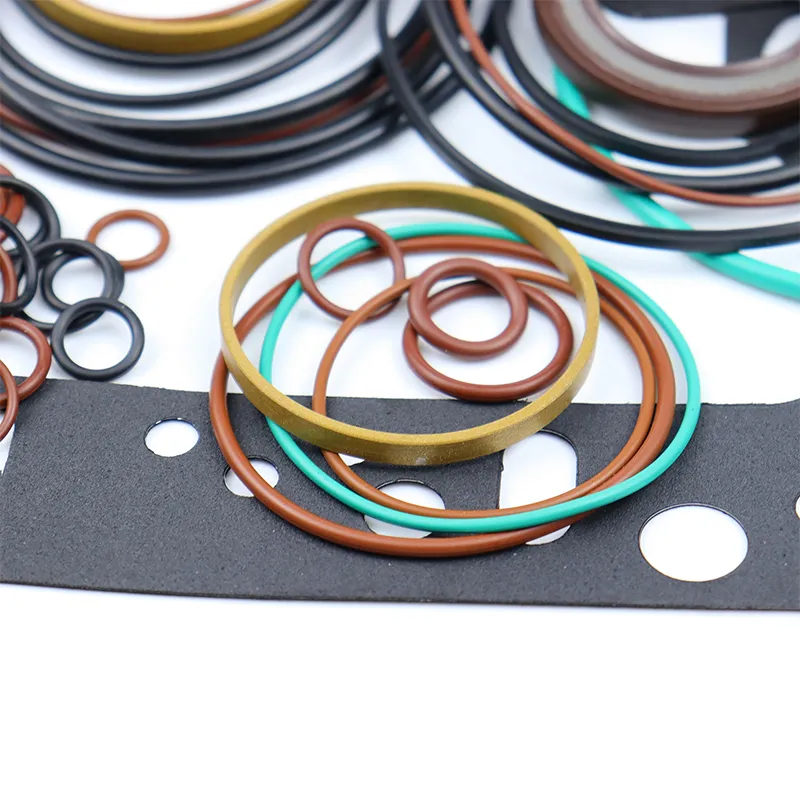
Sealing rings are used to prevent leaks, maintain pressure, and separate fluids in systems that require reliable performance under challenging conditions. These rings are integral to minimizing wear and tear, avoiding costly breakdowns, and ensuring efficiency. A sealing ring kit typically includes an assortment of O-rings, gaskets, and other seal types used in machinery maintenance and repair tasks.
Selecting the right sealing ring kit isn’t a straightforward task. It requires expertise and understanding of various parameters such as temperature, pressure, and chemical exposure. Materials are a significant factor; common materials include rubber, silicone, PTFE, and metal. Each has unique properties that must align with the application's demands.
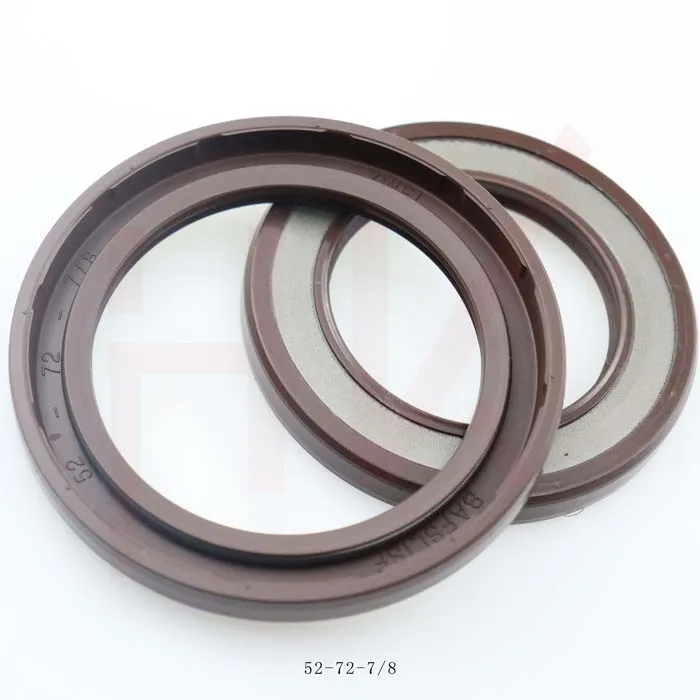
For instance, in applications subjected to high temperatures, such as automotive engines, silicone and PTFE seals offer high heat resistance. For environments with chemical exposure, EPDM (Ethylene Propylene Diene Monomer) demonstrates excellent resistance. Selecting the wrong material can lead to premature failure, leading to costly downtimes and repairs.
A well-curated sealing ring kit offers versatility and convenience. It allows technicians to perform on-site maintenance without delays, catering to a range of applications. This convenience serves as an invaluable asset, particularly in industries where time is of the essence. Aerospace or automotive industries, for instance, heavily rely on immediate solutions to avoid disruptions in assembly lines or critical systems.
sealing ring kit
Ensuring the longevity and reliability of systems, sealing ring kits are pivotal for industries that demand precision. Choosing a kit from a trusted manufacturer guarantees that each piece has undergone rigorous testing and quality checks. When a sealing ring is applied, its accuracy is paramount; even a slight deviation can lead to leaks or system failures. Manufacturer certifications and adherence to industry standards are concrete indicators of quality and reliability.
Installation of sealing rings necessitates attention to detail and expertise. Incorrect installation can damage the ring or the joint it is meant to secure. It is crucial that installers are well-trained, understanding the nuances of fitment, lubrication, and torque specifications. Experienced technicians recognize the signs of improper seal use, such as uneven wear patterns or leakage, which helps in diagnosing and rectifying potential issues before they lead to significant disruptions.
Additionally, maintaining a comprehensive database on each component within a sealing ring kit is invaluable for processing replacement requests and managing inventory efficiently. Investing in digital tools and software that tracks usage, installation history, and performance metrics can significantly streamline maintenance workflows and reduce operational costs.
In advanced applications, high-tech solutions such as sensor-equipped seals are becoming more prevalent. These seals can provide real-time data on their condition and the operating environment, alerting users to potential issues before they evolve into failures. Innovation in sealing technology continuously drives industries toward increased reliability and performance, making the selection of sealing ring kits an evolving challenge for engineers.
In summary, when it comes to sealing ring kits, expertise, and careful selection make all the difference. These kits are not mere afterthoughts but pivotal components that ensure the safety, efficiency, and longevity of machinery across diverse industries. Investing time in understanding the specifications, selecting the right materials, and ensuring proper installation can prevent costly failures and drive operational success. Engaging with reputable suppliers and continuously updating knowledge on technological advancements will keep companies ahead in the competitive landscape, ensuring machinery performs at its best.