Oil pump seals are critical components that ensure the efficient operation of various machinery and engines. Their importance in maintaining the seamless flow of oil and preventing leakage cannot be overstated. Understanding the intricacies of oil pump seals not only highlights their mechanical significance but also underscores the expertise required to select and maintain them properly.
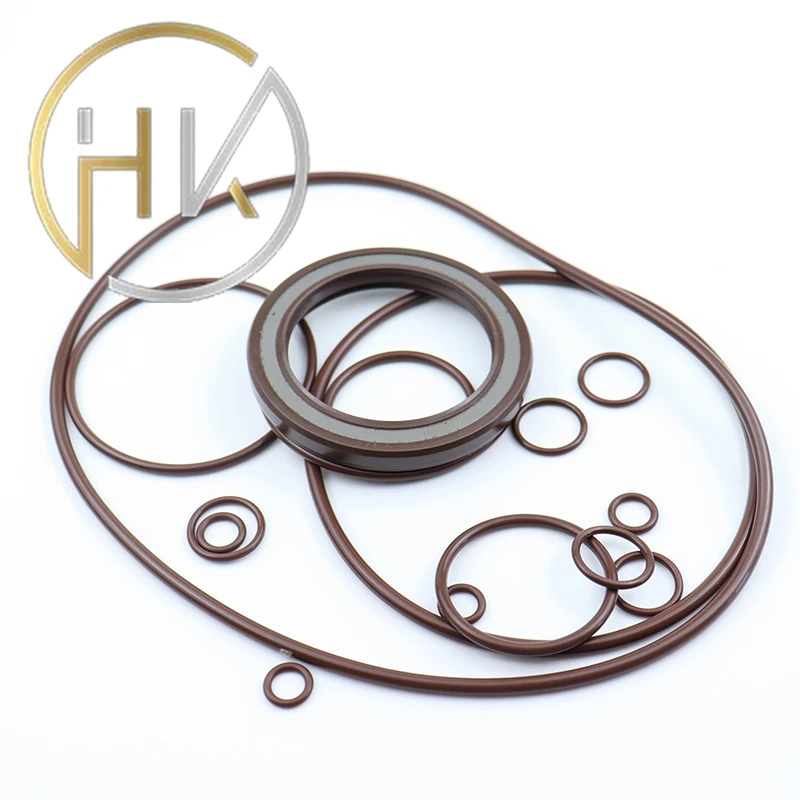
The primary function of an oil pump seal is to create a barrier that retains lubrication within the oil pump system while keeping contaminants out. This is crucial for the proper functioning of engines, as any oil leakage can lead to severe mechanical failures. Over the years, advancements in material science have led to the development of seals that can withstand higher pressures and temperatures, further emphasizing the need for expertise in selecting the right seal for specific applications.
Choosing the right oil pump seal hinges on understanding the specific requirements of the machinery it will serve. Factors such as temperature range, pressure levels, and the type of oil used play a vital role in determining the suitable type of seal. Various types of seals, such as rotary seals, lip seals, and mechanical seals, are available, each designed to handle specific conditions and requirements. Expertise in mechanical engineering and material science is essential to navigate these choices effectively.

Proper installation and maintenance of oil pump seals are just as critical as selecting the right seal. Misalignment during installation, incorrect sizing, or material mismatch can lead to premature seal failure, resulting in costly repairs and downtime. Ensuring that installation follows the manufacturer's recommended procedures and using the correct tools can prevent such issues. Regular inspections for signs of wear and tear, such as cracks or deformities, can help in timely replacement, thereby mitigating risks of leakage.
oil pump seal
Specialists with extensive experience in machinery maintenance often recommend using seals made from modern materials like Viton or PTFE, which offer enhanced resistance to heat and chemical degradation. These materials' inherent properties make them ideal for high-performance environments, extending the lifespan of the seal and reducing maintenance costs.
In industries where oil pump systems are integral to operations, adhering to rigorous standards and specifications for seal selection and maintenance is vital. Consulting with manufacturers and utilizing their expertise can ensure compliance with industry standards and enhance the trustworthiness of machinery operations. Manufacturers often test their seals under stringent conditions to certify their reliability, providing an additional layer of assurance for end users.
Moreover, the role of technology in refining oil pump seal design cannot be overlooked. Computational simulations and finite element analysis are cutting-edge techniques used to predict seal performance under different operating conditions. These methodologies require a high level of expertise but offer invaluable insights that traditional testing might overlook. By leveraging such advanced tools, businesses can significantly enhance the reliability and efficiency of their oil pump systems.
To bring this all together, an investment in high-quality oil pump seals and their proper maintenance is an investment in the longevity and efficiency of engines and machinery. Relying on expert advice and aligning with best practices in installation and inspection will not only optimize performance but also instill confidence in both operators and stakeholders. As the demand for precision and reliability in industrial operations continues to rise, so too does the necessity for authoritative guidance and trustworthiness in the selection and handling of essential components like oil pump seals.