High pressure lip seals offer critical solutions across various industries requiring exceptional sealing capabilities under demanding conditions. These seals are specially engineered to withstand elevated pressures, rigorous environmental exposure, and the demanding operational parameters often found in such applications. Their utility stretches from aerospace to power generation, oil and gas, to automotive industries, each demanding bespoke solutions.
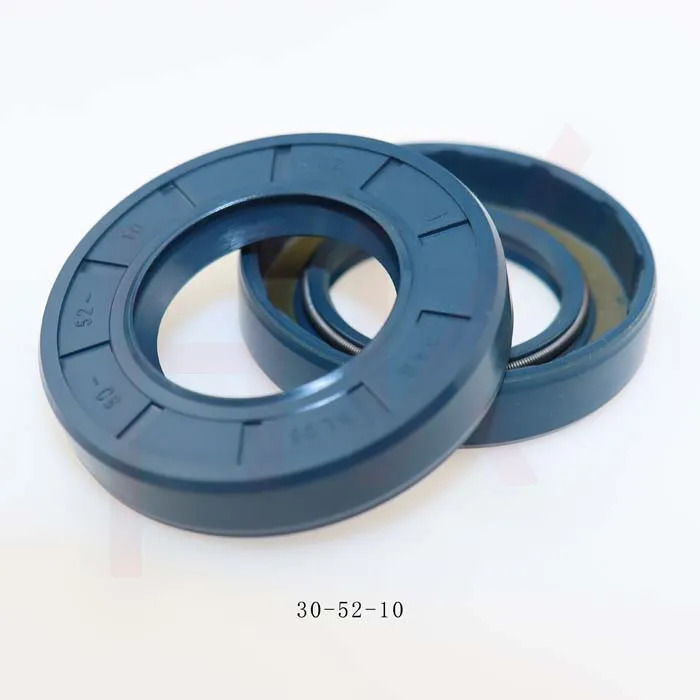
The hallmark of high pressure lip seals is their sophisticated design and material composition. Engineered from advanced polymers, elastomers, and rubber compounds, these materials are selected based on the specifications of the job they need to perform. For instance, polytetrafluoroethylene (PTFE) and fluorocarbon compounds are frequently utilized for their superior temperature tolerance and chemical inertness. This assures that the seals remain durable under temperature fluctuations ranging from sub-zero climates to extreme heat conditions, without degradation, thus extending operational life and reducing replacement frequency.
The expertise employed in designing these seals involves an intricate understanding of fluid dynamics and thermal properties. Manufacturing processes further incorporate precision engineering to fabricate seals that can sustain high pressure loads without succumbing to material fatigue or failure. The precise lip design ensures optimal contact pressure and distribution across the sealing surface, a critical factor when aiming to minimize leakage paths under high-pressure environments.

Real world applications underscore the extensive expertise deployed in the production and utilization of high pressure lip seals. For instance, in aerospace hydraulics, these seals are entrusted with maintaining the integrity of systems crucial to aircraft operation and safety in extreme conditions. The design expertise contributes to aircraft components that are lighter, more efficient, and above all,
reliable.
high pressure lip seal
The authoritative understanding of seal dynamics and materials ensures these components operate flawlessly within safety specifications. Manufacturing companies specializing in seal technology undergo rigorous testing regimes and certifications to validate the performance of their seals under simulated operational conditions. As such, industry standards and quality certifications, such as ISO or ASTM, are meticulously adhered to, instilling confidence in end-users regarding the products' reliability and safety.
In the realm of trustworthiness, transparency in manufacturing processes and consistent delivery of proven performance data are crucial. Customers rely on documented evidence of quality control measures, testing standards, and case studies demonstrating seals' performance under real-world conditions. Expert consultation during the selection process further enhances trust, enabling clients to work closely with engineers to select tailor-made solutions that fit their specific applications.
Sustainability considerations and innovations continue to influence high pressure lip seal development. As industries move toward greener operations, the demand for seals that minimize environmental impact by reducing leakage and extending component life grows. Manufacturers are researching alternative materials and developing seals that integrate seamlessly into environmentally-friendly systems without compromising on performance.
In a rapidly evolving industrial landscape, the authority and trust that come with selecting the right high pressure lip seal cannot be overstated. The commitment to expertise, innovation, and endurance in adverse conditions signals industry leadership, proving indispensable for operations that cannot afford failure. By adhering to such stringent standards and remaining at the forefront of seal technology, manufacturing partners ensure the reliability and efficacy that clients depend on, thereby cementing their place as essential contributors to industry success.